Добрый день, КОНТ! В своей подборке новостей, я уже неоднократно рассказывал о ходе модернизации производства идущей на ПРЗ (прессово-рамный завод), в настоящий момент все работы выходят на завершающую стадию.
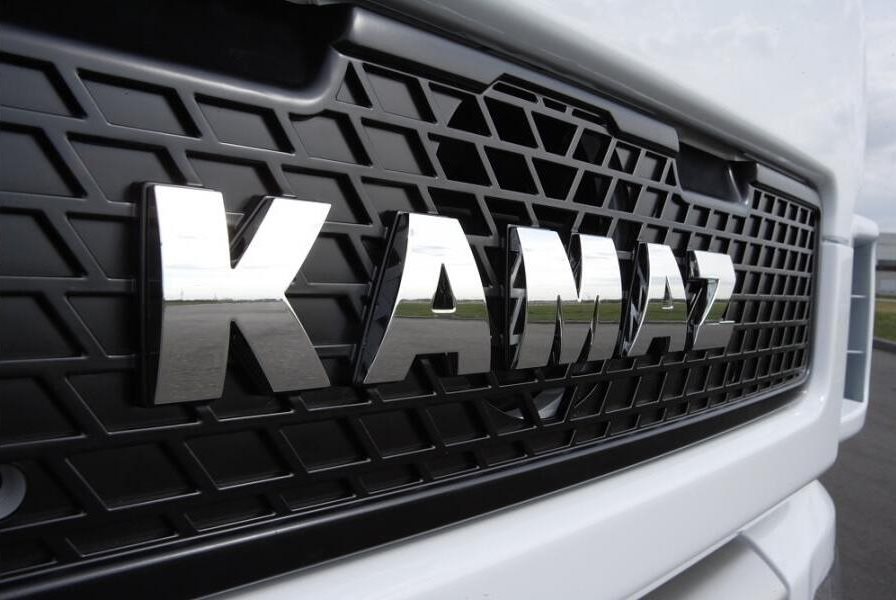
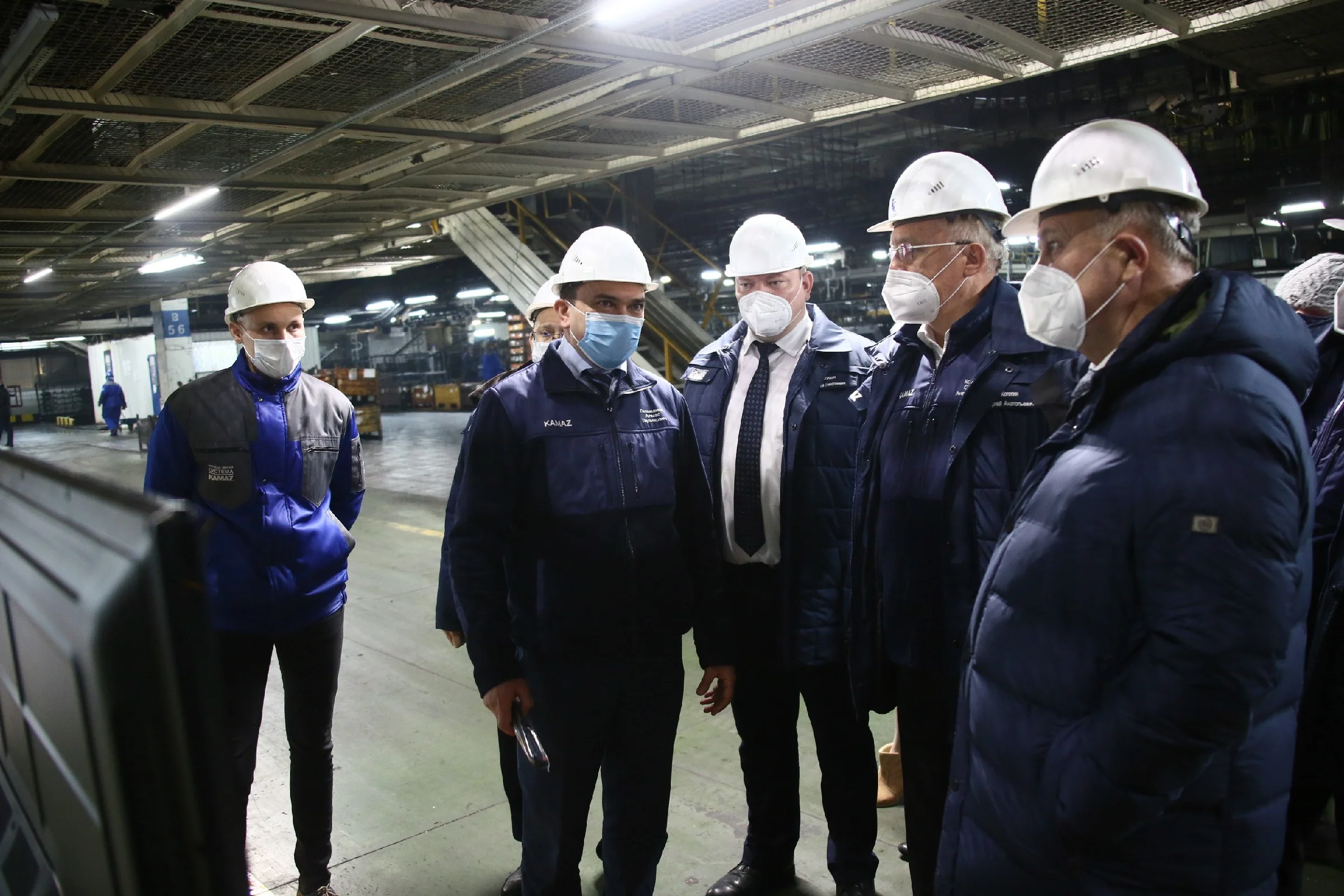
Гендиректор автогиганта Сергей Когогин ознакомился с результатами реализации инвестиционных проектов на прессово-рамном заводе «КАМАЗа». Вместе с ним обошли завод первый заместитель гендиректора Юрий Герасимов, директор ПРЗ Сергей Птичкин и другие топ-менеджеры компании. Начали обход с площадки нового производства рам.
