Предлагаю вашему вниманию страницы из неизданной книги «Выбор пути. По страницам истории конструкторской мысли». Книга была подготовлена к печати осенью 2008 года. Материал передала в Музей КАМАЗа Кимерал Аида Рафаиловна.
Стабильность – признак мастерства….
Есть еще одна «вечная тема» в истории конструкторской мысли КАМАЗа. Это кабина, по которой КАМАЗ узнают всегда и все – профессионалы и случайные люди, в России и за границей.
Годы шли, сменялись модели и целые семейства камских грузовиков, но кабина оставалась практически такой же. Сделаем сразу смелое заявление. Недостатки кабины КАМАЗа, которые стали притчей во языцех – на самом деле продолжение ее достоинств. Оборотная сторона ее универсальности и экономичности, в точности по старой испанской пословице – «Господь сказал: бери, что хочешь, но плати». Потому что кабина эта была создана «для всего», одна для всех моделей и случаев, для всей гаммы челнинских автомобилей. Для спецнадстроек, у которых кран должен лежать на крыше, и для лесовозов, и для армейских машин. Ведь даже то, что у нее до недавних пор вместо одного панорамного были два плоских стекла – требование военных…
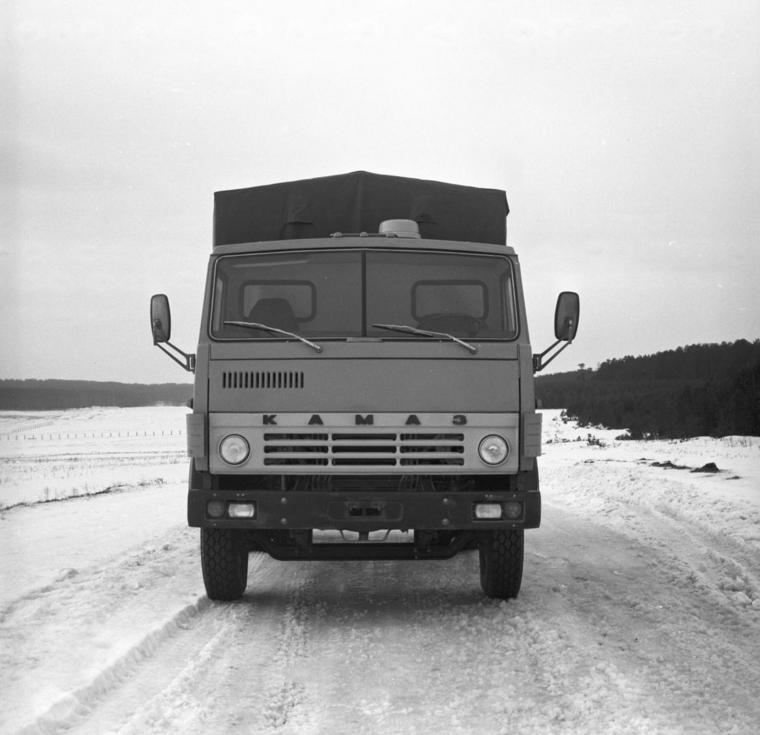
С позиции министерства все было просто и понятно – отличная вещь, универсальная, главное, не надо ничего трогать. Повторялась до боли знакомая ситуация: МАЗу можно делать панорамные стекла, КАМАЗу – нельзя… При этом панорамное стекло, вопреки общему мнению, практически не увеличивает обзорность, то есть реальный эффект от него оценить сложно. А с точки зрения чистой экономики плоские стекла выгоднее. Между прочим, в Америке до сих пор (прим. 2008 год) множество грузовых автомобилей щеголяет плоскими стеклами. История камазовской кабины была интересной и непростой.
Бескапотные грузовики в СССР в начале 70-х делали в Горьком (ГАЗ-66), Кутаиси («Колхида») и Минске – МАЗ-500. Дизайн минской кабины профессионалы ехидно назвали «беременная барышня с фартуком».
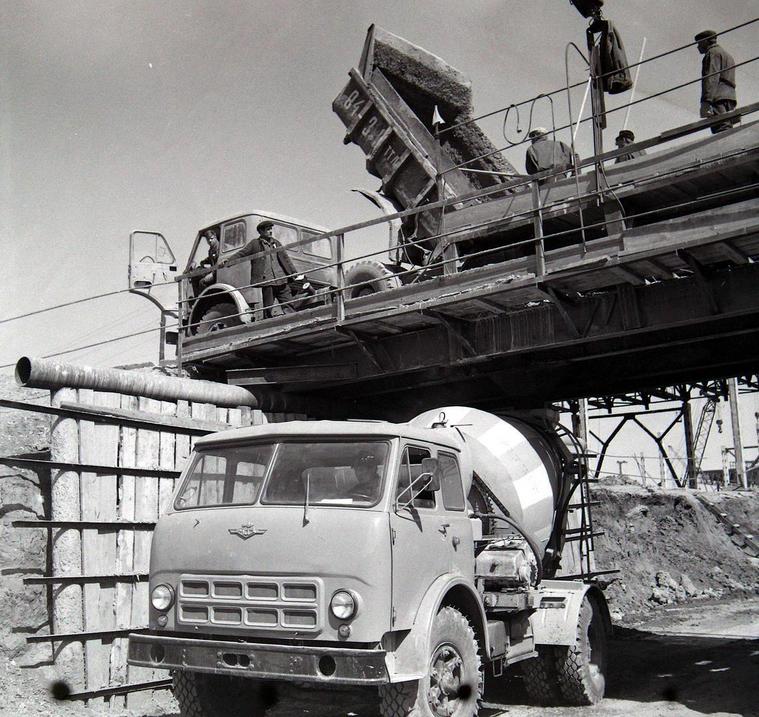
Не удивительно, что минчане больше не стали рисковать на эстетическом поприще и для следующей машины попросту использовали кабину шведской Scania. Разработчиком нового грузовика, как мы помним, министерство назначило ЗИЛ, у которого бескапотник был только в проекте.
За основу кабины КАМАЗа и взяли то, что готовили для нового ЗиЛ-170. Занималась этим группа под руководством зам.главного конструктора ЗиЛа Виталия Борисовича Певцова. Габариты были непривычны, эргономику бескапотной кабины никто детально не изучал. Так что, когда пришел приказ отдать наработки будущему КАМАЗу, это вызвало у зиловцев скорее облегчение – облик своих машин удалось сохранить, от «нелюбимого дитяти» избавились. А для коллег – пожалуйста, можно и поработать под заказ.
