
«КАМАЗ» проведет испытания самосвалов на полигонах одного из лидеров угольнодобывающей промышленности РФ – холдинговой компании «СДС-Уголь».

О тестовой эксплуатации грузовиков договорились четыре стороны: кроме производителя и потребителя в испытаниях примут участие КузГТУ и МГТУ им. Н. Э. Баумана. Соответствующее соглашение было подписано топ-менеджментом всех организаций на автомобильном заводе "КАМАЗа". Научные сотрудники университетов займутся теоретической базой проекта – их задачей станет дальнейшее развитие технологий машиностроения, применяемых при разработке карьеров.
Новая линия на заводе двигателей, установленная в рамках проекта «Передние оси», совсем скоро заработает в полную силу. Автоматизированный комплекс для сборки ступиц с подшипником немецкой фирмы Paul Köster и оборудование, приобретенное в рамках проекта, позволят собирать оси из деталей собственного производства, а не покупать их.
Уже в ноябре, по словам начальника конструкторско-технологического отдела завода двигателей Айрата Лутфуллина, будет увеличение программы выпуска ступиц с необслуживаемым подшипником, предназначенных для модельных рядов 5490 и 54901. Без обслуживания ступичного узла эти автомобили смогут проехать до миллиона километров.

– Линия предназначена для запрессовки подшипника в ступицу. К этому соединению предъявляются серьезные требования. В конструкторской документации оговорены усилия и глубина запрессовки. Также очень высоки требования и к механической обработке самой ступицы, поэтому перед процессом запрессовки перепроверяется посадочный диаметр подшипника, контролируется разность температур подшипника и ступицы и QR-код на подшипнике, – рассказывает Лутфуллин.
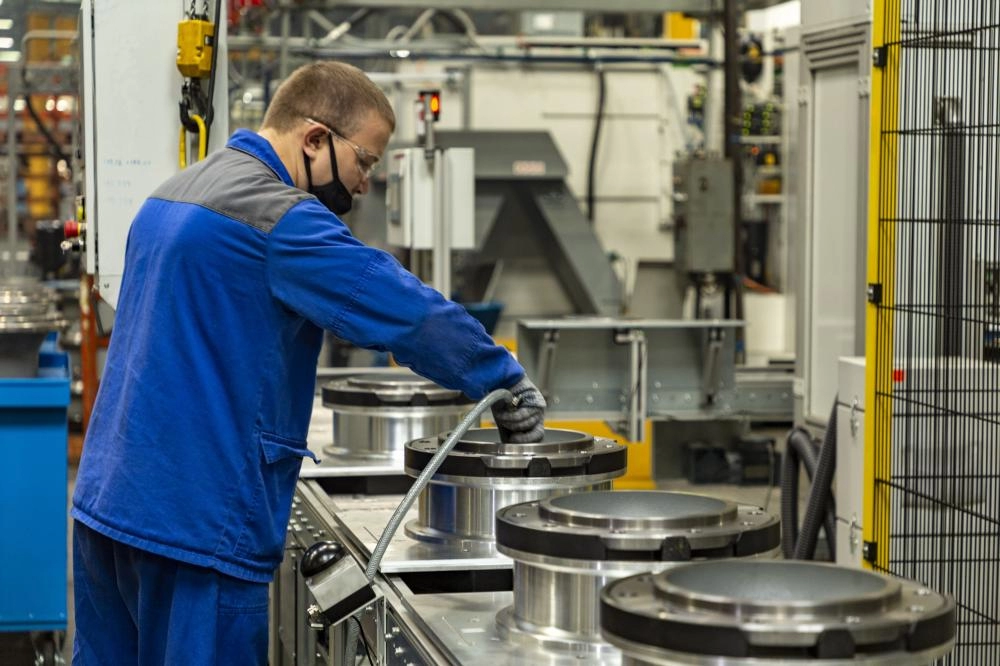
Только при выполнении всех этих условий происходит процесс запрессовки. Он выглядит так: сначала на линию заходит эталон, по нему калибруется система. Наладчик устанавливает ступицы в 13 транспортных паллет, и они поступают на станцию измерения, где происходит проверка качества изготовления детали и сверяется ее соответствие конструкторской документации. Если деталь соответствует установленным значениям на станции запрессовки, паллета останавливается, с накопителя робот берет подшипник, проверяет на нем QR-код и, если все в порядке, устанавливает его на ступицу. Перед установкой подшипника сравнивается температура ступицы и подшипника – разница должна быть не больше двух градусов для исключения погрешности усилия запрессовки. Пресс в новом автоматическом комплексе – с сервоприводом, так что работает бесшумно и точно контролирует и усилие запрессовки, и ее глубину. При соответствии значений на собранный узел наносится свой QR-код.
