Продолжая разговор, начатый в первой статье (https://cont.ws/post/363813), всмотримся в некоторые «клочья разорванной» экономики России. Поговорим про то, как Англичанка нагадила Скобелеву и Ржевскому, про пользу от смычки научных мозгов и разумного тарана; об изобретателях, днем работавших мозгами, а по ночам разгружавших вагоны с мотоциклами. И про то, как авиастроители из царства постиндустриала обращаются за лечением к русскому Айболиту: «Залечи, силь ту пле , наши трещинки». А их коллеги из самой исключительной страны открывают в изолированной России Авиационный центр, где, - в отличие от своих центров в других странах - будут не только обучать пилотов, но и вести научные исследования совместно с русскими учеными...
Смешно читать и слышать все более истеричные выпады в адрес «сидящей на нефтяной игле страны-бензоколонки», со стороны наших дражайших «партнеров». Тех самых, что на этой игле в Гегемоны вырвались, а недавно с радостью уселись на грязнущую сланцевую иглу, принесшую некоторым регионам Америки экологический СПИД.
Мало того, постоянно обвиняющие Россию в нелюбви к экологии, нефтегазовые компании Америки в 2011 году сожгли в факелах более 30% всего попутного газа в Северной Дакоте. Согласно данным Всемирного Банка, в США в 2007 году в факелах было сожжено 78 миллиардов кубических футов попутного газа, а в 2011 году – уже 251 миллиард куб. футов. То есть, севшая на СПИДоносную иглу Америка получила рост «производительности» своих газовых факелов на 223% и первое место по темпам этого роста среди всех крупных «факелоносцев» мира.
У нас с Америкой, к счастью, тренды в сфере утилизации попутного газа разнонаправленные.
«Сургутнефтегаз», например, утилизирует почти 100% попутного газа, - благодаря самому большому ГПЗ на 7100 миллионов кубометров сырья в год. Лишь немного отстает от «Сургута» вертикально интегрированная компания «Сибур» с его 95% утилизации. В этом направлении движутся, - хоть медленно, но верно - и другие наши компании.
Конечно, в 2015 году этот показатель (в среднем по стране) составил 87%, не дотянув до 95%, запланированных еще на 2013 год, но при этом он был выше, чем годом ранее (84%). Движение нефтегазовых компаний в этом направлении государство стимулирует кнутом и пряником.
http://bv.com/Home/news/solutions/energy/us-natural-gas-flaring-is-attracting-increased-attention
«Эксперт», № 15, 11 апреля 2016
А кого-то и подстегивать не надо. Например, - человека, получившего совсем недавно Золотую Звезду «Героя Труда Российской Федерации». С 1984 года возглавляющего «Сургутнефтегаз». Трудоголика, живущего там, где и работает его компания. Там же его компания платит и налоги (в отличие от всех других нефтедобывающих компаний, штабы которых прописаны, - и платят налоги – в Москве). Недаром о его компании и самом Богданове жители Сургута говорят с придыханием, и лишь повторяют: «Только бы в Москву не забрали».
Человек чувствует себя счастливым из-за того, что на работу может ходить пешком. И от того, что каждое лето может прикоснуться к своим корням, уезжая на покос к родителям в деревню (название которой стойкая пресс-служба не выдает ни за какие коврижки).
Компания Богданова принципиально не залезает в долги (а значит, - не попала в зависимость ни от каких банков), всегда имеет «под матрасом» несколько десятков миллиардов долларов. А сам Богданов всегда выступает против любой государственной поддержки, то есть, - за конкуренцию.
Досконально знающий все тонкости нефтедобычи (начинавший свою карьеру помощником бурильщика), умеющий планировать работу компании на долгосрочную перспективу, Богданов, конечно же, ценит это качество и у других. О Путине, например, он говорит так:
- Для меня Владимир Путин являет собой образец аналитического ума. Да, это результат его работы в органах госбезопасности. Но, простите, чего мы так пугаемся? Разве не в этих органах были востребованы в свое время самые лучшие головы России? Разве не эти головы обеспечивали России высокий международный престиж?...
http://neftegaz.ru/persons/view/184
--- Не удивительно, что именно Богданов, умеющий считать деньги компании и отлично понимающий, что «дешево» это вовсе не значит – «хорошо», еще в начале 1990-х стал первым крупным заказчиком высокотехнологичной продукции тогда только встававшей на ноги фирмы.
Которая в 1992 году выпустила первые пять тысяч ступеней для погружных нефтяных насосов, впервые в мире изготовленных по уникальной порошковой технологии.
- Первый насос, который опустили в скважину с нашими ступенями, проработал 945 суток. Это было настоящее чудо — насосы с литыми ступенями обычно работали не больше 150 суток, — вспоминает Олег Перельман. — Все сомнения по поводу качества порошковых деталей отпали».
- .... Они [представители «Сургутнефтегаза».] увидели наши порошковые ступени на выставке и заказали сразу 75 тысяч штук с поставкой через три месяца. А у нас на предприятии тогда работало около ста человек, и делали мы всего 20 тысяч ступеней в год, — рассказывает про первый контракт Олег Перельман. — Мы, конечно, на уши встали, задержали заказ месяца на два, но сделали. И наши ступени себя очень хорошо зарекомендовали».