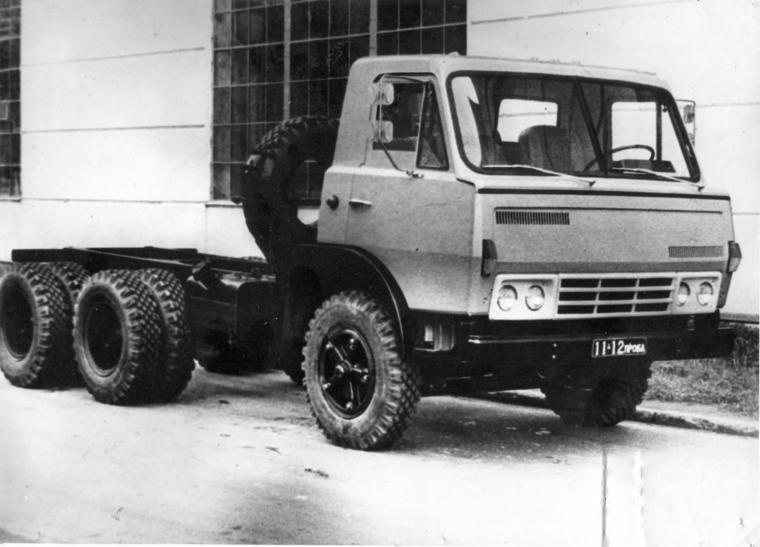
На заводе была сильная дизайнерская группа, занимавшаяся правительственными лимузинами ЗиЛ-114. Им и поручили разработку кабины – может быть, потому она получилась такой прямоугольной (фирменный стиль не вытравишь!). Проектирование вели первоначально без серьезного анализа зарубежного опыта, часто искали решения на ходу. Последнюю версию дорабатывал Лев Самохин.
Одна из проблем была вот в чем. Создать современный автомобиль невозможно без развитого производства компонентов. Электрика, пластмассы, резины, формованные уплотнения и многое другое – все это требует специальной конструкторской и технологической проработки. А в то время большинство советских автозаводов недалеко ушли от «натурального хозяйства», большую часть номенклатуры изготавливали у себя.
Крупные заводы, специализирующиеся на выпуске комплектующих для автомобилей, по сути, и появились-то в СССР только благодаря ВАЗу. При проектировании КАМАЗа на них рассчитывать было еще невозможно.
Отсутствие таких внешних ресурсов, а значит, и опыта проектирования в этой области, неизбежно приземляло разработчиков. В том же направлении действовала позиция заказчика - министерства.
Конструкторам рекомендовали обходиться без роскоши: лишь бы водителю было тепло (все-таки осваивать предстояло Сибирь). А комфорт, эргономика – это излишества. Поэтому кабина большегруза получилась архипростой, даже аскетичной.
Вместо мягких панелей в салоне появились жесткие стальные, упростилась обивка дверей. Цельнолитые панели из вспененных полимеров на отечественных легковушках тогда уже появились, но применять их на грузовиках никто не собирался – штампованные стальные панели стоили намного дешевле.
Платой за экономичность стали низкая, даже по меркам того времени, термо- и шумоизоляция, примитивные сиденья, недостаточный обзор. Первые образцы кабины дребезжали, все звенело и гудело. Нужно было снижать шум, работать над эргономикой и комфортом, улучшать размещение приборов.
Тогда решили поискать готовых решений за рубежом. Естественно, возникла знакомая трудность – масштабы производства. С учетом поставок в запасные части, кабин надо собирать до 1000 штук в день! Гибкое производство с универсальными сварочными роботами при таких объемах будет очень дорогим.
И советская сторона искала технологию, при которой все процессы распадаются на простейшие «кубики» – жесткие линии, в которых не предусматривалось даже возможности переналадки.
Закладывали-то всего два типа кабин: со спальным местом и без, которые можно было бы делать на одной линии. При таком подходе оборудование будет стоить раз в пять дешевле, но где его взять?
Как мы помним, никто в мире не делал столько одинаковых грузовиков… А вот с кабиной повезло.
Как раз тогда голландский DAF, немецкий Magirus, французские Renault и Unic решили пожертвовать индивидуальностью ради снижения издержек. И заказали… одну кабину на четверых.
Грузовик каждый делал сам, а вот кабину, точнее – ее силовой каркас, для этого «Клуба четырех» предполагалось выпускать на одном заводе.
Отличаться они должны были несущественными внешними элементами. Благодаря такой кооперации суммарный объем выпуска получился серьезный. Технологическое оборудование консорциум заказал во Франции, у одного из лидеров – компании SIAKI, разработчика сварочных линий для массовых легковых автопроизводств.
На эту же фирму вышла и закупочная комиссия КАМАЗа. Французы с удовольствием предложили советской стороне разработать аналог того, что делали для «Клуба четырех». Кабина европейского развозного грузовика была небольшой, и на удивление совпала по габаритам с тем, что требовалось КАМАЗу. Совпадало и еще одно граничное условие. Главным критерием «Клуба четырех» была дешевизна, и малая материалоемкость (в первую очередь – по металлу) играла нашим проектировщикам на руку.
Оставалось решить единственную задачу - конструктивно приблизить камазовскую кабину к проекту «клубной», добиться минимального количества деталей и точек сварки. В этом случае SIAKI готова была пойти на существенную уступку в цене.
С учетом предложений французской стороны, в проект вносили изменения под современные мировые технологии: оборудование для производства «клубной» и челнинской кабины французы разрабатывали и делали практически одновременно.
В результате челнинские конструкторы создали уникальную кабину - с точки зрения технологичности производства на автоматических сварочных линиях. Конструкторские решения этой кабины были на очень высоком техническом уровне. Притом, что в любой кабине огромное количество деталей, удалось обойтись минимумом сварных точек.
Итоговая себестоимость операций по сварке-сборке кабины КАМАЗа составляла… 14 (четырнадцать) рублей, при себестоимости всей машины в 10-11 тысяч.
Так были одновременно созданы и конструкция, и технологическая линия для ее сборки – идеально соответствующие друг другу. Оборотной стороной этого соответствия и высокой производительности сварочного оборудования было то, что внесение малейшего изменения требовало остановки ВСЕЙ линии.
Да что там конструкторские новации – любой ремонт становился катастрофой! В общем, получилось то, что обычно происходит в дикой природе. Если вид идеально адаптирован к одной конкретной среде, жизнь его легка и приятна – но зато крайне опасным становится изменение этой среды.
Таким образом, в основе конструкции кабины КАМАЗов менять можно было немногое. Поэтому фокус внимания конструкторов и дизайнеров смещался на внешние элементы.
В результате часто получались «аномальные» разработки – иногда действительно перспективные и оригинальные, иногда курьезные. Например, зиловские конструкторы спроектировали двери накладными – так, что они ступенькой ложатся снаружи. Это не слишком удачное решение сохранялось долгое время, пока не стали делать подштампованные стенки кабины – и двери, наконец, встали заподлицо.