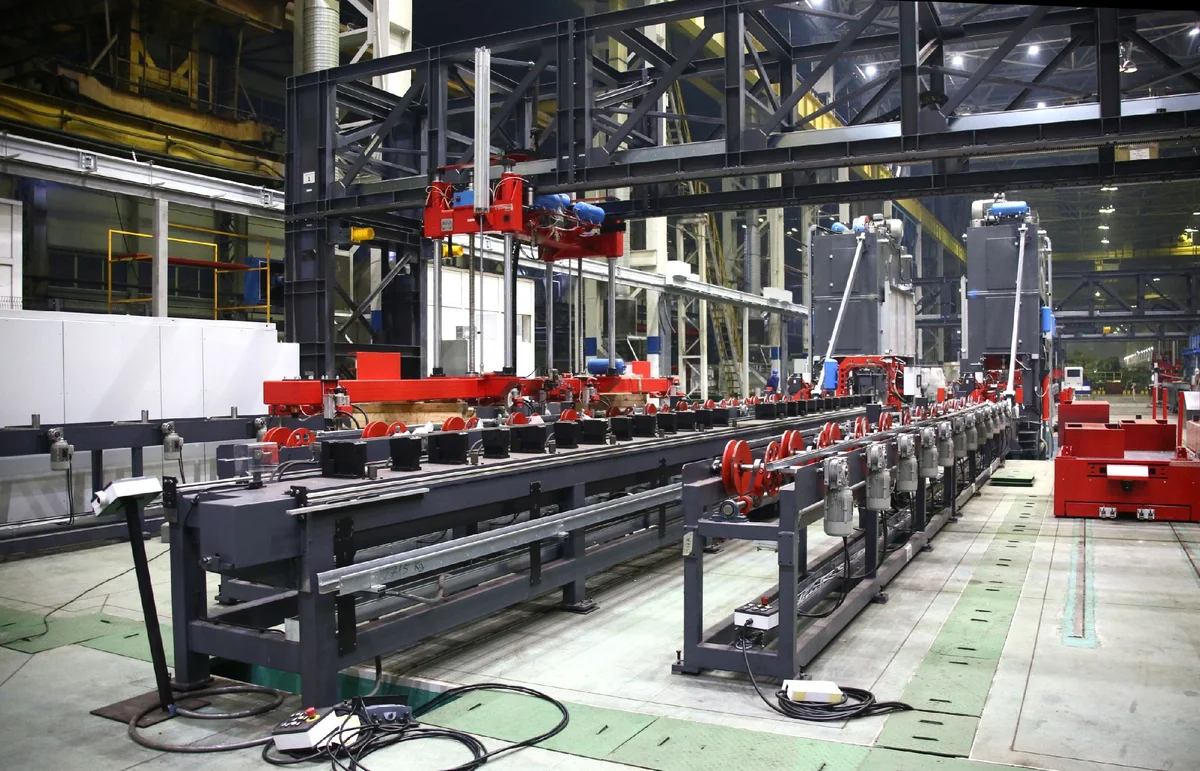
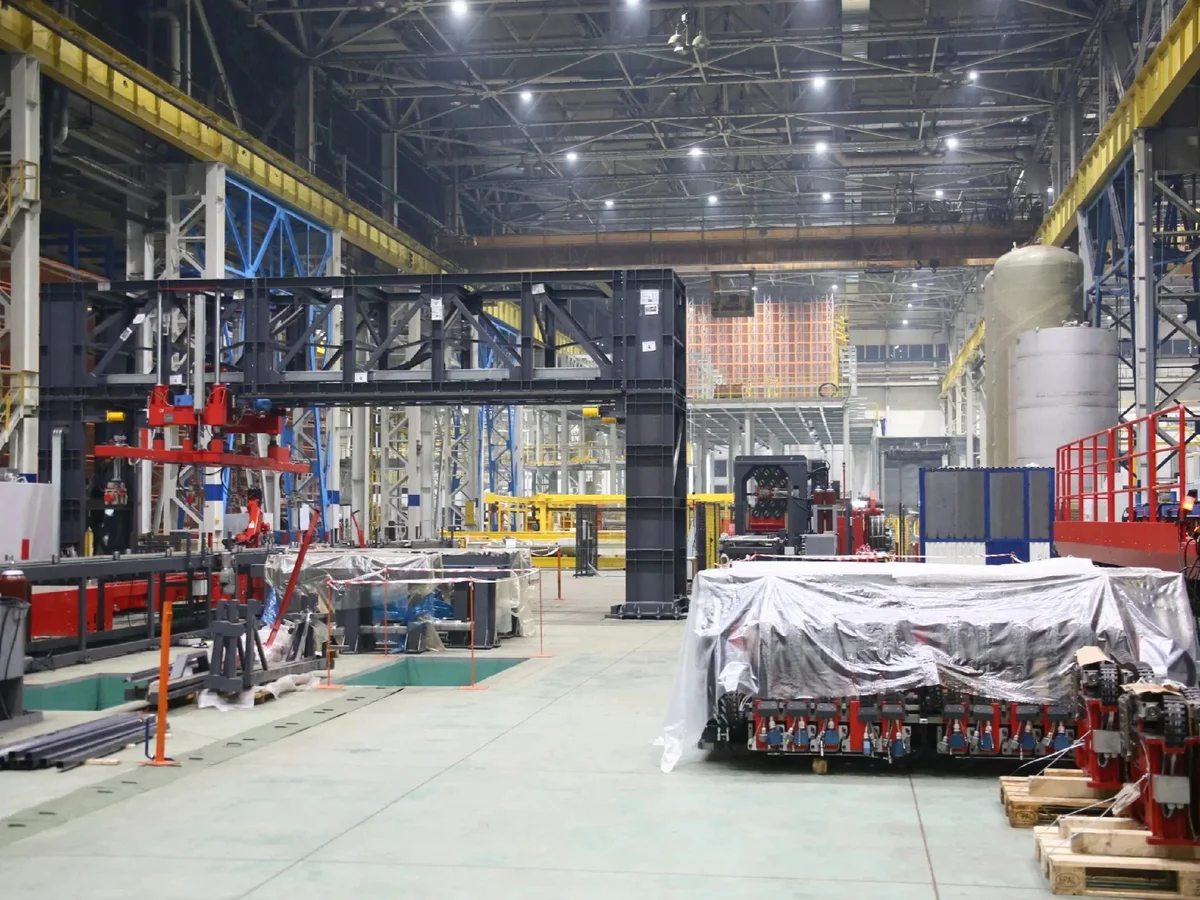
Модернизацию прессово-рамного завода начали в 2017-м году и планируют завершить в 2021-м. Её цель – современное производство рам с повышенной прочностью и антикоррозионными характеристиками. Эти рамы будут устанавливаться на автомобили КАМАЗ нового семейства К5. Три основные линии данного производства — профилирование лонжеронов, окраска рам, сборка рам.
