Добрый день, КОНТ! Предлагаю очередную подборку из накопившихся новостей автогиганта.
Автопарк МЧС в Биробиджане пополнился новой спецтехникой. Об этом сообщает пресс-служба ГУ МЧС по Еврейской автономной области.
Так, на службу к спасателям поступила пожарно-насосная станция на базе КАМАЗа. Грузовик пришел на замену автомобилю, прослужившему 33 года. Отмечается, что техника будет использоваться при наводнении для откачки воды с территорий населенных пунктов. А также с помощью нее будет производится тушение крупных пожаров: оборудование позволяет установить насосную станцию на открытый водоисточник и, запитывая по рукавным линиям автоцистерны, в кратчайшие сроки ликвидировать возгорание.
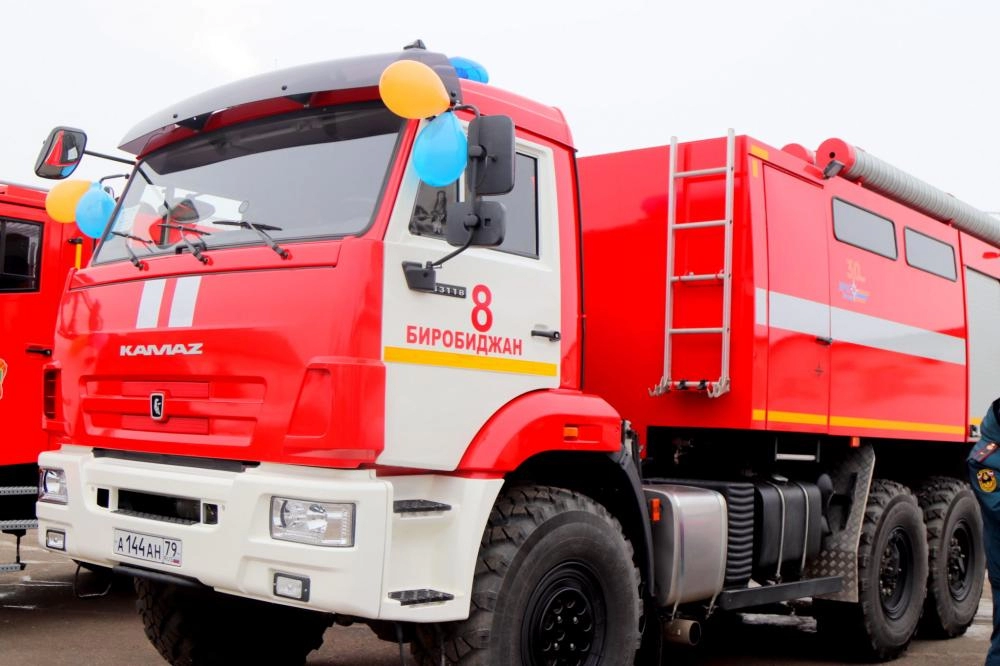

«Такой техники в распоряжении подразделений Главного управления еще не было. Спецтранспорт оснащен всем необходимым оборудованием для ликвидации возгораний, а также оказания помощи пострадавшим во время чрезвычайных происшествий. Оборудован автомобиль и спецприборами - индивидуальными маячками, с помощью которых можно узнать, что происходит с сотрудниками, находящимися в эпицентре пожара. В случае если в непригодной для дыхания среде что-то произошло с газодымозащитником, он находится в неподвижном состоянии, в автомобиле срабатывает сигнал и немедленно отправляется дополнительное звено на помощь и спасение», - заявил начальник Главного управления МЧС России по Еврейской автономной области Роман Бойко.