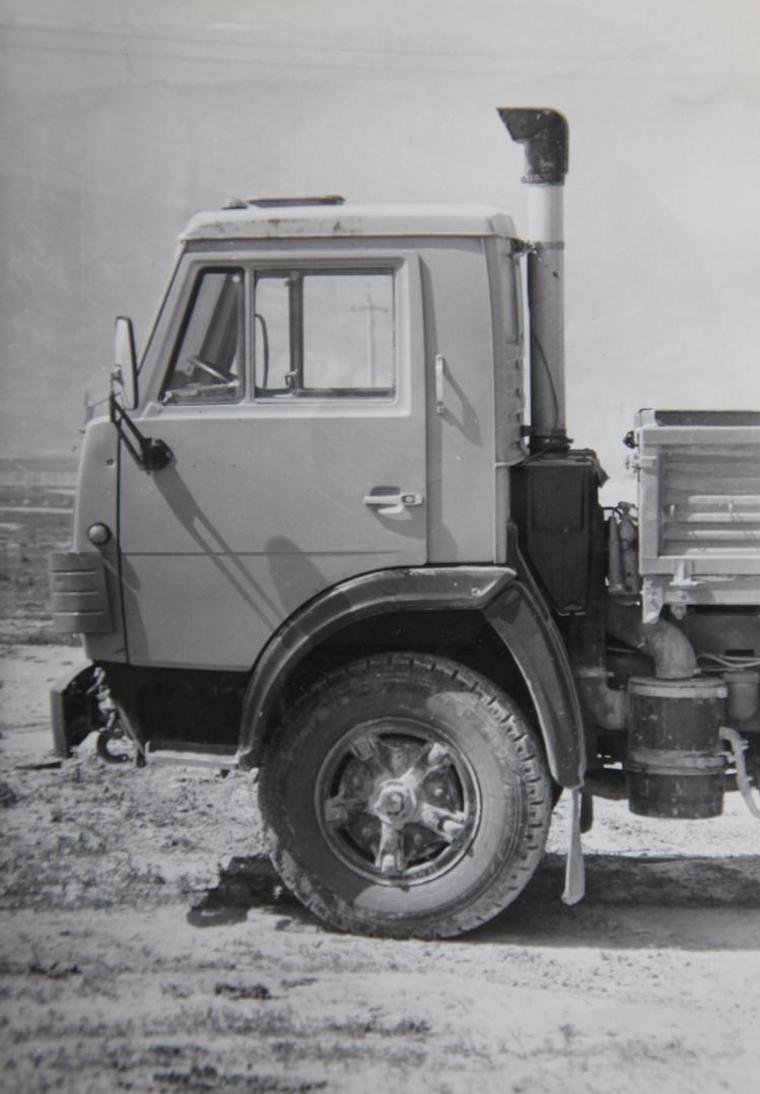
А было и «альтернативное» предложение, причем недавно – не меняя саму кабину, ставить на нее специальные декоративные накладки вровень с плоскостью двери... Не приняли, но вариант такой рассматривали.
Неожиданный способ сделать кабину гладкой появился, когда приступили к созданию магистрального тягача 6410. Внизу на фотографиях первый (в цвете) и второй образцы автомобиля КАМАЗ-6410.
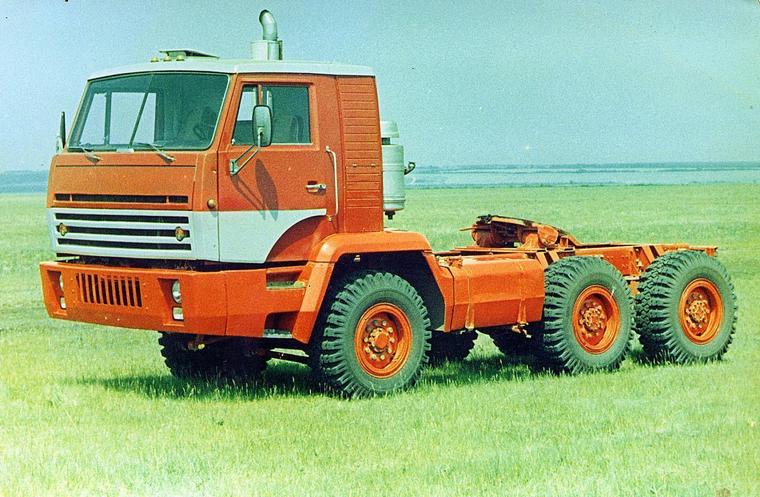
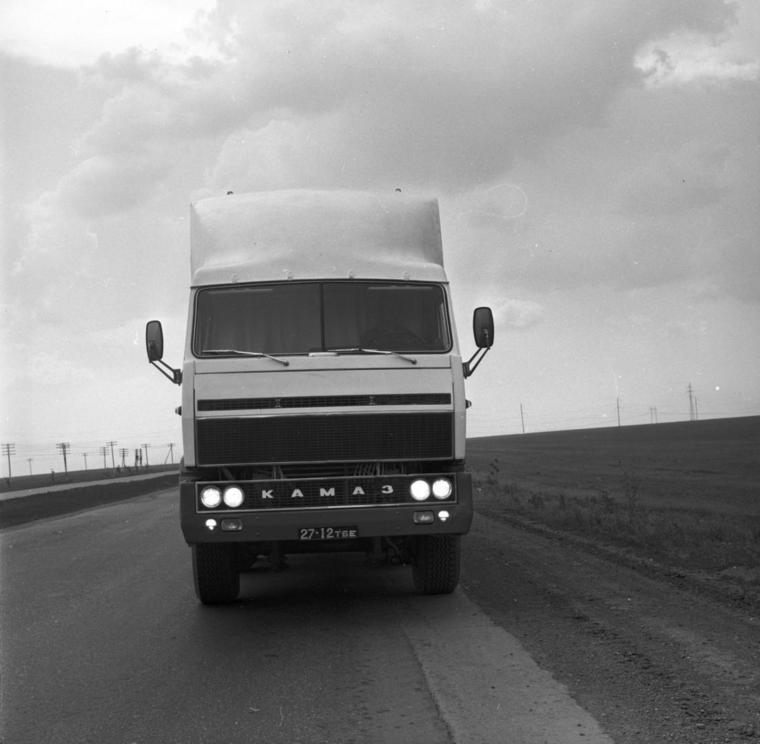
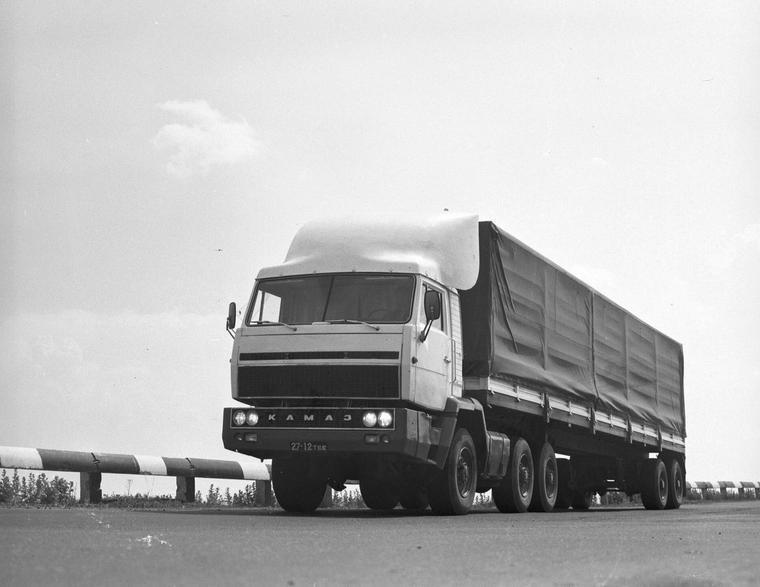
Ему сначала проектировали как раз такую большую и просторную кабину, о которой все мечтают. И чтобы она была обтекаемой, взяли и разместили двери … сзади. Ступеньки там сделали, и даже объяснение придумали – так, мол, водителю удобнее будет.
В обычной кабине он открывает дверь с правой стороны, а там ведь другие машины по дороге едут – его могут сбить. А тут он спокойно вышел назад, можно осмотреться, куда сойти: хочешь - на ту сторону, хочешь - на эту. Все совершенно безопасно и очень удобно... В серию, конечно, тоже не пошло.
Подобного рода изыски никогда не умирали. Разумеется, было и множество серьезных, перспективных идей. Например, Сергей Варламович Екимов, еще на КАМАЗе, запатентовал идею, которая потом легла в основу многих современных концептов – автомобилей будущего.