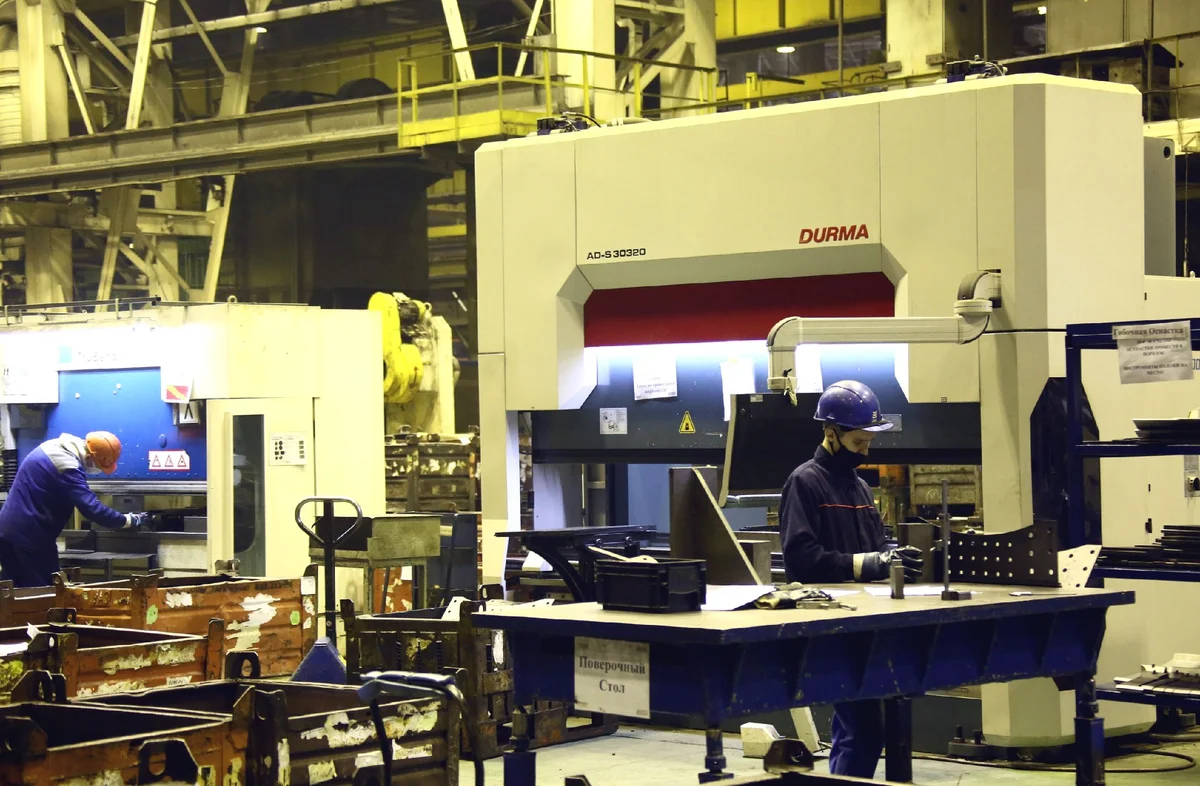

На солидной площади появились очертания конвейеров, работа идёт полным ходом. На линию окраски поставлен весь объём оборудования, смонтировано 43%, срок запуска – второй квартал 2021 года. В декабре необходимо завершить монтаж дробемёта, зоны маскирования, камеры окраски, туннеля для агрегата подготовки поверхности.