За эти ступени «Сургутнефтегаз» расплатился с фирмой-изготовителем, как тогда было принято, бартером: в адрес «Новомета» пошли эшелоны сырой нефти, которую не так-то просто было продать...
Мотоциклы продавать было проще, но тоже хлопотно:
«Потребителем нашей первой продукции стал Ирбитский мотоциклетный завод, производивший мотоциклы “Урал”, — вспоминает генеральный директор “Новомета” Олег Перельман. — Они тогда делали по сто пятьдесят тысяч мотоциклов в год». Заказчик расплачивался с пермяками натурой. «Днем мы делали втулки из порошка, а по ночам разгружали вагоны с новенькими “Уралами”, чтобы потом развезти их по магазинам», — рассказывает о тех временах Александр Рабинович, директор по науке и новой технике «Новомета».
До недавнего времени в то, что рабочие органы насоса можно изготовить методом порошковой металлургии, не верил почти никто. Кроме горстки упорных ученых, решивших доказать обратное и в начале 1990-х основавших компанию «Новомет». Сегодня «Новомет» с оборотом более 200 млн долларов и тремя тысячами сотрудников входит в тройку ведущих отечественных производителей нефтепромыслового оборудования.
Лидерство это было обеспечено, среди прочих факторов, и еще одним ноу-хау новометовцев, которое дает важные преимущества конечной продукции: чудо-клеем, намертво «спаивающим» металлические детали.
- Процесс напоминает приготовление безе: две половинки этих пирожных точно так же скрепляют кремовой прослойкой. Из цеха склейки лотки с «пирожными» перемещают к печи. Оператор кладет сверху на каждое «пирожное» широкое плоское медное кольцо. В печи медь пропитает пористую структуру порошковой детали и обеспечит конечному изделию необходимую прочность. Обжиг продолжается 14 часов при температуре около тысячи градусов. Спеченные детали с бронзовым отливом от впитанной меди выезжают с противоположного конца печи. Теперь это единая деталь — ступень погружного насоса. Пытаться разорвать бывшие составные части «пирожного» столь же бесполезно, как разламывать цельный металлический брусок. «Шва нет, — с гордостью говорит автор ноу-хау Александр Рабинович. — Деталь стала равнопрочной. Если ударить зубилом — разломается где угодно, только не по месту склейки».
С 2002 года «Новомет» выпускает не просто ступени, а полнокомплектные погружные насосные установки (УЭЦН) для добычи нефти. Цена такой системы на рынке доходит до 100 тысяч долларов.
У «Новомета» собственный инженерно-технический центр, позволяющий разрабатывать спецоборудование, способное работать в агрессивных абразивно- и газосодержащих водонефтяных средах. И не только.
Они еще и вышивать умеют. Лазером
В ходе такого «вышивания» (которое называется «селективное лазерное спекание») происходит создание трехмерного объекта из порошкообразных материалов.
В CAD системе создается электронная модель детали. Программа делит электронную модель на слои толщиной 0,15 мм.
Средняя скорость выращивания детали - 25 мм/час, таким образом, модель размером 200 х 200 х 200 мм выращивается примерно за 10 часов
В общем, сегодня эта молодая пермская компания по своему технологическому уровню практически не уступает американским конкурентам с их 80-летней историей развития погружного насосного оборудования, - фирме REDA. Основанной в начале ХХ века выходцем из России, Армаисом Арутюновым.
Из-за устаревших технологий и дефицита качественных сплавов нефтяное насосостроение в СССР было обречено на отставание.
«Отрасль была очень ограничена в материалах. Помимо этого ее сдерживали производственные технологии: рабочие органы насоса изготавливались литьем в землю, у которого масса минусов: низкая точность формы при сложной геометрии детали, большая шероховатость поверхности. Кроме того, эта технология очень трудоемка и дает много брака, — рассказывает Шарифжан Агеев, заместитель генерального директора по науке ОКБ по бесштанговым насосам, партнера “Новомета”. — А у американских насосов был совсем другой уровень качества — они отливали свои ступени точным литьем из нирезиста. Поэтому во времена СССР мы не могли догнать их ни по качеству, ни по КПД».
Появление на сцене «Новомета» с уникальной порошковой технологией разом сняло эти проблемы. «В отличие от литья в землю порошковая технология обеспечивает гидравлически гладкие поверхности и высокую точность формы», — объясняет Олег Перельман. За счет этого при одинаковой геометрии КПД порошковой ступени всегда выше, чем литой.
Чем страшен для «партнеров» союз русских мозгов, - «Новомета» и ОКБ БН
Сейчас американцы стараются делать все, чтобы наши Кулибины не обошли их на повороте. Специалисты одного из партнеров «Новомета», - ОКБ по бесштанговым насосам (ОКБ БН) - рассказывают, что американцы, например, несколько раз предлагали Агееву (шефу ОКБ) большие деньги только за то, чтобы он не работал с Перельманом.
Логика наших заклятых партнеров понятна: большинство инновационных продуктов пермяки разработали совместно именно со специалистами ОКБ БН, которое с 1950 года являлось ведущим отраслевым центром по погружным электроцентробежным нефтяным насосам в структуре Министерства нефтяной промышленности СССР. За 40 лет до распада страны и отрасли в ОКБ успели сделать и частично испытать сотни разработок — модификации ступеней, электродвигатели и проч. Большая часть этих наработок во времена Союза так и не дошла до скважин. Отчасти из-за дефицита качественных сплавов, отчасти в силу того, что советские заводы осваивали новую технику очень неохотно.