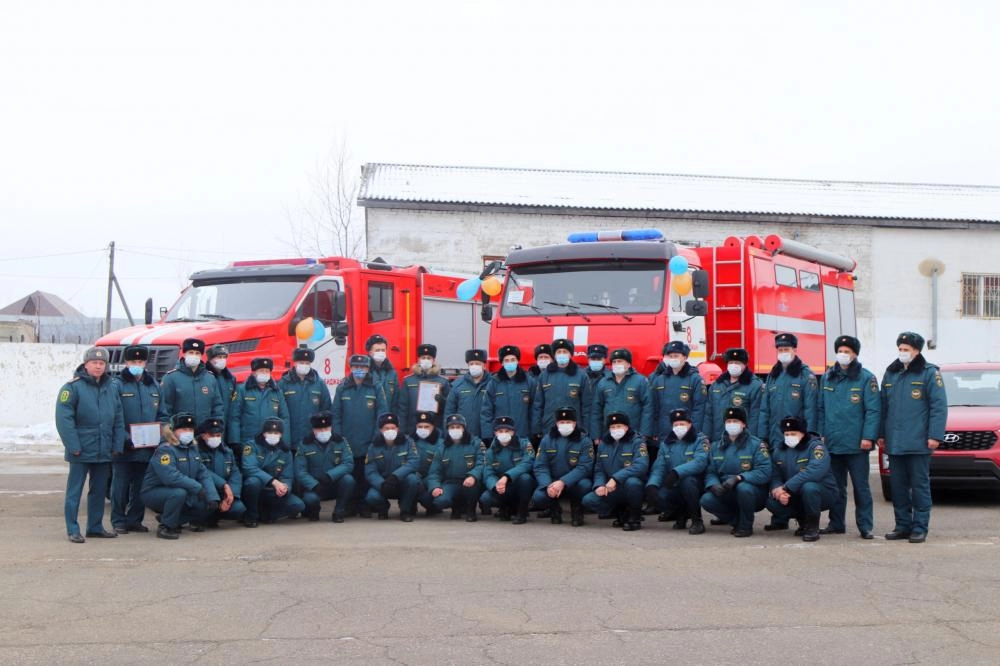
Фото: пресс-служба ГУ МЧС по Еврейской автономной области.
В 2021 году универсальная линия на базе горячештамповочного пресса LZK-4000 № 3, расположенная в КПК-1 кузнечного завода, отметит 45-летие. Свой юбилей оборудование встретит в обновлённой версии. Над его преображением сейчас работают многочисленные специалисты кузнечного завода и подрядных организаций.
Во второй половине 70-х годов кузнечный завод «КАМАЗа» был оснащён 43 универсальными ковочными линиями на базе кривошипных горячештамповочных прессов с разным усилием прессования производства чешской фирмы «Шмерал». Десятилетия оборудование интенсивно эксплуатировалось, выдавая поковки. К январю 2019 года линия LZK-4000 № 3 выработала свой ресурс и была остановлена на капитальный ремонт.– Капитальный ремонт этой линии – процесс чрезвычайно трудоёмкий, он потребовал изготовления и восстановления большого количества крупногабаритных дорогостоящих узлов и запасных частей, – комментирует начальник бюро ОГМ кузнечного завода Тимур Ахметзянов. – Расчётный срок капремонта этой ковочной линии 18 месяцев.
В начале этой ремонтной истории на кузнечном заводе была сформирована межфункциональная команда, в которую вошли специалисты ремонтно-механического цеха (РМЦ), лаборатории промэлектроники (ЛПЭ), цеха ремонта и обслуживания оборудования корпуса № 1 (ЦРиООК-1), отдела главного механика (ОГМ). Перед ними была поставлена задача привести линию в исправное состояние.