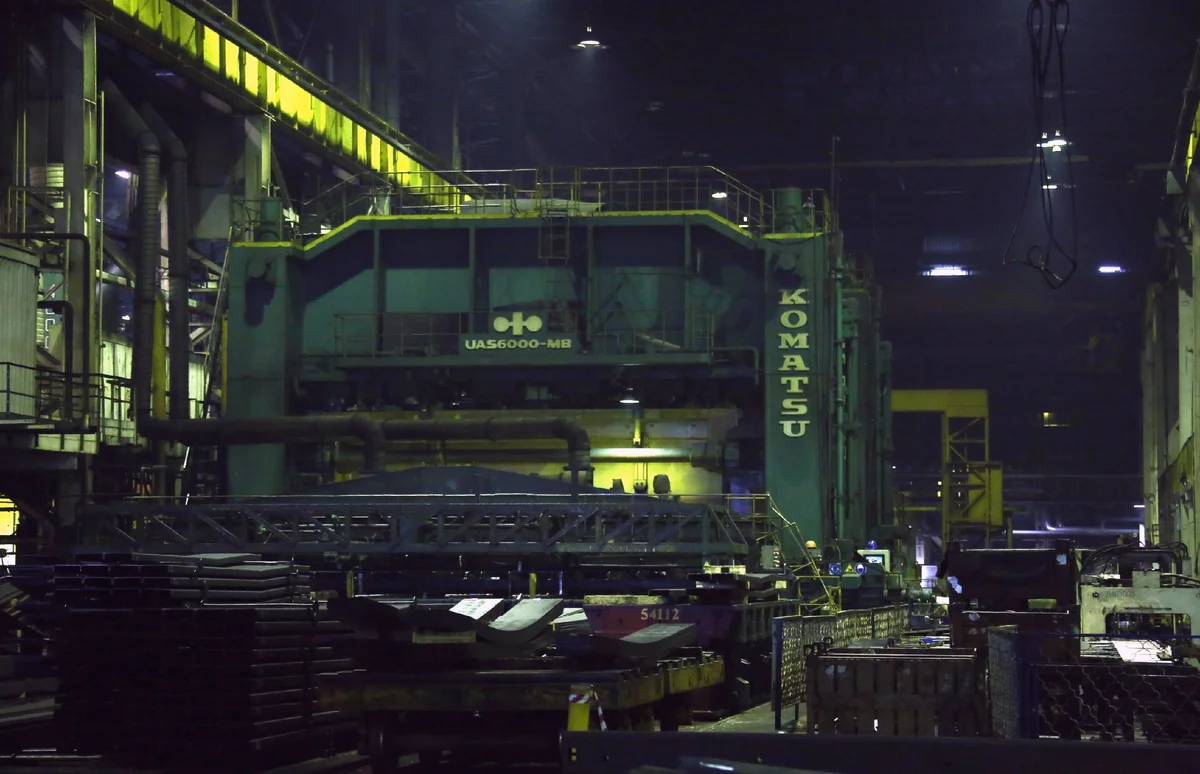
Для конвейера сборки рам изготовлено 95% оборудования, поставлено 70%. В декабре планируется завершить монтаж металлоконструкций, манипуляторов загрузки кассет, электрических сетей. Срок запуска – первый квартал 2021 года. А на линии изготовления лонжеронов уже установлено основное оборудование. В январе начнутся пусконаладочные работы, которые будут вестись параллельно с обучением специалистов.
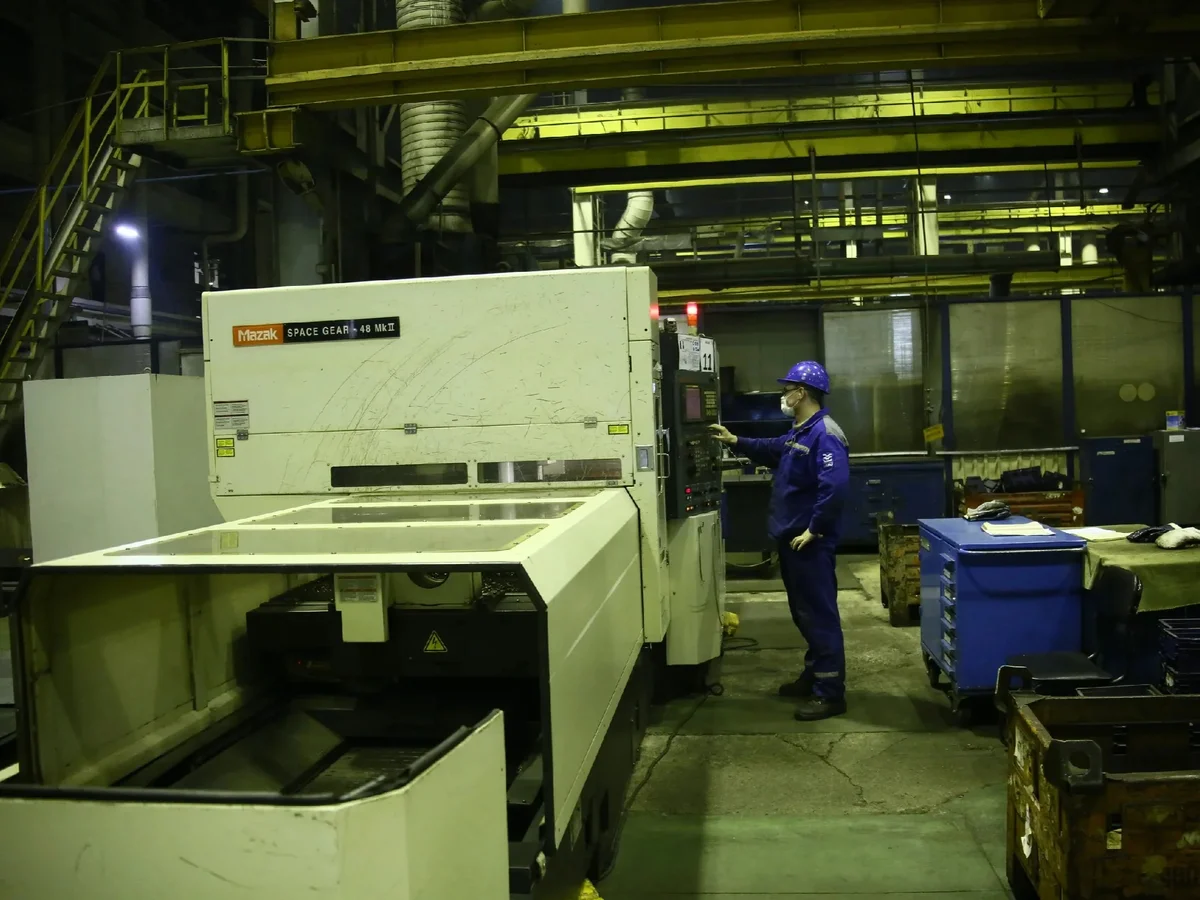
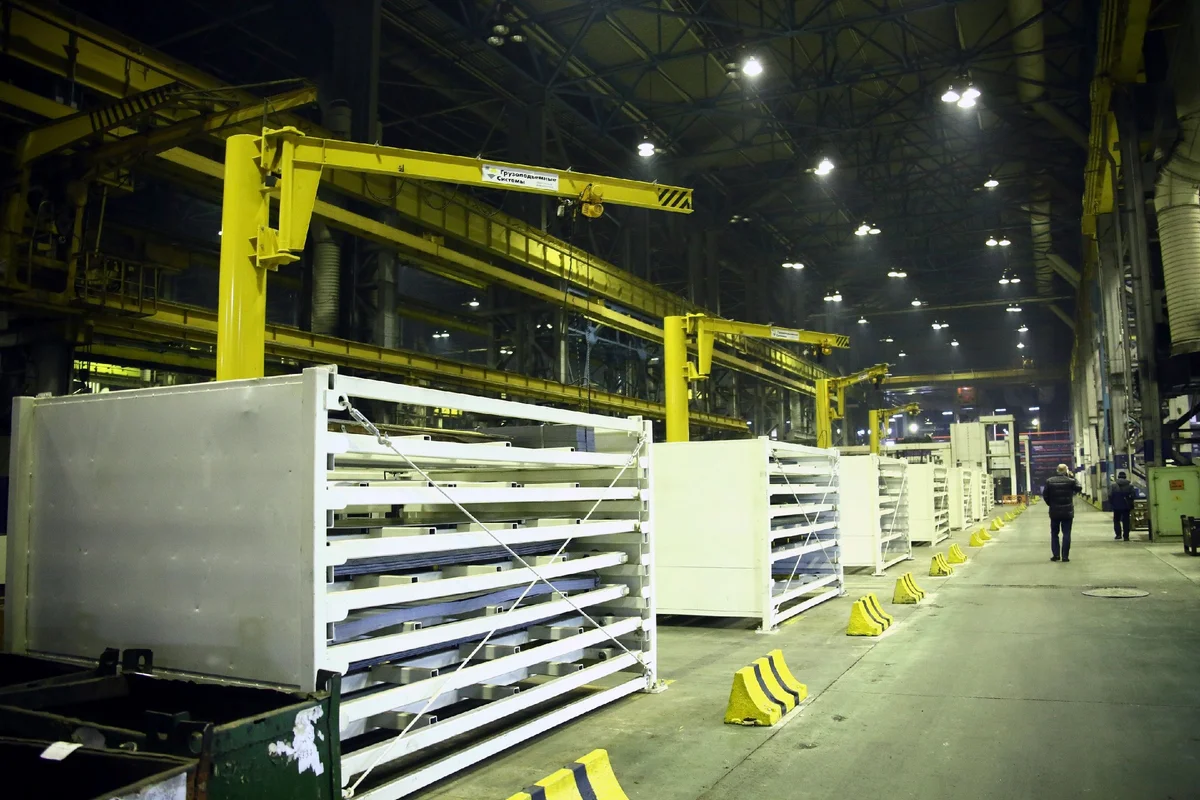