По его расчетам оказалось, что минимальное сопротивление имеет кабина без углов, описанная радиусом. Сейчас такие уже делает «Исудзу», многие другие. На КАМАЗе все было не только рассчитано, но и проверено – продуто в аэродинамической трубе на КАИ.
Екимов на этой основе сделал несколько дизайнерских проработок – сначала на КАМАЗе, потом уже в собственной фирме «Автодизайн».
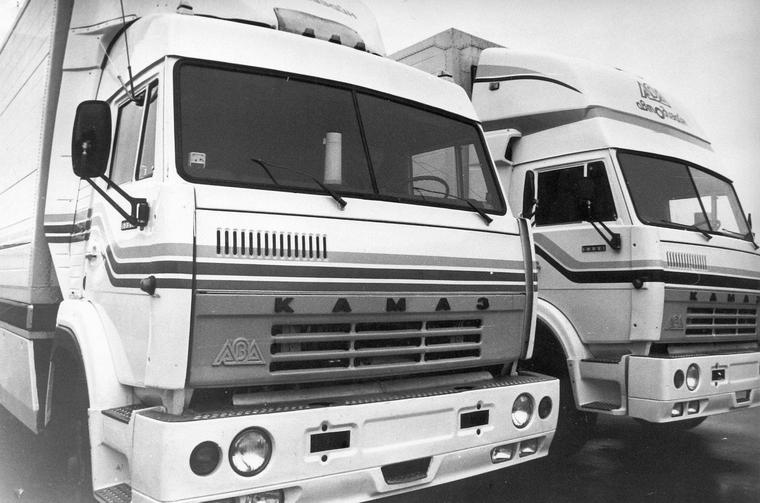
Есть очень интересные эскизы 1986 года: с круглой кабиной и покатой крышей. Если их сравнить с современными ДАФами, «Исудзу» - одинаковый подход очевиден, только в Челнах его придумали больше двадцати лет назад. Покатая крыша - тоже оригинальная камазовская разработка. Когда в аэродинамической трубе продували, решили заодно проверить: как меняются свойства кабины, если варьировать угол наклона верха?
Оказалось, что популярные «лбы» - обтекатели - это не очень аэродинамично, вопреки общему мнению. Машина с крышей, у которой угол наклона около 10°, ведет себя лучше - проявляется интересный эффект. На машине с обтекателем поток отклоняется вверх, и скорость у него становится все выше и выше по мере перетекания на крышу, а давление в нем все ниже и ниже – обыкновенная аэродинамика, как на крыле самолета. В зону самого низкого давления, на крышу, возникает подсос снизу вверх, вдоль боковых стенок кабины и кузова.
Этот поток, вместо того, чтобы протекать горизонтально, по кратчайшей линии, движется по кривой, длина которой в полтора раза больше. А трение, как мы знаем, пропорционально длине пути.
Кроме того, за кормой образуются мощные вихри, это тоже ведет к немалым потерям. А если наклон минимальный, кабина просто раздвигает поток, минимизируя перетоки и вихреобразование.
Оба решения остались на будущее – до тех времен, когда можно будет строить другие кабины, а не перелицовывать старую конструкцию.
Когда пошли разработки для левостороннего движения, на экспорт, появилась и такая смелая мысль. Зачем вообще делать два варианта кабин – левый и правый, когда можно место водителя просто разместить посередине?
Это, конечно, осталось на уровне идеи, а потом появились иностранные концепты с таким подходом – у знаменитого дизайнера Луиджи Коллани, например. Там тоже в серию не идет, но по другим причинам - посередине кабины моторный тоннель, над ним трудно что-то разместить. А с нашей особой конструкцией кабины это было бы очень легко.
Отдельная эпопея – концепт «Айсберг», совершенно аномальная конструкция. Вот когда камские проектировщики, как сейчас говорят, «оторвались по полной», и сотворили с кабиной все, что можно: и двухуровневой ее сделали, и водителю подняли верх, душ и кухню встроили. Полная гостиница на колесах, в общем.
Вернемся, однако, к истокам. Кабину сделали, производство запустили. Внизу на фотографии, первая кабина, изготовленная на прессово-рамном заводе 19 декабря 1975 года.

Но едва только первую собранную машину с этой кабиной выкатили на дорогу, как выяснилось, что она – страшная грязнуля! Если на дворе малейшая сырость – вокруг автомобиля на ходу возникало прямо-таки облако грязи. Ехать невозможно: зеркала мутные, через открытое окно все залетает внутрь.
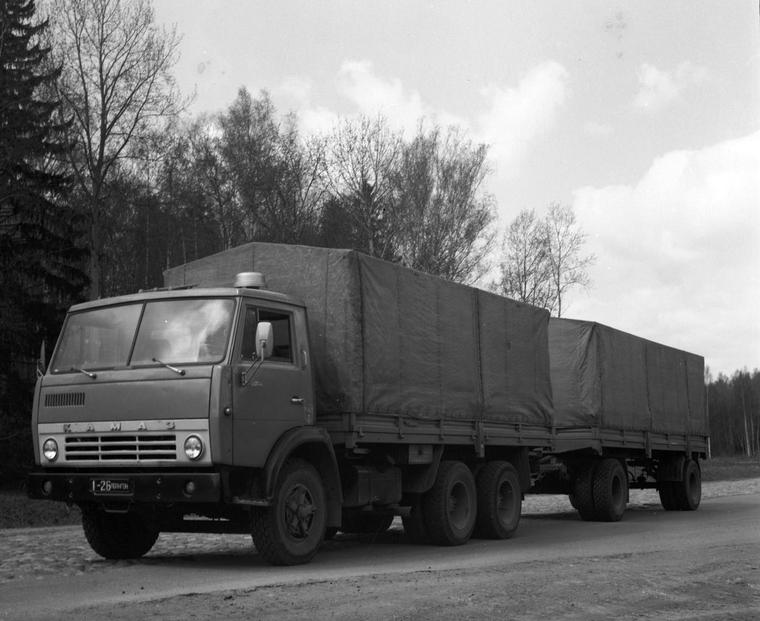
С другими советскими машинами такого не было - вероятно, дело в форме кабины?
На Западе внешние обводы грузовиков уже тогда на стадии разработки обязательно «продували» в аэродинамической трубе. У советских автомобилестроителей такой практики не было, с КАМАЗов и начали исследовать аэродинамику грузовика.
Базу для исследований нашли быстро. В столице Татарии, всего в 250 километрах от Набережных Челнов, находится КАИ, а у него в распоряжении - собственная аэродинамическая труба.