«В ОКБ накоплены колоссальные заделы по ступеням — масса технических решений, которые уже придуманы и опробованы, и результаты испытаний, свидетельствующие о тупиковых путях и неудачных идеях. Благодаря им мы знаем, как не надо делать, а значит, не тратим попусту время и деньги», — рассказывает Олег Перельман, открывший и оценивший этот ресурс еще в конце 80-х, сразу, как только начал заниматься ступенями.
Новометовцы стараются по максимуму использовать заделы, интеллектуальный потенциал и опыт инженеров ОКБ. К примеру, наработки по ступеням для насосных установок малого диаметра — 4-й габарит (наружный диаметр 86 мм) и 3-й габарит (наружный диаметр 81 мм) — были сделаны в ОКБ БН еще в 80-х, однако до «Новомета» отечественные производители такую технику не выпускали, ограничиваясь набором стандартных габаритов: 5 (92 мм), 5А (103 мм) и 6 (114 мм).
Между тем существует достаточно большой фонд скважин малого диаметра, которые первоначально предназначались для разведочных или ремонтных целей, однако в периоды высокой конъюнктуры нефтяного рынка из этих скважин выгодно добывать нефть. Так, первую малую установку 3-го габарита у пермяков приобрела ТНК-ВР, чтобы разрабатывать бывшую разведочную скважину. В разряд скважин малого диаметра переходят и обычные скважины, где на прохудившиеся обсадные колонны ставят металлические заплаты, после чего насосы стандартных размеров туда уже не проходят. Не имея оборудования для эксплуатации таких скважин, нефтяники их попросту бросали. Теперь это рынок для инновационных продуктов «Новомета», и конкурентов в этой нише у пермяков пока нет.
«Эксперт», № 50, 2012
https://www.novomet.ru/rus/company/technology/rapid_prototyping/
http://www.sdelanounas.ru/blogs/40533/
--- «Роснефть», собранная государством за последнее десятилетие практически с нуля, по итогам 2015 года подтвердила статус крупнейшей публичной нефтегазовой компании, добыв рекордные 254 миллиона тонн нефтяного эквивалента. Свободный денежный поток «Роснефти» в прошлом году превысил 12 миллиардов долларов, а чистый долг сократился с 43, 8 миллиарда долларов до 23, 2 миллиарда долларов. И это, - в условиях санкций и худшей за десятилетия рыночной конъюнктуры.
Что касается западных компаний, то такие мажоры, как BP, Shell, Chevron, Total, объявили о сокращении инвестиций в добычу еще в 2014 году, а в 2015 году они произвели дополнительные сокращения еще на 10-20%. «Роснефть» же, предвидя дефицит нефти именно из-за такого сокращения инвестиций другими компаниями, в 2015 году увеличила количество вновь введенных скважин на 15%.
И, кстати, о птичках, - о себестоимости добычи нефти. Она у «Роснефти» в два раза ниже, чем у других российских нефтяников, и в 4-5 раз ниже, чем у западных мажоров.
В своем недавнем выступлении в Питере Сечин назвал ее значение: 2,1 – 2,7 доллара (?!!!).
http://expert.ru/expert/2016/24/obgonyat-snova/
--- Экономист по образованию, Никита Агеев в начале 2000-х вместе с отцом, бывшим дипломатом, консультировал российских ученых, желавших продвигать технологические разработки в Китае. Одна из технологий заинтересовала Агеевых, и они потратили $200 000 на покупку патента и опытной установки-генератора.
Плазменная прочистка нефтяных скважин позволяет увеличить их продуктивность как минимум на десятки процентов, а в некоторых случаях — на 200–300%. В скважину опускается труба, оснащенная цепью конденсаторов. При подаче энергии, особая проволока на конце трубы за тысячные доли секунды переходит в состояние плазмы, которая моментально превращается в газ, создающий в замкнутом пространстве огромное давление. Возникает ударная волна, и внутри пласта на расстоянии до 1500 м образуется сеть трещин, облегчающих поступление нефти в скважину.
То есть, когда консерваторы в нефтяных компаниях расчавкают вкуснятину этой технологии, сопоставимой по эффекту с гидроразрывом пласта, - но в 10 раз дешевле! - эта технология, в условиях заморозки нового бурения из-за низких цен на нефть, сможет получить широкое распространение.
Созданная Агеевыми компания «Новас Энерджи Сервис» начала вплотную заниматься плазменно-импульсной технологией, которую, как оказалось, можно приспособить под разные задачи. Но чтобы понять это, компании пришлось провести десятки полевых испытаний, в том числе не слишком удачных.
Романа Абрамовича заинтересовала не только прочистка нефтяных скважин, но и идея, которую Агеев начал обдумывать, — использовать плазменный взрыв для добычи метана и дегазации угольных пластов с целью повышения безопасности на шахтах. Компания «Георезонанс», созданная для вывода на рынок технологии работы на метановых месторождениях, получила $700 000 на НИОКР. Около $2 млн Абрамович вложил в Dewasi, созданную для продвижения такой же технологии в Китае. А в сентябре 2015 года он выделил $1 млн «Новас Энерджи Сервис», на которую были переведены все патенты и контракты по работе на вертикальных нефтяных скважинах.