В цехе малых серий руководитель производства Ильдар Асылгараев отчитался о мерах, принятых для повышения ритмичности поставок комплектующих на сборочные конвейеры Автомобильного завода.
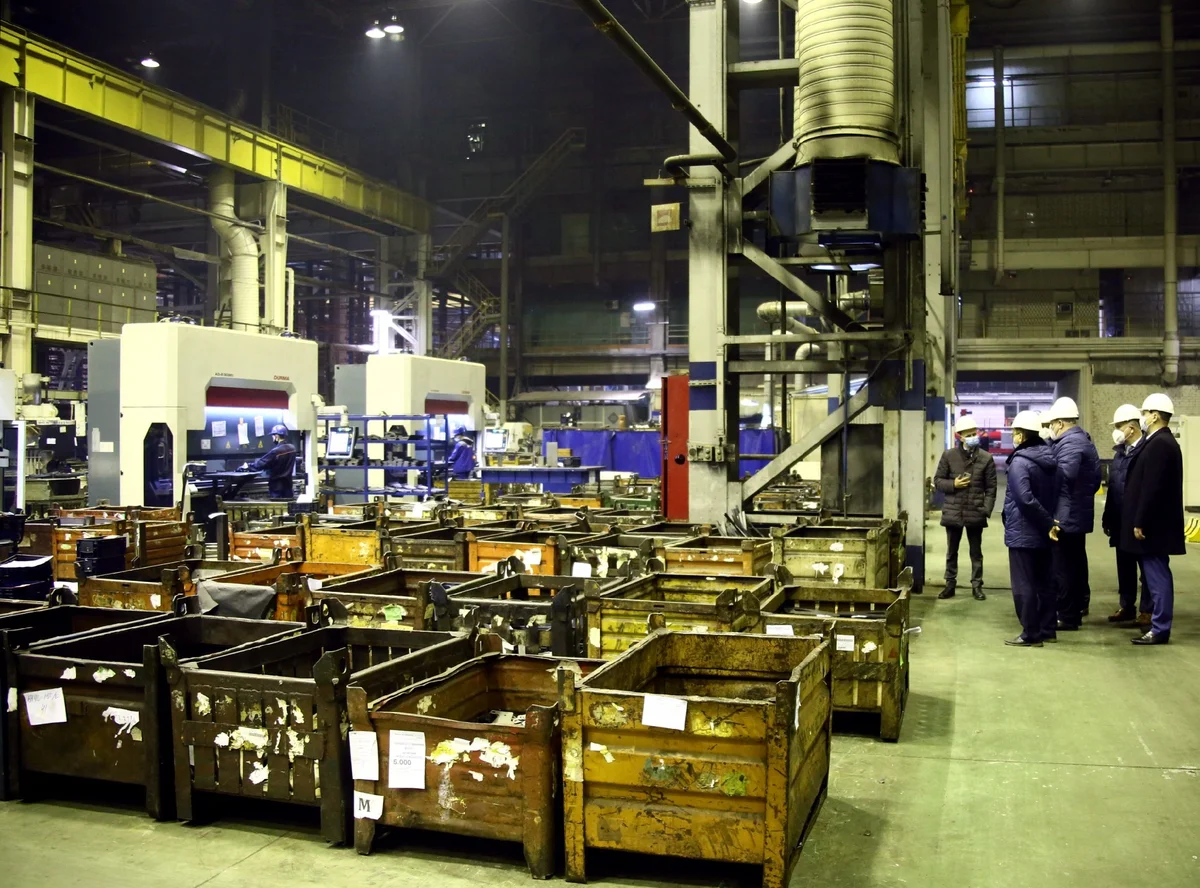
– После проведения картирования, - сказал он, - мы составили тактический план развития из 45 пунктов. Основные направления – снижение потерь при обслуживании установок лазерной резки и гибки металла и изготовление новых штампов. Чтобы уменьшить время загрузки и выгрузки металла, организованы склады рядом со станками. Повысить оперативность настройки оборудования позволит загрузка задания прямо с системы SAP. Программа изготовления штампов выполнена на 83%.