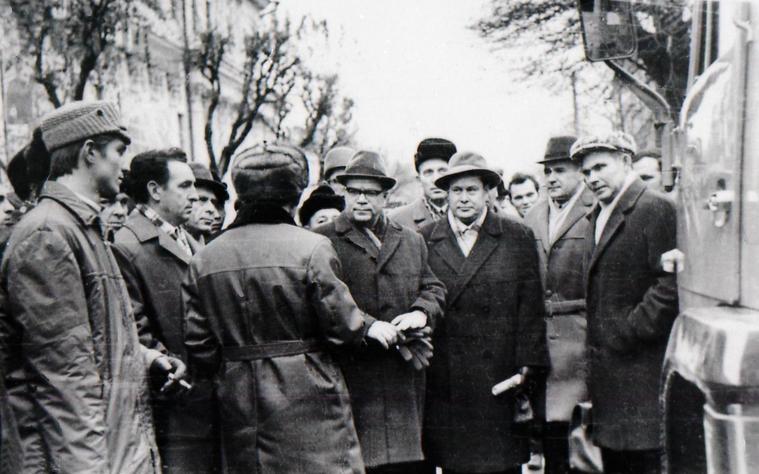
Сотрудничество с КАИ оказалось плодотворным. Выяснилось, что при движении автомобиля происходил срыв потока, завихрение, и все из-под колеса (а колесо располагается как раз по «оси» сидения) немедленно засасывалось в зону отрицательного давления, оказавшуюся именно у окон, дверей и зеркал заднего вида.
Поток воздуха надо было перенаправить. По результатам исследований в трубе специалисты-аэродинамики КАИ установили, что радиус закругления боковой панели (где «лоб» переходит в «бок») должен быть не менее 150 мм.
Ну, должен-то должен. Но производство вовсю работает, машины с конвейера идут. Шоферы грязные, злые, матерятся, а изменения в каркас внести невозможно!
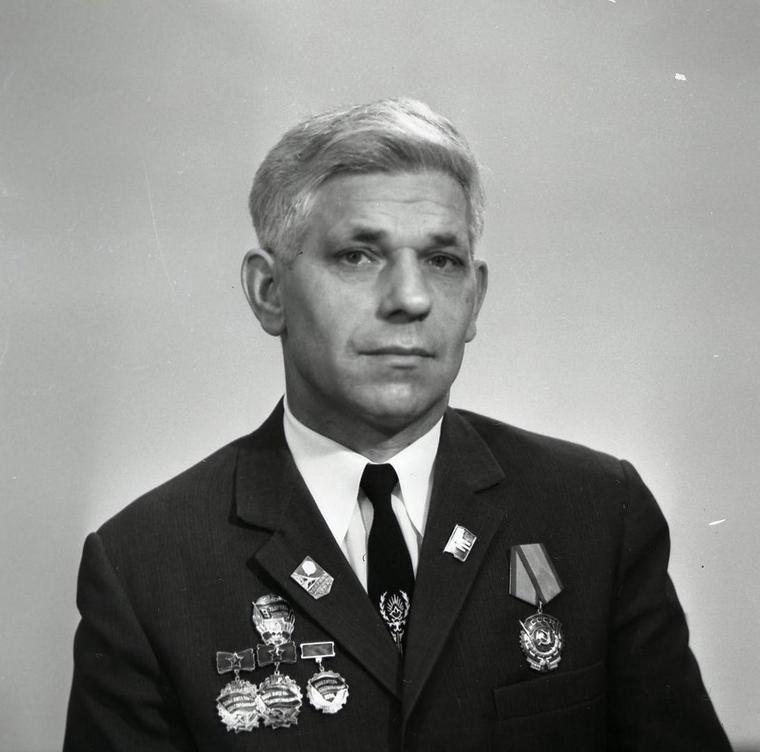
Решение пришло совершенно неожиданно. Жестянщик экспериментального цеха Иван Павлович Соснин буквально «на коленке» выколотил два симметричных дефлектора. Детали сразу установили, выехали на дорогу, в самую грязь. Главный конструктор Барун все проверял сам. Эффект оказался ошеломительным! За счет того, что входное отверстие было побольше, а выходное – поменьше, создавалась струя, которая как раз и отсекала грязь на нужном уровне.
Эти дефлекторы стали первыми изменениями, внесенными в конструкцию уже выпускавшегося автомобиля. Панельки, «сляпанные» на самом простом штампе, спасли огромную технологическую линию.
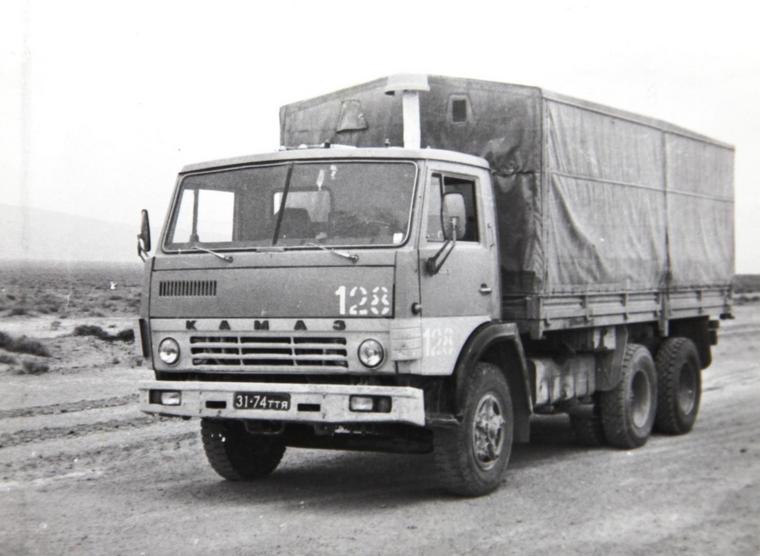
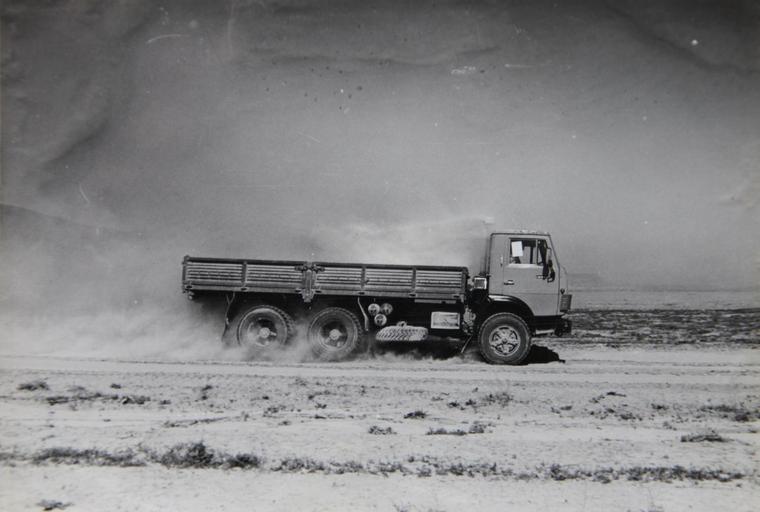
Позже их облагородили, сделали вполне эстетичную деталь по всей длине стыка фронтальной и боковой панелей – но идея осталась. А в целом уникальную по технологичности кабину в целом никто менять не собирался.
Была такая история. Стекла готовых кабин стали часто трескаться. Сначала думали, что при погрузке-разгрузке сами стекла бросят, как попало или стукнут, получается незаметный скол.
Обеспечили амортизацию – брака поменьше, но все равно трескаются. Возвраты, ремонт, жалобы со всех сторон. Шум поднялся такой, что коллегию министерства специально собирали, камазовских конструкторов обвинили в том, что кабина вся «дышит»: «Немедленно сделать расчет жесткости заново! Повысить жесткость!».
Расчеты десять раз перепроверили – жесткость в порядке, а трещины идут.
Помог выяснить причину ККК. Поставили специально конструктора, решили так: двое суток пусть стоит и смотрит, лично стекла отбраковывает. Потом проверим – появятся на «отборных» машинах трещины или нет. И после всех проверок приходит только что собранная машина- с трещиной стекло.