За сентябрь — декабрь 2015 года «Новас Энерджи Сервис» заработала около 5 млн рублей, не считая стоимости выполненных и не оплаченных на конец года контрактов (еще 2,5 млн рублей). В числе ее клиентов, например, «Татнефть» и «Русснефть».
Несмотря на кризис и падение цен на нефть, «Новас Энерджи Сервис» планирует за 2016 год получить контракты на 30–50 скважин в России и 10–20 — в Китае, Малайзии, Кувейте, Бахрейне, Таиланде и Индии. Стоимость контракта в России теперь редко превышает $15 000, за рубежом она может доходить до $100 000.
http://www.forbes.ru/svoi-biznes/startapy/318829-povyshayushchee-davlenie-abramovich-vlozhilsya-v-plazmenno-impulsnuyu-te
--- Отвечая на вопрос: «Во что бы он вложил сейчас 1 миллиард долларов, если бы он у него был ?» - подумав и вздохнув, Поляков отвечает: «Развивал бы только наш сельскохозяйственный сегмент: самая стабильная и доходная отрасль».
Вот так завершает интервью с главой одной из российских фирм неполживый рупор семейки Прохоровых, - «РБК» - в номере за июнь 2016 года.
Что же это за фирма такая, у которой, судя по печальным вздохам ее босса, дела совсем швах, и которую так трогательно, - просто от души - жалеет РБК ?
- В декабре 2015 года мировой сапфировый рынок был потрясен известием: японская компания Kyocera покидает рынок искусственного сапфира, не выдержав конкуренции. Новость удивительна тем, что еще десятилетие назад многоотраслевой японский гигант, с неограниченными финансовыми и инженерными возможностями, занимал половину этого перспективного рынка.
--- Эти десять лет мы воевали в том числе с этой компанией. Надо признаться, они держались очень хорошо, все-таки у японцев технологии и менеджмент на очень высоком уровне. И вот под занавес года мы их полностью выбили с рынка. То есть они были вынуждены закрыть завод, перевести сотрудников на другие направления. Это была очень сложная борьба», — признается Олег Качалов.
По итогам победы завод «Монокристалл» (подразделение принадлежащего Полякову концерна «Энергомера») вместе с белгородской промплощадкой занимает около 30% мирового рынка сапфира, и это первое место. Отрыв от ближайшего конкурента — более 10 процентных пунктов. Остальной рынок поделен более чем десятком производителей камня по всему миру.
Если не вдаваться в подробности, то ответ на вопрос, как же россиянам удалось обогнать иностранцев, лежит на поверхности: на всех установках для выращивания кристаллов стоит шильдик «Сделано в России». Эти установки производят на сестринском предприятии «Монокристалла».
Для того чтобы выйти на нынешний уровень, «Монокристаллу» потребовалось 15 лет и более 200 млн долларов инвестиций.
В результате, летом 2015 года в Ставрополе вырастили кристалл сапфира массой 300 килограммов. Эксперты уже заявляют, что применение сверхбольших кристаллов сапфира способно ускорить развитие многих высокотехнологичных отраслей.
«Нас не устраивает преимущество по технологиям на 10 или 20 процентов. Нам необходим разрыв в разы, и этот разрыв мы не просто поддерживаем на протяжении последних нескольких лет, но и уходим вперед», - говорит генеральный директор «Монокристалла» Олег Качалов.
«РБК», июнь 2016, стр. 87
https://etokavkaz.ru/sekret-firmy/vlastelin-kamnei
http://expert.ru/expert/2016/13/v-epitsentre-sapfirovoj-revolyutsii/
--- В 2000 году светодиоды на подложках из монокристаллического сапфира были еще в диковинку. Такие структуры групповым способом выращивают на одной общей подложке, - вэйфере, но потом весь этот массив нужно разделить на отдельные диоды – чипы. Подложки были размером в один-два дюйма, а вот величина отдельного диода не превышала нескольких сотен микрон. И этих чипов с одной подложки должно было получаться сотни тысяч. Для чего нужно было произвести, - с очень высокой точностью – очень много разрезов.
Для этой цели ученые из фирмы «Мултитех» придумали машинку лазерной резки сапфировых вэйферов по технологии IntroScribe, которая была испытана, - с великолепными результатами – в 2004 году. В патентовании опыта у ученых не было, так что возились они с ним очень долго. И в этот период к ним заявились трое представителей фирмы с восточного острова.
Ученые были рады вниманию иностранцев, и, считая, что общение с этими восточными людьми должно проходить в духе «Мир, Дружба, Суши», поделились с гостями секретами своей чудесной машинки. Оказалось, что зря...
«Эксперт», № 20, 2016
--- В 2010 году Челябинский трубопрокатный завод открыл новый цех по производству труб мощностью 900 тысяч тонн труб в год, в который было вложено 880 миллионов долларов.
На общем фоне его выделяли две вещи. Во-первых, у цеха было «имя» — «Высота239», данное в честь географической точки, на которой построено здание. Во-вторых, и главных — абсолютно новый подход к работе. Среди его внешних «атрибутов»: современный интерьер и почти стерильная чистота — все это на территории площадью в 14 футбольных полей.