Тимур Ахметзянов (справа): «Капремонт универсальной ковочной линии LZK-4000 № 3 позволит привести оборудование к нормам технологической точности, значительно повысить качество поковок, снизить аварийные простои и затраты на закупку запчастей»
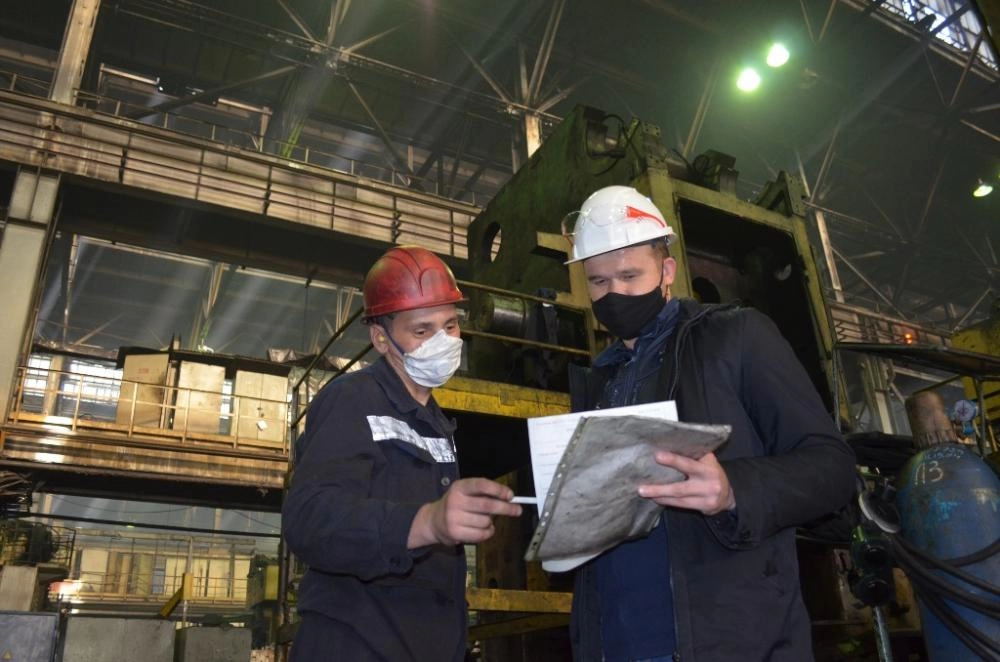
По словам Тимура Ахметзянова, трудности в дело внесли неисправности, с которыми специалистам завода пришлось столкнуться впервые за несколько десятков лет эксплуатации и ремонта оборудования. Например, сложная задача усталостного разрушения шатуна и ползуна пресса. Силами работников РМЦ кузнечного завода изготовили новый шатун, а новый ползун был закуплен.
Кроме того, предстояло решить наисложнейшую задачу, связанную с разрушением фундамента пресса. Силами специалистов сторонних организаций с привлечением спецтехники для восстановления фундамента были выполнены демонтаж и монтаж станины ковочного пресса весом 112 тонн. Удалось улучшить и качество фундамента, в первую очередь за счёт применения в армировании усиленной рамы, что придаст ему долговечность.

Не осталось без внимания и электрооборудование. С учётом, что его многие компоненты уже не выпускаются, специалистам завода предстояло найти для ремонта современные решения: впервые было предложено вести управление релейной системы от микроконтроллера, а значит, получена возможность контролировать защиту всех важных параметров работы пресса. А ещё, главный электродвигатель с фазным ротором заменён на электродвигатель с ротором короткозамкнутым, управлять которым теперь будет частотный преобразователь. По оценке специалистов, такая замена повысит ресурс работы и обеспечит защиту привода по многим электрическим параметрам.
Сегодня в РМЦ завершается сборка механической части пресса, после чего силами специалистов ЦРиООК-1 и ЛПЭ будет завершён монтаж электрооборудования. Впереди пробный пуск и обкатка пресса. До 15 ноября планируется запустить оборудование в эксплуатацию. Тем временем команда специалистов кузнечного завода уже готовится приступить к капитальному ремонту следующего объекта КПК-1 – линии LZK-6300 № 2.

На производстве чугунного литья литейного завода изменили технологию изготовления картера заднего моста для самосвала 6522. Доработка помогла значительно снизить трудоёмкость процесса.