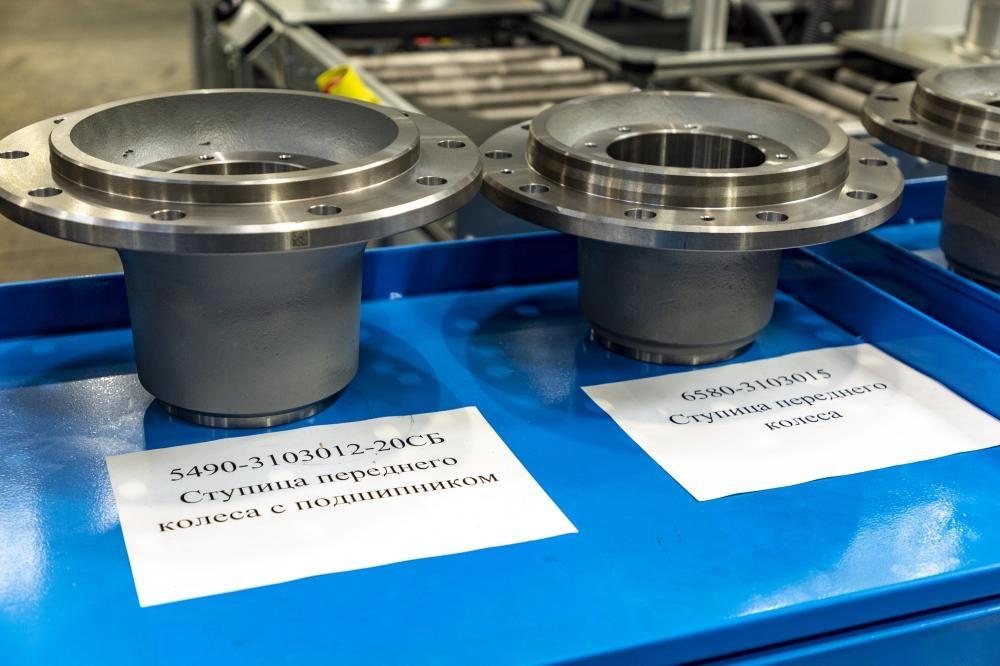
Маркировка происходит с помощью лазера. Зона маркировки находится за защитным стеклом и снабжена системой вытяжки и фильтрации продуктов выжигания. В QR-коде записана модель ступицы, глубина и усилие запрессовки, дата и время выпуска. Эти данные потом на АвЗ считываются при сборке передней оси и заносятся в документацию.
Производительность линии – восемь деталей в час. Она рассчитана на выпуск 25 тыс. машкомплектов передних ступиц. Сейчас линия запущена не на всю мощность, поэтому на ней работает один человек. Ручного труда здесь тоже хватает: нужно загружать подшипники, следить за работой системы и снимать готовые или не соответствующие документации детали. Роборука, как ни крути, человеческую не заменяет, но здорово помогает.
Чистота детали – важный параметр, без которого на производстве не обойтись. От него напрямую зависит качество выпускаемой продукции. Ведь как собирать, к примеру, двигатель, если на масляную неочищенную деталь налипли пыль и грязь? На заводе двигателей об этом знают не понаслышке и о «гигиене» деталей позаботились: в цехах 201 и 113 провели масштабную модернизацию комплекса трех моек.
Необходимость в этом назревала давно: по словам начальника центральной заводской лаборатории технологической точности ЗД Владимира Борисова, старые версии моек работали больше 40 лет каждая. И возраст дал о себе знать: прохудились баки, плохо работали форсунки, подающие воду, нагревательные элементы не давали нужной температуры, а транспортная система износилась и подверглась коррозии.