«Сначала подумал, что попал то ли на театральную площадку, то ли в Диснейленд», — сказал на открытии производства Владимир Путин.
Что же касается «атрибутов» содержательных, то «Высоту239» стали называть не иначе, как «революцией в отечественной и мировой металлургической отрасли». Новейшие технологии, инновации, максимальная автоматизация процессов, экологическая безопасность — в трубопрокатном цехе есть всё, о чем только может мечтать современное производство.
Для обозначения новых подходов к работе был даже придуман специальный термин — «белая металлургия». Как объясняют его авторы, это определение создано на контрасте с металлургией «черной», читай, «грязной».
И еще одна важная составляющая нового взгляда на металлургическую отрасль — кадры. Подавляющая часть тех, кто сегодня работает на «белых» производствах челябинского металлургического холдинга (кроме «Высоты239», это «Железный Озон 32» и «Финишный центр») — это сотрудники с высшим образованием. При этом, признаются в холдинге, только после запуска суперсовременных цехов стало понятно, что «белых металлургов» не готовит ни одно учебное заведение. Чтобы восполнить этот пробел в компании запустили собственную корпоративную программу.
http://www.4thmedia.org/2016/04/now-russia-makes-an-organic-revolution/
--- В 2010 году в Красноярске была основана компания, команда которой уже в 2011 году нащупала идею, позволившую ей разработать прорывную для мировой металлургии технологию. С ее помощью можно решить важные проблемы отрасли — снизить процент брака при литье крупногабаритных алюминиевых слитков и устранить дефекты в изделиях из алюминия. Кроме этого, технология позволит отливать слитки из новых сплавов, то есть шагнуть вперед в производстве готовых изделий из алюминия.
У решившего открыть эту компанию Евгения Павлова к тому моменту за плечами были аспирантура по электротехнологиям и работа в научно -производственном Центре магнитной гидродинамики.
— После тщательной проработки и оценки идеи мы решили продвигать ее [технологию] на мировом рынке: увидели, что она способна решить комплекс проблем, которые есть у каждого крупного производителя алюминия и изделий из него. Представьте, что вы варите суп: сложили в кастрюлю все необходимые ингредиенты, но не перемешали их. Вряд ли суп получится вкусным, если компоненты не распределить по кастрюле. Что-то подобное происходит и при литье габаритных алюминиевых слитков. Из-за того, что в сплаве присутствуют компоненты различной плотности с разной температурой плавления, внутри они распределяются неравномерно. По этой причине появляются дефекты — трещины, пористость. Исключить их существующие технологии не позволяют. Наша же разработка выравнивает состав и температуру при застывании, лишая конечный продукт дефектов.
Интерес к разработке уже проявили более десятка зарубежных компаний-производителей алюминия. В их числе Alcoa, Chalco, Hydro, BHP Billiton, Dubal и другие. Ожидается, что среди отечественных производителей одними из первых возможности технологии будут использовать РУСАЛ и Каменск-Уральский металлургический завод (ОАО «КУМЗ»). И список продолжает пополняться.
Успех этот не свалился на фирму с Небес.
Павлов поясняет: эта проблема актуальна для алюминиевой отрасли всего мира — а разработка красноярцев значительно снизит процент брака или устранит его вовсе. Дефекты слитка неизбежно приводят к тому, что и конечная продукция, полученная из таких алюминиевых сплавов, будет некачественной. Именно так произошло с AirBus 380: из-за дефекта слитка на крыльях самолета образовывались трещины, отваливался кожух двигателя. Как следствие, производитель лайнера был вынужден отвечать за брак и терпел миллиардные убытки.
— Поэтому мы обратились к ведущему европейскому производителю деталей для AirBus с предложением устранить с помощью нашей технологии подобные дефекты. При этом договорились, что наше оборудование будет оплачено только в случае положительных результатов испытаний. Так началась дорогостоящая рискованная работа по созданию новой технологии за счет собственных средств.
Испытания технологии (в Швейцарии) заняли полгода — с апреля по октябрь 2015-го. Отлитые слитки распиливали, проводили рентгеноструктурный анализ каждого среза. Накопленная за полгода статистика подтвердила: разработанная красноярцами технология работает — слитки однородны по своему составу, в них нет трещин и пористости. Кроме этого, скорость литья с использованием технологии увеличивается до 80%: благодаря электромагнитному перемешиванию сплав кристаллизуется быстрее.
Швейцарский завод-производитель, как это и было прописано в договоре, приобрел у красноярцев технологию и оборудование. В свою очередь разработчики технологии, имея на руках фактические результаты, начали выводить свое детище на мировой рынок.
... 3 июня 2016 г. американский авиастроительный концерн Boeing открыл Авиационный учебный и научно-исследовательский центр в «Сколково». Это первый из более чем десяти Центров, что компания имеет во всем мире, в котором одновременно с обучением коммерческих пилотов будет осуществляться исследовательская деятельность.
Научно-исследовательский центр сосредоточится на ведении проектов в сфере гражданской авиации совместно с российскими университетами и организациями. Планируются работы в области решения актуальных проблем авиационной науки, безопасности полетов, металлургии ( здесь почти наверняка, по-моему, постараются сотрудничать и с компанией «УниМет» Евгения Павлова - shed), создания агрегатов и частей.