Стали его менять – тоже под присмотром, тут-то все выяснилось.
Оказалось, рабочий заправляет стекло в резину … стальной отверткой – раз-раз, и готово.
Отогнули резинку, а там уже скол. Просто никто раньше внимания на это не обращал. Ввели в технологию эбонитовую отвертку, и кошмар закончился. Трещины исчезли, как будто их и не было никогда.
Азаматов Рамиль Абдреевич.
При подготовке этой книги не удалось найти ни одного упоминания о планировавшейся продолжительности жизни автомобилей на конвейере. Получается, кабина должна была оставаться незыблемой константой, «фирменным знаком» КАМАЗа до тех пор, пока не придет в полную негодность оборудование, на котором она производится. С очень приличными шансами попасть когда-нибудь в «Книгу рекордов Гиннеса»…
В записных книжках Ильи Ильфа, одного из создателей Остапа Бендера, есть отклик на рекламу 20-х годов прошлого века: «Мне не нужна «вечная» игла для примуса – я не собираюсь жить вечно!».
Мнением литераторов Минавтопром, разумеется, не интересовался. Но время шло, страна удивительно быстро и бурно менялась. С одной стороны, экономические трудности российского и заводского масштаба объективно отодвигали возможность решения таких инженерных задач. А пожар на заводе двигателей КАМАЗа мог бы вообще поставить крест на каких-либо улучшениях.
С другой стороны, становилось ясно – рынок пришел всерьез и надолго. Слишком аскетичные решения рано или поздно не позволят заводу успешно конкурировать с другими производителями. Главный конструктор понимал - необходимо, как минимум, обновить кабину, изменить ее облик, не меняя каркас.
Современные пластики могут существенно облагородить интерьер и экстерьер машины, а получить облицовочные панели можно с использованием недорогой оснастки.
Заказ на модернизацию – фейслифтинг - кабины КАМАЗа получили в начале 90-х дизайнеры голландского концерна DAF.
Принципиальным было сохранение оснастки, установленной на прессово-рамном заводе – а значит, конструкции каркаса. Некоторыми штампами можно было пожертвовать, но узлы сварки оставались неприкосновенными.
В самом конце 1993-го года двух молодых специалистов и начальника отдела компоновок отправили на шесть месяцев в Голландию, для участия в разработке. Голландцы создали математическую модель, изготовили макеты интерьера и экстерьера в натуральную величину, выполнили рабочие чертежи.
Пластилиновый макет голландского фейслифта до сих пор стоит в НТЦ - его автор Бертран Янссон лично приезжал в Набережные Челны сдавать проект.
В итоге за очень скромные деньги удалось получить обновленное «лицо» КАМАЗа (кстати, тогда же появилась и новая треугольная эмблема).
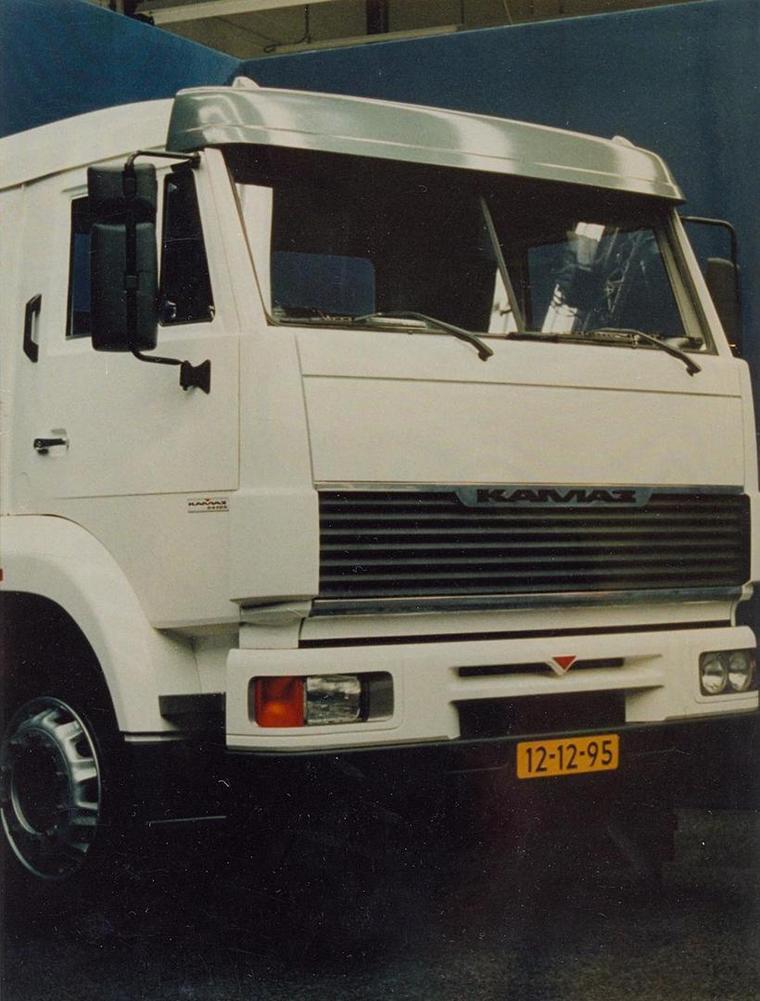
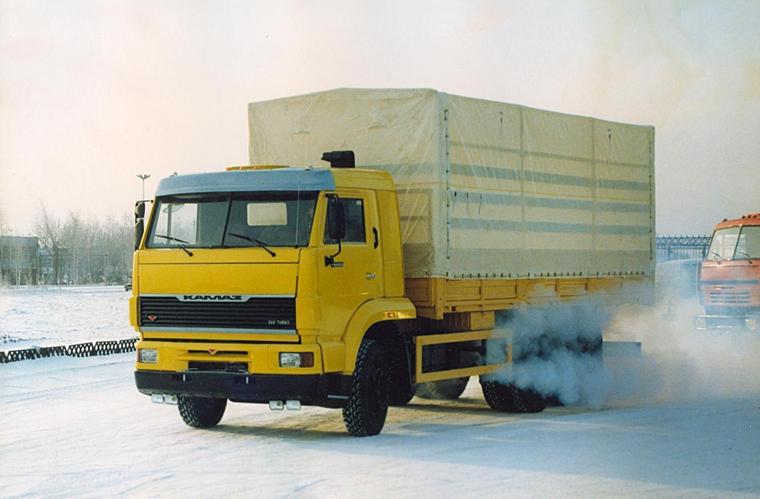
В мае 95 года проект приняли, сегодняшний облик камазовской кабины – продолжение того фейслифта.
Часть проблем удалось решить минимальными усилиями. Или, по крайней мере, отложить до лучших времен – когда завод выйдет из тяжелого кризиса, наберет достаточно сил для серьезных изменений. А проблем, конечно, хватает.
Прежде всего, надо увеличивать размеры кабины – это, по общему мнению, основная слабость конструкции КАМАЗа. Иначе невозможно сделать в ней хороший тоннель, чтобы, к примеру, сдвинуть вперед двигатель. Это сократило бы общую длину автомобиля, дало ряд других преимуществ - например, в системе охлаждения можно было бы поставить большие радиаторы.