А без моек не обойтись, ведь детали, которые нужно качественно отмыть, важные – например, это кольцо газового стыка, коромысло клапана и шестерни коробки передач. Прежде при простое приходилось изготовленные детали переносить, а габаритные – перевозить на находящиеся поблизости мойки, а ведь лишнего времени на производстве не бывает. Более того, не каждая деталь подходит к определенной мойке: бывало, детали не влезали или, напротив, проваливались в ячейки транспорта.
Задачу перед исполнителями главный инженер завода поставил серьезную – модернизировать пришлось буквально все.
– Корпус новых моек изготовили из нержавеющей стали – больше никакой ржавчины, да и срок эксплуатации увеличивается, – рассказывает Борисов. – Все приводные валы и детали узлов сделаны из нержавеющей стали или с гальванопокрытием, приборы контролируют и уровень заливки воды и моющего раствора в мойку, и температуру. Цикл обработки теперь составляет две минуты, раньше мойка занимала больше трех минут.
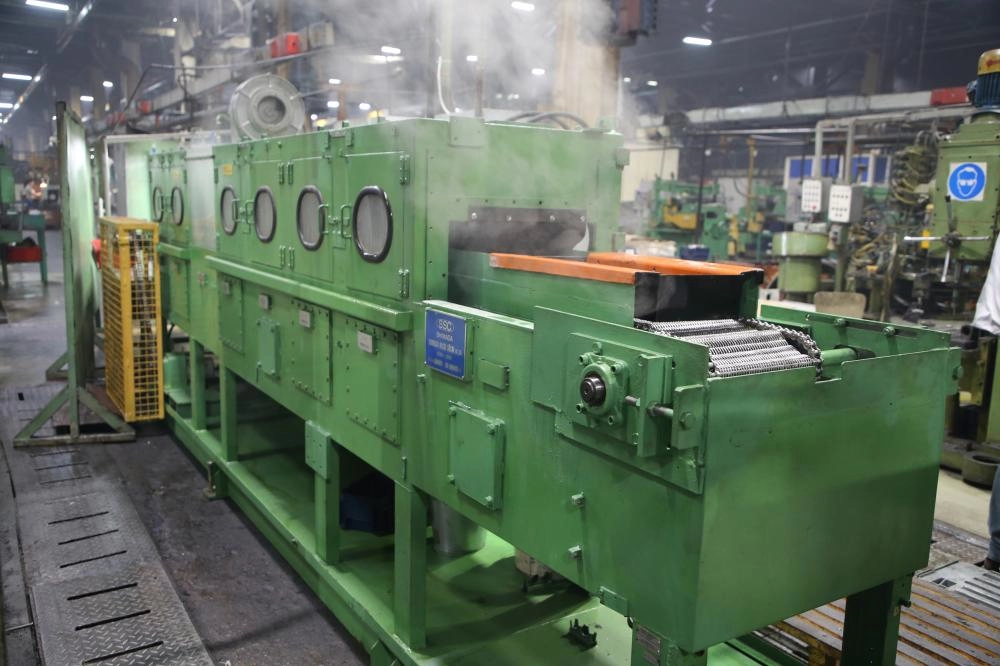
Поменялась и конструкция моек – под каждый вид детали сделали свою систему и одновременно максимально ее упростили. Закупили новые транспортные сети, которые рассчитаны по размеру ячеек на конкретную составную часть будущего двигателя: больше никаких проблем с мелкими деталями, которые в прежнем варианте моек могли провалиться или застрять. Проработали систему промывки, продувки и сушки – на выходе получается чистая, обработанная (в моечном растворе содержатся антикоррозийные компоненты) и полностью сухая деталь.
Работа проделана колоссальная. И все это с минимальными затратами!
– На одну мойку потребовалось порядка 100 тыс. рублей. Часть комплектующих делали на нашем же заводе, – говорит Борисов. – Экономический эффект от модернизации, по нашим расчетам, составит около трех миллионов рублей в год на одну мойку.
Модернизация на этом не закончена: по словам Борисова, до конца текущего года планируется автоматизировать процесс загрузки деталей в моющие машины. Уже продумали и составили схему транспортного агрегата, который будет забирать компоненты и отправлять их «в душ». Это позволит сократить время обработки деталей и снизить потери на транспортировку.