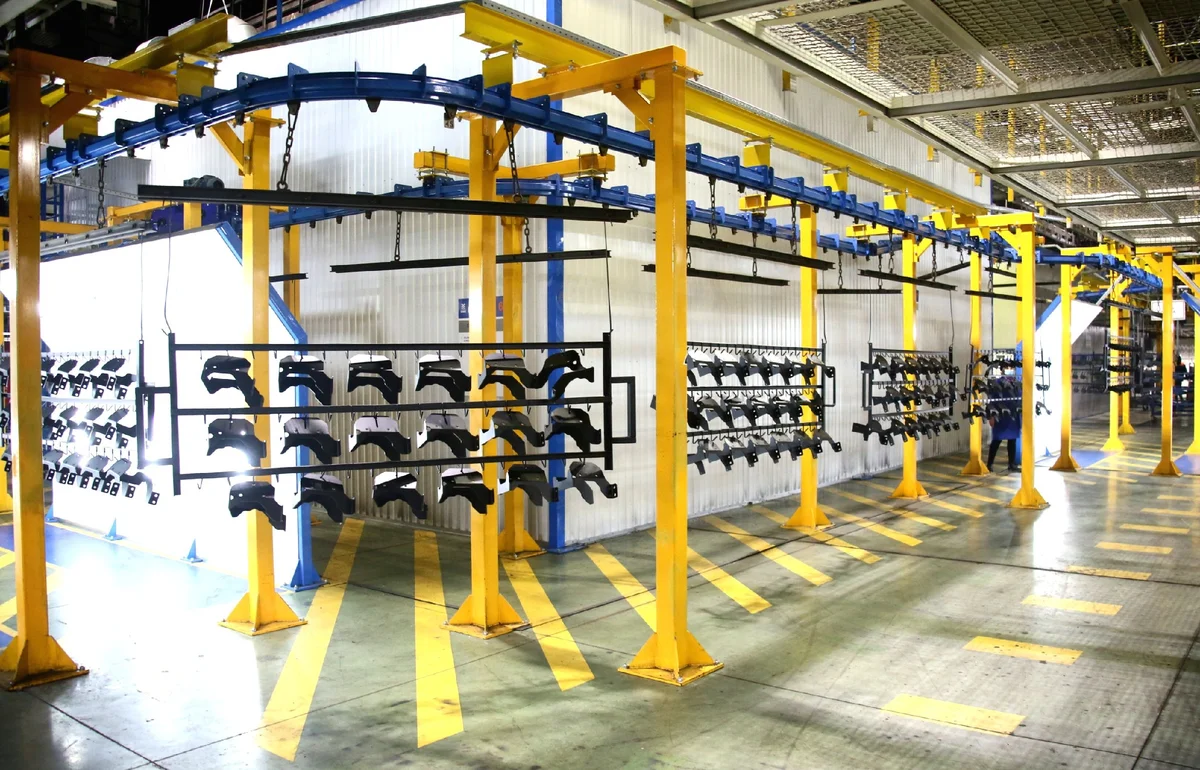
По маршруту обхода гендиректору «КАМАЗа» также продемонстрированы текущие результаты изменения технологии горячей штамповки полубалок картера моста.