Конструкторы НТЦ, естественно, пробовали делать тоннельную кабину из серийной – и сделали, ухитрились даже уложиться в требования ГОСТа. Но тогда внутри стало еще теснее. А это неприемлемо – и так недостаток комфорта не позволяет отнести камские тяжеловозы к магистральным тягачам в полном смысле слова.
Магистральник отличается, в первую очередь, тем, что человек там живет неделями, и для этого нужны нормальные условия. Два спальных места, высокая крыша – для магистральников уже давно не роскошь, это «минимум миниморум».
Решать эти задачи придется в любом случае, отсутствие новой кабины тормозит развитие автогиганта. Какими способами – вопрос отдельный: в комплекс не заложена возможность внесения каких-либо изменений. Например, существует такое «временное решение» - ничего не разрабатывать, сдаться и подстраивать свое шасси к готовым кабинам других производителей.
В НТЦ сегодня можно увидеть самые экзотические варианты КАМАЗов с чужими кабинами.
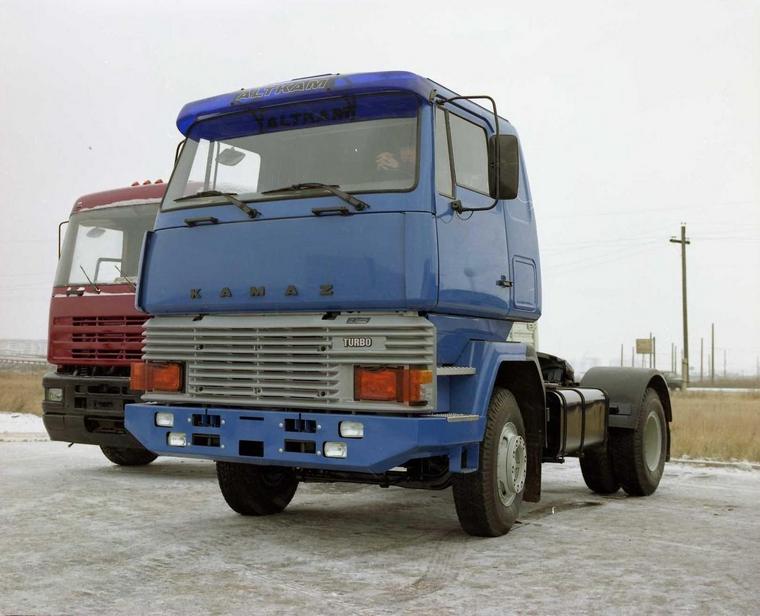

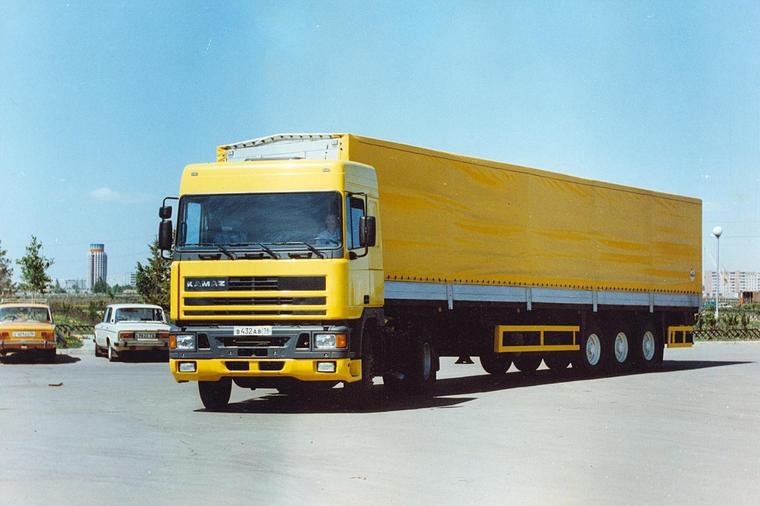
А можно разрабатывать собственную кабину и постепенно менять оборудование, переходя на современные гибкие технологии.
На самом деле, такое решение можно было принять и реализовать раньше. Просто нужна была непреклонная воля, готовность идти до конца и отвечать за свои действия. И обоснованная уверенность в том, что действия эти верны.
Если бы на КАМАЗе в доперестроечное время сложилась на достаточно долгий срок примерно такая тройка – сильный и грамотный директор, сильный и творческий главный конструктор, авторитетный главный дизайнер – пожалуй, удалось бы переломить ситуацию. Находило же Советское государство средства и побольше тех миллиардов, которые нужны были КАМАЗу. Потом бы на экспорте все вернули с лихвой.
Но, допустим, решили свою кабину все-таки делать. Дальше тоже развилка - надо выбирать, кто будет разработчиком. Основных путей три – сделать самим, купить готовую или заказать разработку. Смогут ли прямо сейчас в НТЦ еще раз самостоятельно спроектировать кабину?
Существует фиксированный набор требований по эргономике, безопасности. Уложиться в него формально не так уж сложно, так что смогут, конечно – на определенном уровне.
Но, играя по мировым правилам, КАМАЗ не может себе позволить «определенного» уровня – ему необходим, как минимум, высокий. А для этого требуется потратить весьма немалые деньги – и главное, время - на взращивание собственной серьезной школы дизайна, которая до настоящего времени была невостребованной. Потому что с дизайна и общего облика должна начинаться разработка автомобиля – по крайней мере, тех его частей, которые открыты для всеобщего обозрения, кабины в первую очередь.
Так что, вероятно, выбор надо делать между двумя оставшимися вариантами – рассматривая покупку готовой кабины в любом случае как временное, промежуточное решение. И главное - политическая воля - имеется, Генеральный директор Сергей Анатольевич Когогин решение принял. КАМАЗ рассматривает предложения от ведущих зарубежных дизайн-ателье по разработке новых кабин для всего модельного ряда.
При этом фирма-разработчик должна выдать в качестве результата не только документацию на само изделие, но и документацию на соответствующую оснастку. С указанием конкретного производителя каждого вида оборудования, которое потребуется для запуска новой кабины в производство. Начать их производство планируют через четыре года.
В соответствии с действующей концепцией развития, КАМАЗ намерен к 2012 году выйти на уровень выпуска 100 тысяч автомобилей, и они просто обязаны иметь новое лицо. И это только начало пути. Поскольку в современных-то условиях обходиться одной-двумя моделями по тридцать лет уже не выйдет, разрабатывать новые кабины придется достаточно часто.
Так что восстанавливать и развивать свою дизайнерскую службу все равно, наверное, целесообразно. Однако службу современного типа.
В компании DAF, например, принято для каждой разработки собирать временную команду - из Англии, Америки, Италии приезжают специалисты на год-два.
Принцип аутсорсинга – набор временных исполнителей под задачу, «сделали и разбежались». Значит, незачем держать своих специалистов? Ответ неправильный. Свой штат у них, разумеется, есть, хотя и недостаточный для всесторонней законченной разработки. Но в этот штат входят только профессионалы мирового уровня, потому что они должны сделать главное.
Во-первых, создать саму концепцию новой машины, ее стиль и образ, учитывая и традиции фирмы, и новые мировые тенденции, и все остальное, что должен знать и чувствовать нутром настоящий дизайнер.
Во-вторых, квалифицированно и четко сформулировать техническое задание для команды проектировщиков, «перевести» свою концепцию на более приземленный язык требований и граничных условий.