В учебном центре установлены полнопилотажные тренажеры Next-Generation 737 и 777. Оставлено место еще для двух тренажеров, в том числе, еще одного Next-Generation 737, производства российский компании «Кронштадт». В тренажере использованы как российские технологии, так и технологии компании Boeing — и все это также впервые.
... среднерыночная цена установленных в центре тренажерных комплексов составляет $10-15 млн.
Удивительно ли такой интерес «исключительных» к России ? – Совсем нет. Ведь в «сияющем граде на холме» квалификация Работяг (и воротничками разного цвета), неуклонно падает (о чем мы писали здесь: https://aftershock.news/?q=node/409208), что хорошо видно на примере и американских авиастроителей. У самолетов которых даже глохнут двигатели во время полетов, или отваливаются куски самолета. Как в случае с продукцией «Боинга» и их поставщиков-мажоров.
Двигатели General Electric (GE) ( фирмы, где больше половины прибыли сейчас идет от финансовых оперций, а не от «грязной» работы с железом - shed ), которыми оснащен Боинг 787, глохнут прямо в воздухе.
2016 год
29 января один из двух двигателей модели GEnx-1B PIP 2 Боинга 787 Japan Airlines неожиданно заглох в то время, когда самолет находился на высоте 6096 метров. Пилотам пришлось сажать самолёт с одним двигателем.
Власти Америки озаботились проблемой двигателей только в отношении 49 самолетов, находящихся непосредственно в США. Изготовитель двигателей заявил, что на этих самолетах двигатели будут заменены к сентябрю. При этом в 29 авиакомпаниях мира летает в общей сложности 175 самолетов Боинг 787. – Пусть себе так и летают ?
2014 год
В марте 2014 года фирма заявила, что должна проверить около 40 еще не поставленных Dreamliner,- из-за трещин в крыльях.
2013 год
В середине октября от Боинга 787 d'Air India в полёте отваливается кусок самолета размеров 1 метр на 2,5 метра. Пилоты заметили это только при приземлении. В самолёте находилось 148 пассажиров.
http://newslab.ru/article/699565
http://aviator.guru/blog/43922713331/Boeing-otkryil-aviatsionnyiy-uchebnyiy-i-nauchno-issledovatelski
http://sdelanounas.ru/blogs/78575/
https://aftershock.news/?q=node/391448
--- Российская компания Tesso вышла на рынок промышленного кондиционирования с громким заявлением, что их система сокращает потребление электричества в десять раз.
В десять раз меньше и капитальных затрат, расходов на сервисное обслуживание. «Например, на охлаждение ста квадратных метров обычные кондиционеры тратят 11 киловатт-часов электроэнергии, а Tesso — 1,2 киловатт-часа», — объясняет один из основателей компании Игорь Горячев. Причем кондиционеры могут работать напрямую от солнечных батарей, не нужен даже преобразователь.
С середины 1990-х и до 2012 года Tesso сотрудничала только с РЖД — в компании разрабатывали системы кондиционирования для вагонов, трансформаторов и электрооборудования Московского метрополитена.
Выручка компании за 2015 год — 2 млн долларов. План на 2016 год — 16 млн. Общий мировой рынок компания оценивает в 100 млрд долларов, причем ожидается, что его объем будет ежегодно увеличиваться на 10%.
Процесс охлаждения в варианте Tesso мало отличается от природных процессов. Искупались вы в море, вышли, ветер вас обдул, вода испаряется, температура падает — и вот вам уже холодно.
Уникальность продукции Tesso - в применении косвенного метода охлаждения. В кондиционерах компании нет соприкосновения воды и воздуха. "Наш кондиционер состоит из пластин и вентилятора. Вентилятору нужно немного - порядка 10% от потребностей общей системы кондиционирования. Вентилятор засасывает воздух снаружи и подает его охлажденным в помещение. Хладагентом выступает обычная вода", - рассказывает Горячев.
Михаил Маркман, нынешний технический директор Tesso, еще в 1990-е, будучи студентом, решал задачу: как снизить электропотребление в вагонах РЖД в условиях, когда на смену открытой форточке приходили технологии, пожирающие электроэнергию. Больше всего ее уходило в точке преобразования постоянного тока в переменный, на котором работал компрессор. Получалось, что система подготовки тока раза в три дороже системы кондиционирования, а это 20% стоимости вагона.
Было найдено решение, - работать без фреона и компрессора... Вода в поездах есть, а нужно ее немного – около литра на «киловатт холода».
ОАО «РЖД». Компания TESSO является официальным поставщиком кондиционеров во все реконструируемые вагоны.
УП «Московский метрополитен» Вся система кондиционирования для трансформаторов и
электрооборудования оснащена системами охлаждения TESSO
«Северсталь» и «Златоустский металлургический комбинат». На данных предприятиях решена проблема охлаждения крановых кабин в горячих цехах, непосильная другим типам оборудования.