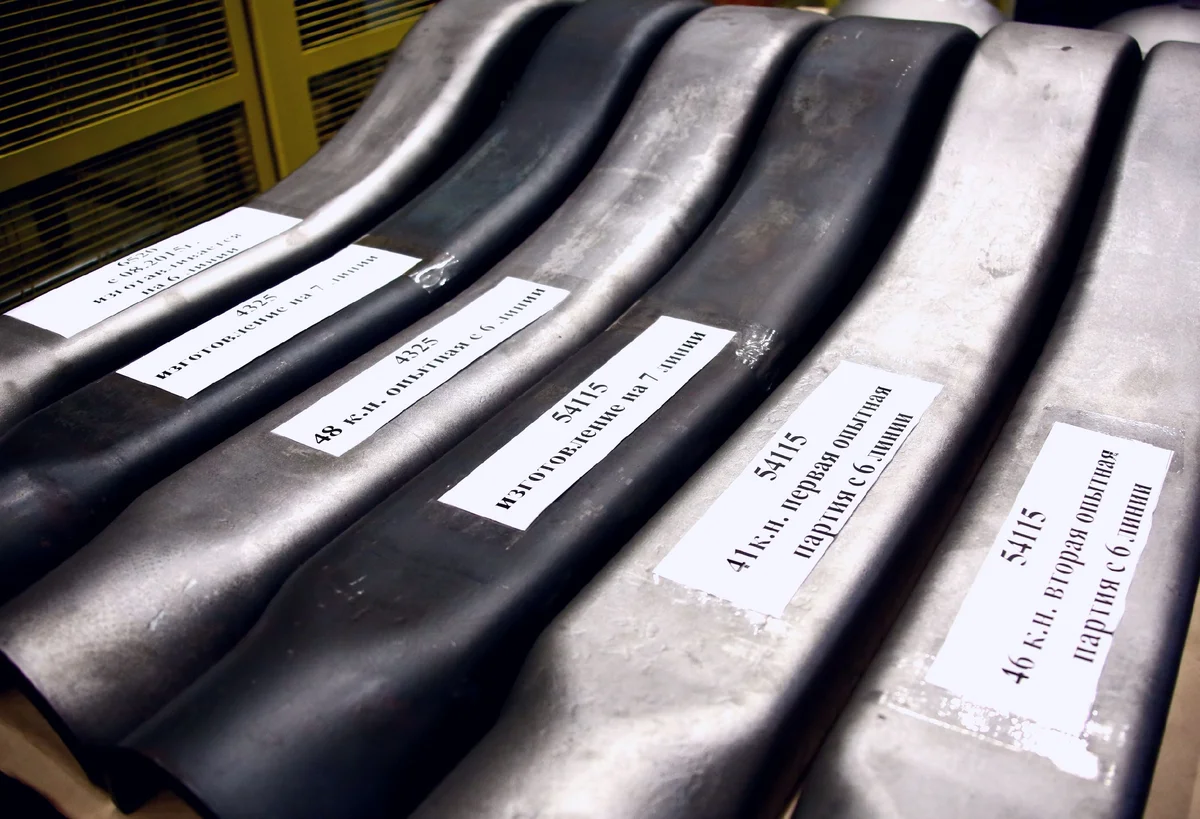
Результаты внедрения на линии 004 порошковой окраски презентовали в цехе окраски № 1. Новая технология позволила в два раза увеличить коррозионную стойкость лакокрасочного покрытия комплектующих изделий для большегрузов.

– Мы эту проблему решаем шаг за шагом, – уверен Сергей Анатольевич. – В следующем году о ней можно будет забыть, потому что качество окраски касается не только автомобилей нового модельного ряда, но и моделей серии К3.
В рамках модернизации производства на прессово-рамном заводе «КАМАЗа» ввели в эксплуатацию новую окрасочно-сушильную камеру проходного типа для окраски каркасов кабин в оригинальные цвета. Новое оборудование позволило повысить производительность, сократить логистические потери и улучшить условия труда.
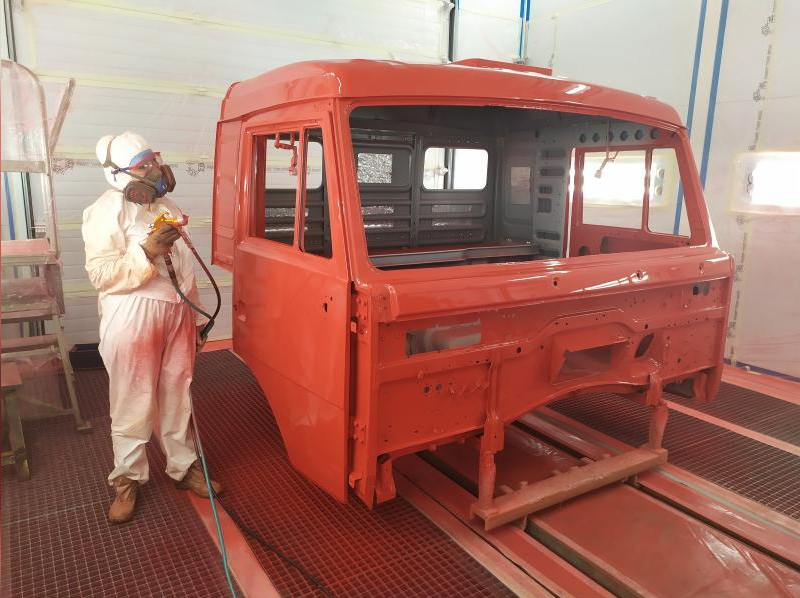
До ввода в эксплуатацию новой окрасочно-сушильной камеры (ОСК), все каркасы кабин окрашивались в оригинальные цвета в окрасочной камере «Гелиос», расположенной на нулевой отметке. После катафорезного грунтования кабины приходилось снимать с напольного конвейера и спускать вниз. Это приводило к значительным временным и логистическим потерям. Кроме того, производительность «Гелиоса» составляла всего 10,5 каркасов в сутки, что влияло на объёмы выпускаемой продукции.
Новая ОСК, встроенная в линию окраски, стала продолжением технологической цепочки окрасочной линии DURR. Она предназначена для окраски поверхности кабины в оригинальные цвета методом пневмораспыления в два слоя с выдержкой между слоями (технология «мокрым по мокрому») с последующей сушкой.
После катафорезного грунтования каркас по имеющемуся напольному конвейеру перемещается в окрасочную камеру. Здесь на первом этапе происходит шлифовка дефектов вторичного грунта, протирка и последующая окраска. Затем каркас проходит сушку при температуре не менее 80°С с последующим охлаждением. Завершается работа контролем лакокрасочного покрытия.
Благодаря вводу новой окрасочной камеры удалось сократить логистические потери, увеличить производительность до 18 кабин в сутки, улучшить качество лакокрасочного покрытия каркасов кабин, а также снизить затраты на техническое обслуживание оборудования. Кроме того, значительно улучшились условия труда работников ОСК. Камера построена по новой технологии, в ней покраска и сушка разделены на отдельные секции, также имеется отдельная зона дефектовки. Улучшены освещённость камеры окраски и кондиционирование. Исключена сорность при окраске, современные фильтры препятствуют попаданию краски в систему.