В-третьих, принять (или не принять…) выполненную работу. Это оптимальный путь, по которому идут сегодня все крупнейшие автомобилестроители. Стратегические вопросы дизайна и проектирования решать своими силами, а в аутсорсинг (сторонним фирмам-исполнителям) отдавать все, что требует больших затрат менее творческого труда.
Может быть, заказ на стороне будет несколько дороже, чем разработка своими силами. Однако по суммарным затратам разница, на самом деле, небольшая – потому что главные расходы связаны не с самой разработкой, а с постановкой на производство. Один крупный штамп может стоить сотни миллионов, а их надо, скажем так, совсем не один.
По отношению к этим гигантским расходам разработка будет стоить, наверное, проценты, а то и доли процента. Но такой путь значительно быстрее по срокам, а значит, и экономически более оправдан, в большей мере соответствует стратегии развития автогиганта.
Ну, а воплотится ли в металле что-то из красивых конструкторских концепций и решений прошлых лет - время покажет.
Информация в этой статье относится к 2008 году, в настоящее время уже построен завод каркасов кабин для поколения К5,
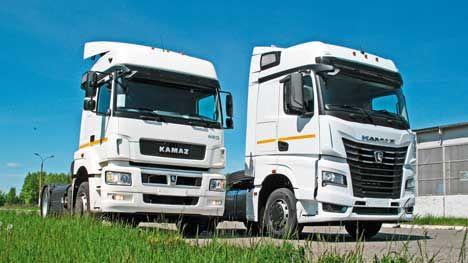
на пресово-рамном заводе имеется производство кабин К4.
Каркасы кабины К5 будут использоваться в сборочном производстве как КАМАЗа, так и Мерседеса.
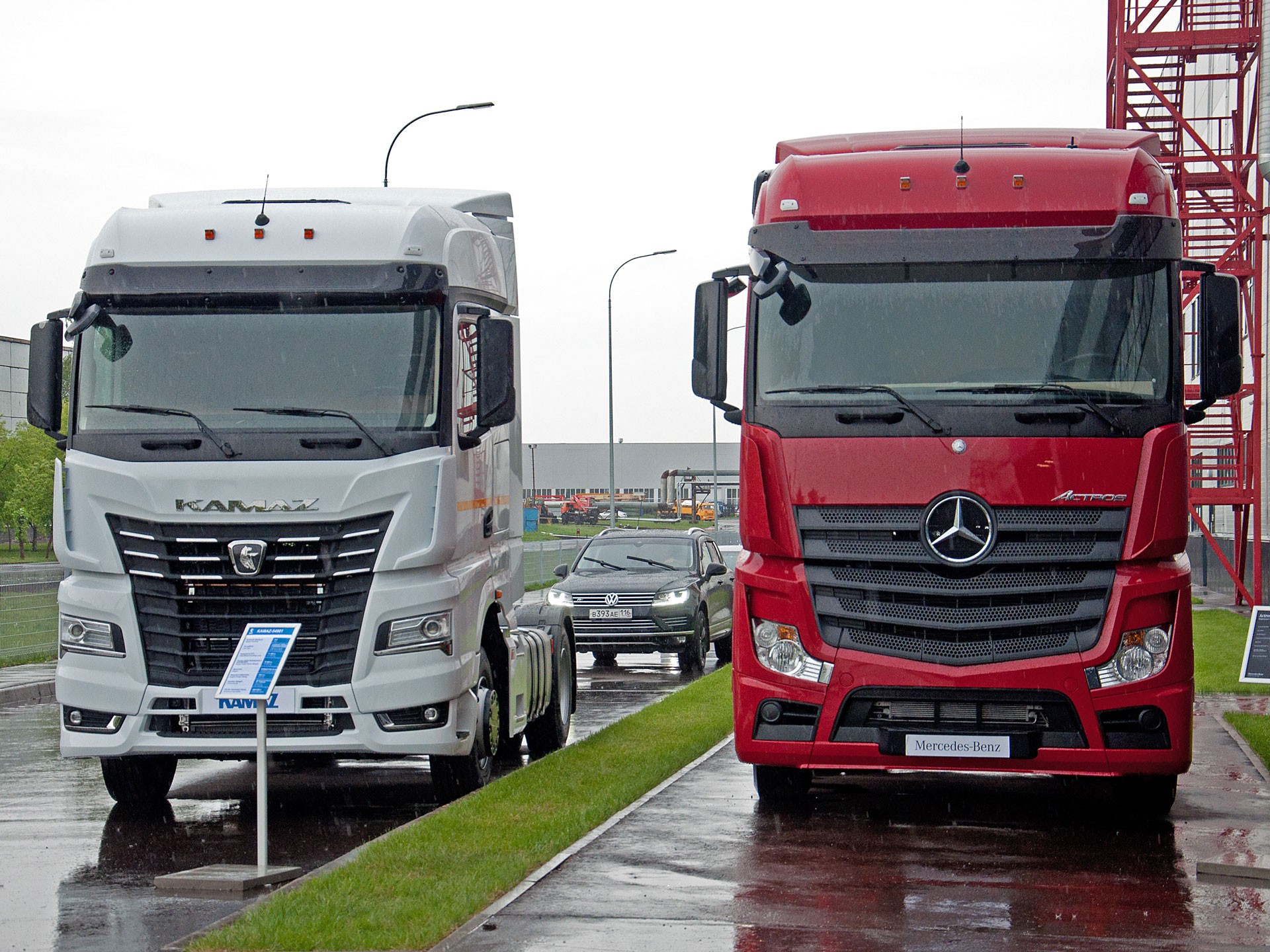
Так-же хочется упомянуть и о попытке разработать собственную кабину для КАМАЗа в 1988 году, об этом в статье "Проект-88"
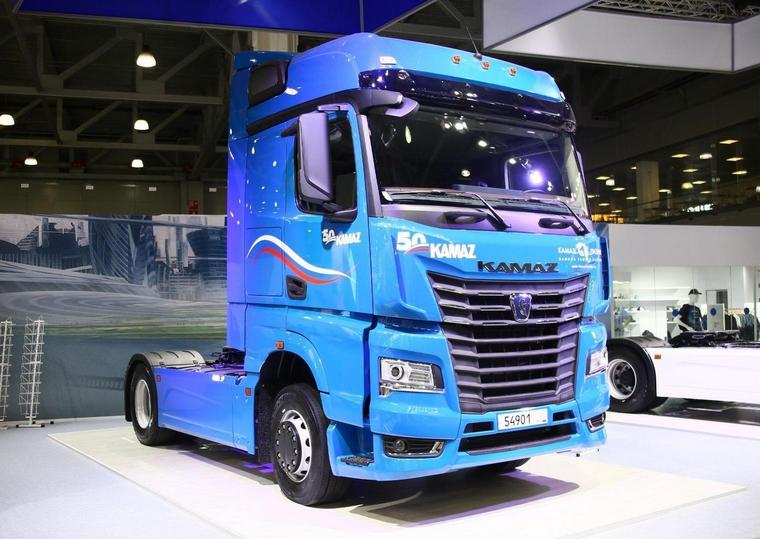
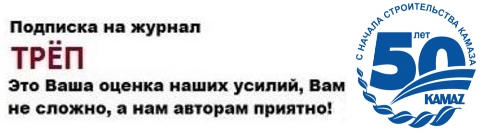
Оценили 29 человек
54 кармы