- Мы 15 лет работали на одного клиента, а в 2012 году решили, что пора покорять мир. Создали новую компанию и начали действовать, — говорит Горячев. Самые заманчивые перспективы сейчас открываются перед Tesso на Ближнем Востоке. ... В этом году я в качестве одного из 20 делегатов России был в Саудовской Аравии. Сейчас арабы рассматривают наши кондиционеры, чтобы обустроить новый остров в Дубае, — рассказывает Игорь.
http://expert.ru/expert/2016/21/myi-iz-holodnyih-mest-i-znaem-pro-holod-vse/
http://energosber18.ru/energosberezhenie/propaganda/mirovoi-opit/we-are-from-a-cold-place-and-we-know-all-about-the-cold.html
http://tessopro.com/
https://vc.ru/p/tesso
--- Основа любого антипригарного покрытия — фторполимер ПТФЭ (политетра-фторэтилен). Но в процессе синтеза ПТФЭ по западной технологии используется перфтороктановая кислота. Незначительные количества этого токсичного вещества могут оставаться в полимере и после окончания технологического процесса.
Российские предприниматели, купившие в 1998 году небольшое предприятие, выпускавшее сковородки с антипригарным покрытием на площадях питерского «Красного Выборжца», решили делать посуду, которой им будет приятно и не страшно пользоваться самим.
Первые полимерные суспензии на основе нетоксичного отечественного ПТФЭ появились только в 1990-х. Со своей рецептурой такой суспензии на рынок вышла и маленькая фирма «Сталафлон», созданая в Екатеринбурге Алевтиной Ладовской. Она одной из первых предложила НМП - «Нева металл посуде» (так назвали компанию, которой достались активы обанкротившегося посудного заводика) попробовать ее разработку в качестве антипригарного покрытия. Питерцам предложение Ладовской понравилось. Сделанная на водной основе суспензия под названием «сталафлон» была абсолютно нетоксична.
Почти через 20 лет, благодаря усилиям всей команды НМП, и, в особенности, талантливому химику, - Марии Титовой, проработавшей в оборонке 40 лет, фирма стала единственной в мире компанией, выпускающей посуду высшего стандарта безопасности.
«Покрытие, которое мы используем, относится к самому высокому, четвертому, классу безопасности. Лучше уже не бывает, — подчеркивает Ольга Иванова, коммерческий директор “Нева металл посуды”. — Кроме нас, наносить это покрытие не умеет никто»...
http://www.sostav.ru/articles/2010/08/18/ko2
«Эксперт», № ?, 18 августа 2010
--- Про синие «ножки Буша» некоторые из нас уже забыли, а ножек этих совсем еще недавно в Россию продавали каждый год на 1 миллиард долларов. Помню, с каким трудом государство от этих ножек отбивалось, как у нас в области, например, со скрипом шло развитие собственного птицеводства (с помощью голландцев). Сейчас свои потребности в качественном курином мясе Россия обеспечивает полностью. Свинина теперь в основном тоже своя, российская.
А за самый трудный сектор животноводства, - за разведение крупного рогатого скота (КРС) мясных пород - страна взялась в 2010 году.
Когда владельцы компании, уже создавшей в России "свиную" империю, замахнулись и на неосвоенный сегмент — производство говядины, заявив, что если проект в Брянской области будет запущен, то их фирма станет лидером и в этом сегменте:
- Во всем мире так. Сначала развивается птицеводство, поскольку период выращивания птицы — всего 42 дня. Потом свиноводство — шесть месяцев, и, наконец, КРС, где животное растет 1,8 года... Но чтобы крупномасштабные проекты развивались, их должно поддерживать государство. Надеюсь, оно к этому уже готово.
К изумлению многих, государство оказалось готово, а два брата-акробата смогли ответить за базар. Несмотря на то, что производство мясного КРС — самый тяжелый сегмент отрасли:
- Всегда, даже в советские времена, он находился в зачаточном состоянии. Нет опыта, специалистов. Сейчас работают небольшие предприятия, но они не очень успешны. Проект, который задумал "Мираторг",— очень сложный. Они будут первопроходцами...
Да еще какими первопроходцами.
Проект агрохолдинга перекрывал все мыслимые полеты фантазии. Казалось, что страна вдруг вспомнила свое тучное крестьянское прошлое и с ходу рванула в космос… агрокосмос.
200 тысяч гектаров залежных земель в Брянской области были выкуплены под посевы многолетних и однолетних трав, зерновые культуры, кукурузу и подсолнечник. Теперь всякий путешественник, отправляющийся из Брянска, наблюдает невиданные картины: поля, фермы, хозяйства, офисы, бойни, элеваторы, кормовые базы... И десятки тысяч черных, как паровозы, коров, растекшихся по полям говяжьего кластера. Это крупнейшее в Европе стадо абердин-ангусов, привезенных из Австралии и Америки, — 155 тысяч голов, круглый год пасущихся на открытом воздухе.
Первая российская зима, действительно, обошлась без потерь. Сотрудники фермы с восхищением рассказывают, как в 30-градусный мороз умные животные выстроились плотным треугольником: «Мерзнут крайние, а в центре нет – им уже тепло. Потом они меняются местами, и так выходит, что они друг друга согревают» (как пингвины shed).
Прямо в поле коровы и телятся. На середину 2012 года появились две тысячи голов прибавления. Это первые «абердинчики» с российским гражданством. ..
В настоящее время (2016 год) на пастбищах компании в Брянской и Калининградской областях содержится уже более 360 тысяч голов этих животных.
Стоимость проекта компании «Мираторг» (с окупаемостью примерно в 12 лет) почти такая же, как у металлургического проекта «Высота 239», - 800 миллионов долларов.