– Ранее при изготовлении отливки внутри стержня применялась стальная труба длиной 1,5 метра. Она придавала прочность конструкции, а её концы служили местами захвата для установки в форму. Песчаный стержень весит порядка 75 кг, его проставляет в форму автоматизированный кондуктор, – пояснил главный специалист технологического отдела ПЧЛ Альберт Габдулхаков.
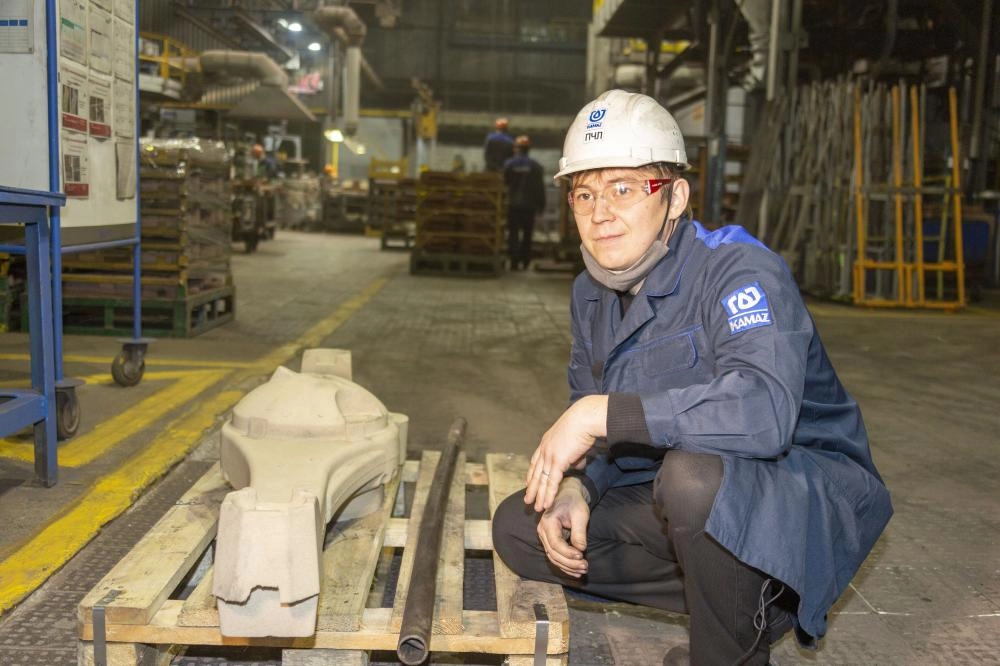
Однако при изготовлении отливки труба проявляла себя не лучшим образом и доставляла большие проблемы обрубщикам, добавил технолог:
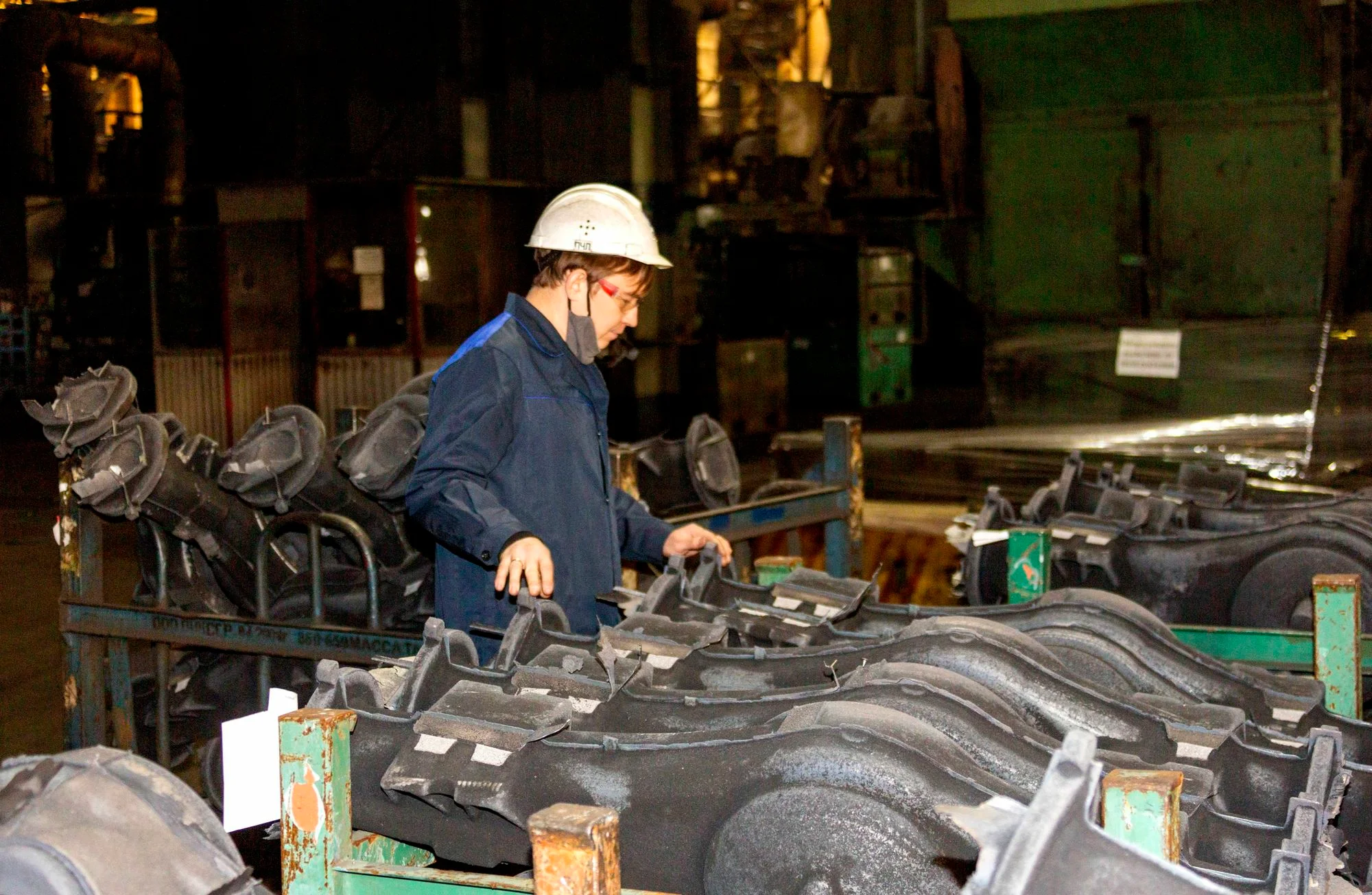
– При заливке формы под воздействием горячего металла происходило коробление трубы. Стержень растрескивался, в трещины проникал металл. На выходе мы получали отливки с большим количеством заливов, которые было очень трудоёмко дорабатывать. Обрубщики подручными средствами доводили отливку до ума: пробивали залитую металлом полость зубилом, пилили, точили… В итоге не успевали делать план. Решением проблемы занялся технологический отдел.

Мы предложили отказаться от использования трубы и доработали конструкцию стержня, чтобы кондуктор мог его захватывать. Изготовили малую партию обновлённых стержней, залили её и получили чистые отливки, не нуждающиеся в доработке. Эксперимент оказался удачным, наш отдел выдал техзадание, в документацию внесли изменения, была доработана модельно-стержневая оснастка. Вот уже третий месяц мы работаем с новыми стержнями и получаем хороший результат.