В лаборатории аналитических исследований материалов ПРЗ осваивают новые приборы для анализа микроструктуры металла. Новое оборудование позволит повысить качество исследований.
Обновление материальной базы ЛАИМ предусмотрено в рамках проектов «Реинжиниринг автопроизводства» и «Модернизация ПРЗ». Улучшилось оснащение лаборатории металлографии, здесь появились станки для автоматической и ручной подготовки проб, автоматический пресс для горячей запрессовки образцов в различные смолы, отрезной станок и анализатор фрагментов микроструктуры твёрдых тел на базе инвертированного микроскопа.
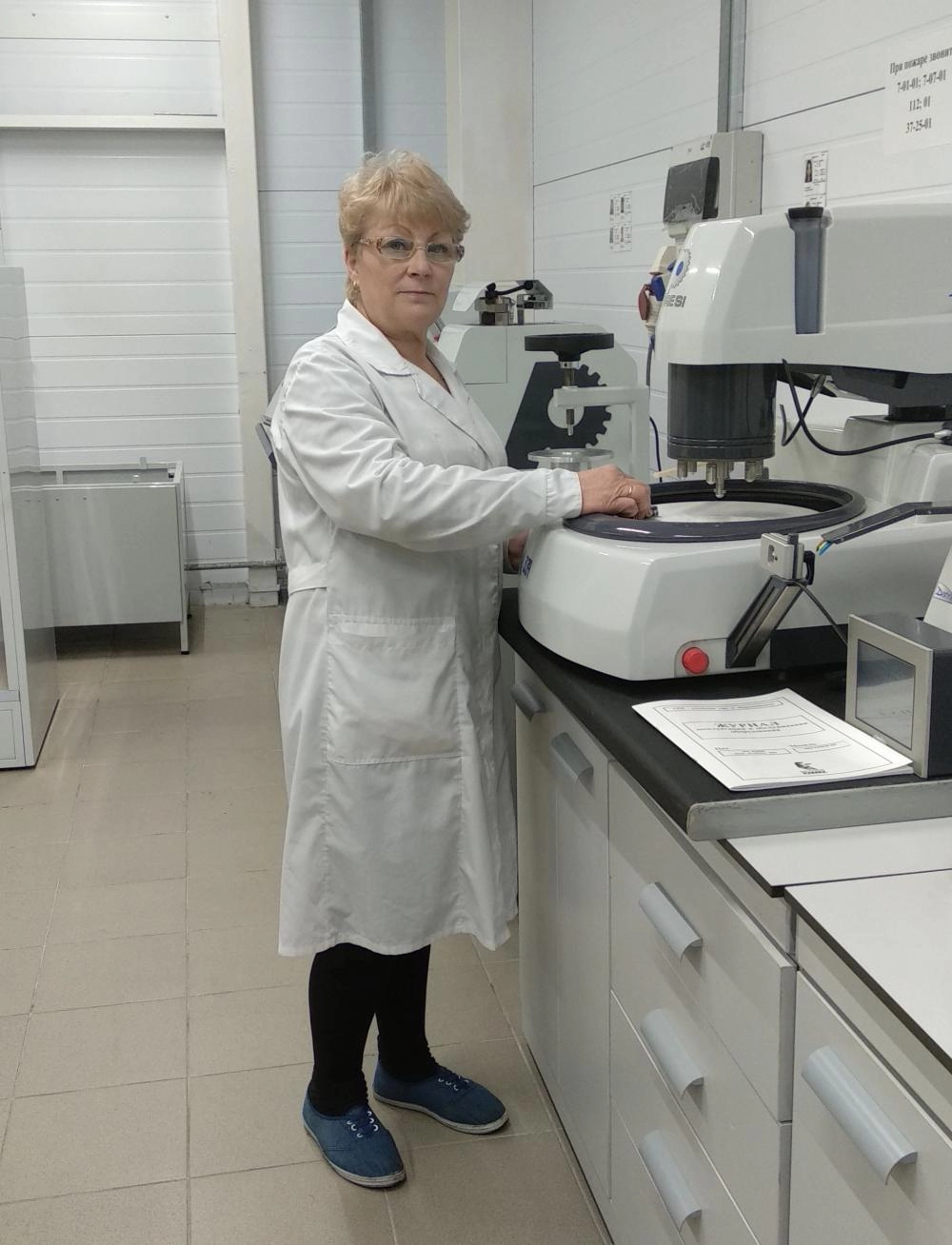
В лаборатории производится входной контроль качества металлопроката, его механических свойств и микроструктуры материала, химического состава.
– При оценке качества микроструктуры выявляются скрытые дефекты, что позволяет исключить проблемы при изготовлении деталей и повысить качество продукции, – пояснила начальник лаборатории аналитических исследований материалов Галина Рябенко.
Прежде чем образец металла окажется под мощным оком микроскопа, его необходимо подготовить к исследованию. Теперь это можно сделать на специальной установке в автоматическом режиме. Другая установка с ручным управлением необходима для того, чтобы доработать шлиф для получения более ясной картины.
Опытный лаборант-металлограф Валентина Евграфова знает, как лучше изготовить образец для исследования. Если детали очень мелкие, их сначала отправляют в автоматический пресс, а потом уже готовят шлиф. Отрезной станок нужен для порезки образцов, в том числе из деталей и узлов, вышедших из строя при эксплуатации для установления причины разрушения.
Строение металла специалисты оценивают под мощным микроскопом с программным обеспечением SIAMS 800. Его возможности позволяют оценить загрязнённость неметаллическими включениями, величину зерна, измерить фрагменты микроструктуры, автоматически выполнить преобразование результатов измерения в результаты анализа. В программное обеспечение включены характеристики металла в соответствии с ГОСТами. От полученных результатов напрямую зависит качество рамы, кабины и многотысячной номенклатуры других комплектующих, которые отправляются на главный сборочный конвейер «КАМАЗа».

Оценили 15 человек
31 кармы