ПАО «КАМАЗ» на базе «НЕФАЗа», своего дочернего предприятия в Нефтекамске (Башкирия), планирует реализовать инвестиционный проект модернизации производства пассажирского транспорта с общим объёмом инвестиций 4,1 млрд. рублей.
В качестве меры по привлечению государственной поддержки проекта рассматривается возможность заключения специального инвестиционного контракта, зарекомендовавшего себя как эффективный инструмент стимулирования инвестиций.
За последние три года объёмы производства ПАО «НЕФАЗ» выросли более чем в два раза, в том числе за счёт роста продаж автобусной техники. Новый проект позволит нарастить производственные мощности, увеличить налоговые отчисления. Предполагаемые сроки его реализации — 2022-2030 годы.
Завод выпускает сразу несколько видов автотехники: самосвальные установки, пассажирские и вахтовые автобусы, электробусы, троллейбусы, ёмкостно-наливную технику, бортовые самосвальные прицепы и полуприцепы. Предприятием освоен широкий модельный ряд автобусов — городского, пригородного, междугородного, автобуса в северном исполнении, автобуса, работающего на метане. Каждый третий российский автобус производится в ПАО «НЕФАЗ». Продукция предприятия зарекомендовала себя как надёжная, даже при эксплуатации в тяжёлых климатических условиях, в более чем 60 регионах России и странах ближнего зарубежья.
В ПАО «НЕФАЗ» целенаправленно осуществляется инвестиционная программа, модернизируется оборудование в цехах, внедряются новые технологии. Объём инвестиций за 2020 год составил 154 млн рублей, за 10 месяцев 2021 года — 251 млн рублей. На эти средства приобретено высокопроизводительное оборудование: установка для лазерного раскроя труб MAZAK (Япония), установка лазерной резки металлов с ЧПУ и двухтандемный листогибочный пресс с ЧПУ производства DURMAZLAR (Турция), токарно-фрезерный станок с ЧПУ производства Doosan Machine Tools (Южная Корея) и др.
Результатом эффективной деятельности ПАО «НЕФАЗ» в 2020 году стала чистая прибыль в размере 288 млн рублей. Годовой показатель EBITDA относительно аналогичного периода 2019 года вырос в 7 раз и составил 622 млн рублей.
За 2020 год отгружено 6 928 самосвальных установок, 2 683 единицы грузовой прицепной техники, 436 единиц ёмкостно-наливной техники, 1 602 пассажирских автобуса, 211 электробусов, 650 вахтовых салонов. Доля новой техники в объёме товарной продукции составила 7,2%.
В 2021 году изготовлены опытные образцы новых моделей пассажирского транспорта — сочленённый электробус КАМАЗ-6292-0000010, электробус с тяговыми аккумуляторными батареями «Микроваст» КАМАЗ-6282-0000121, троллейбус КАМАЗ-62825-0000020 с увеличенным автономным ходом, электробус КАМАЗ-6282-123, автобус НЕФАЗ-5299-0000231-57 в пригородном исполнении в новом облике и водоробус КАМАЗ-6290.
Ожидается, что в 2021 году объём выпуска продукции и услуг ПАО «НЕФАЗ» составит более 30 млрд рублей.
Сегодня основным направлением инвестиционной деятельности ПАО «НЕФАЗ» является реализация инвестпроекта «Увеличение производственных мощностей по выпуску пассажирского автотранспорта до 3 000 единиц в год». Идея проекта заключается в двукратном увеличении производственных мощностей по выпуску пассажирского автотранспорта с 1500 до 3000 единиц в год и организации современного высокотехнологического производства с применением передовых технологических решений в сварочном, окрасочном и сборочном производствах в 2022-2024 годах.
Ещё одним значимым направлением является инвестиционный проект «Развитие производственных мощностей по выпуску самосвальных установок К5 и модернизация самосвального производства в ПАО «НЕФАЗ».
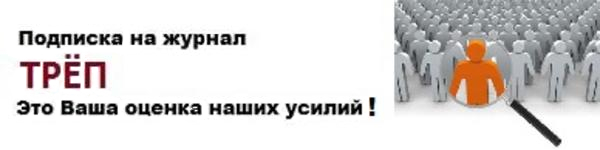
Оценили 18 человек
40 кармы