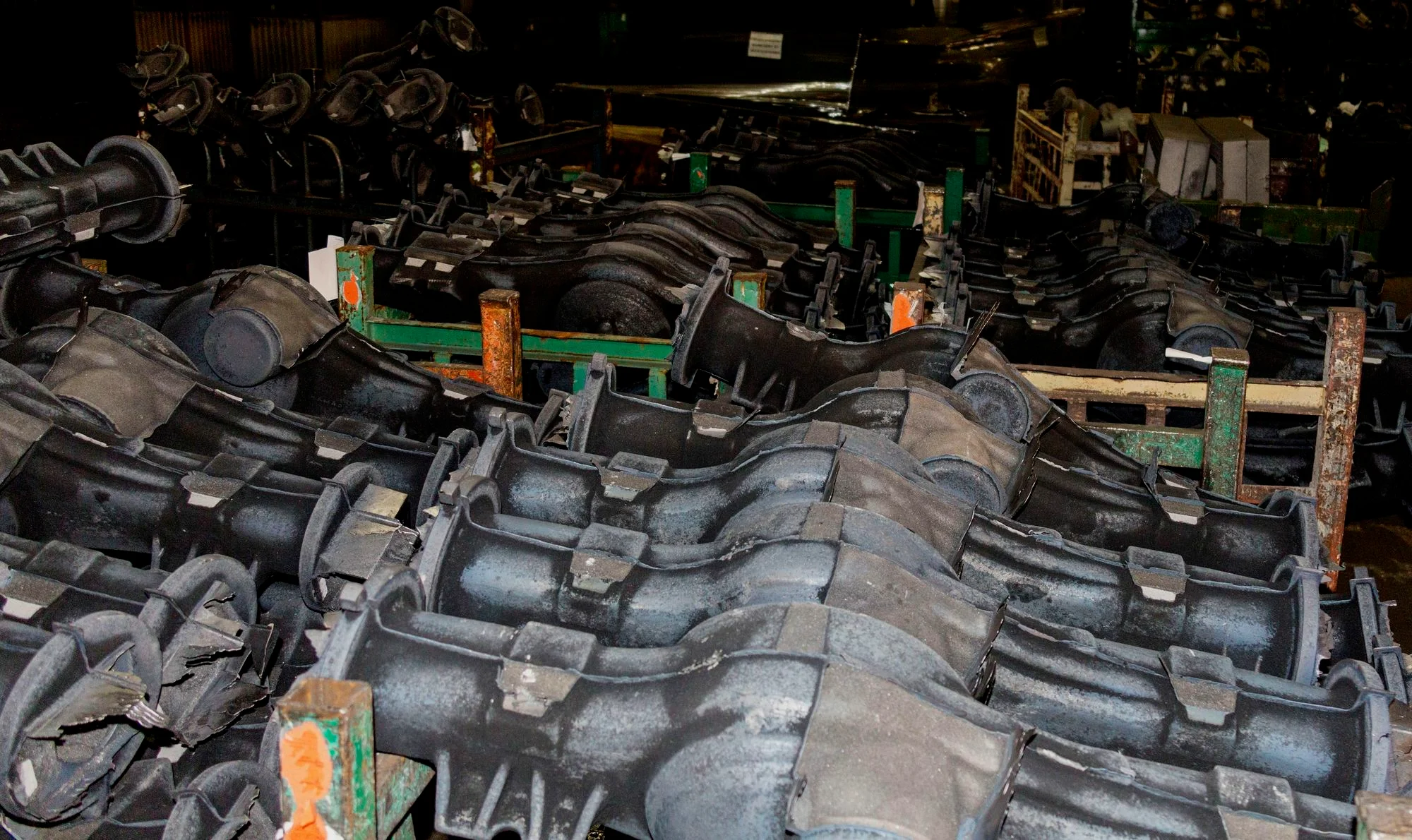
Кроме того, получилось сэкономить: каждая труба стоит порядка 500 рублей, а в месяц по плану выпускается около 100 отливок картера моста. Прогнозируемый экономический эффект – порядка 600 тыс. рублей в год.
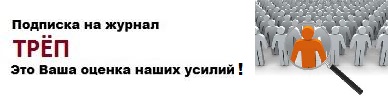
Оценили 20 человек
38 кармы