Всего за три последние года импорт Россией мяса снизился с 2,2 млн тонн до 720 тыс., а объем производства вырос на десятки процентов. АПХ «Мираторг» внедрил в России лучшие мировые технологии мясного животноводства, освоил сложный процесс воспроизводства лучшего генетического материала (несмотря на наличие соответствующей федеральной программы, это не удавалось никому). Его производство росло динамичнее, чем у всех игроков вместе взятых, в среднем на 40% в год, и к 2020-му компания собирается достичь показателя 1,2 млн тонн мяса в потребительской и индустриальной упаковке, из которых 25% будет экспортироваться в 52 страны мира.
Качество продукции «Мираторг» уже признали такие требовательные рынки, как страны Персидского залива и Евросоюза.
«Эксперт», № 15, 11 апреля 2016
http://www.kommersant.ru/doc/1310339
http://ruspioner.ru/cool/m/single/4192
http://mir24.tv/news/society/5237262
http://www.restoclub.ru/spb/review/foodcollection/pjat-mifov-o-premialnoj-govjadine-bljek-angus
http://expert.ru/expert/2016/17/miratorg-s-zadnego-vhoda/
--- Шугурова сразили мальцевские слова: «Какой создала природа почву, такой она и должна быть. Рыхлить можно, а переворачивать нельзя». Он обмозговал со всех сторон идеи ученого, кое-что изменил, и с 1983 года в «Пугачевском» перестали пахать землю и полностью отказались от химии.
... Описывая свою технологию, чаще всего Шугуров употребляет слово «просто». Просто посмотрели, на какой земле растения хорошо себя чувствуют и в засуху, и в дожди, и увидели, что в естественной среде. А это просто потому, что в природе органические остатки удерживают влагу и дают питание растениям там, где они его ищут — у поверхности: здесь больше воздуха и тепла и есть условия для жизнедеятельности микроорганизмов.
- Природа ведь оставляет на поверхности земли листья, стебли, она же их не зарывает на глубину, правильно? — продолжает Анатолий Иванович. — Вот и мы не зарываем. Озимые и яровые убираем комбайнами с измельчителями. Измельченная солома в земле становится носителем углерода — материала для образования гумуса и углекислоты, улучшающих условия воздушного питания растений. Она — как одеяло, под ним растения переносят засуху лучше, чем на черной голой отвальной земле. По нашей технологии выходит, чем больше урожай, тем богаче земля. А то вот говорят, что однолетние растения не обогащают землю... Еще Терентий Семенович Мальцев доказал, что обогащают. Но никто не верил. И я все думаю: неужели они такие идиоты были, что ему пришлось столько лет это доказывать? Всю жизнь! ( с «дикарями» из племени «консо» (см. мою статью по Эфиопии: https://aftershock.news/?q=node/29307#comment-361653 ) Шугурову было бы легче общаться: они на своих холмах-крепостях фактически по такой же технологии несколько столетий работают, - палками-копалками рыхлят только верхний слой - shed )
Урожайность выросла в первый же год: 15 центнеров с гектара против 10. Лет через пять подошли к рубежу 20–25, потом — 30. А сейчас получают за 40 центнеров. Это наивысший показатель по России, столько собирают на Кубани. А вот в Канаде в 2009 году собрали пшеницы по 25 центнеров с гектара.
При этом зерно по новой технологии получается намного дешевле. Если по Приволжскому федеральному округу себестоимость в 2009 году была 2,5–2,6 рубля за килограмм, то в Пензенской области, начавшей внедрять новую технологию, — 2,3, в Мокшанском районе, перешедшем на нее почти целиком, — 1,8 рубля, а в «Пугачевском» — 83 копейки.
Например, с начала июня 2010 года)в Пензенской области не выпало ни капли дождя. Температура держалась на уровне 36–40 градусов. В среднем урожайность в хозяйстве Шугуров составила 16–18 центнеров с гектара при себестоимости 1,5 рубля за килограмм...
В Приволжском федеральном округе урожайность на конец июля составила в среднем 9,6 ц/га. А на площади около 10,7 млн га в пострадавших от засухи субъектах РФ вообще «произошла гибель сельскохозяйственных культур».
http://expert.ru/expert/2010/32/nepahanoe_pole/
--- Сотрудничество и дружба ученых Петра Скобелева (гражданина России) и Георгия Ржевского (гражданина Англии) подняли самарскую научную школу мультиагентных систем (МАС) до космических высот. В прямом смысле этого слова. Так как сейчас МАС-технология НПК "Разумные решения" (основанная на принципе «мыслящего роя») управляет, например, программой полетов, грузопотока и расчета ресурсов российского сегмента Международной космической станции.
Рожденная российскими мозгами МАС как часы работает на благо лондонского такси. "Представьте себе, - говорит Георгий Ржевский, - две тысячи машин и два вызова ежесекундно, и при этом независимо от присущих мегаполису пробок, , такси прибывает к заказчику в течение 15 минут".
Этот проект был реализован Скобелевым и Ржевским в рамках корпорации Magenta Technology, в 2000 году зарегистрированной в Лондоне. Ученым принадлежало по одной трети активов стартапа, оставшаяся доля была у их партнера Майкла Питерса, который занимался продвижением продукции.
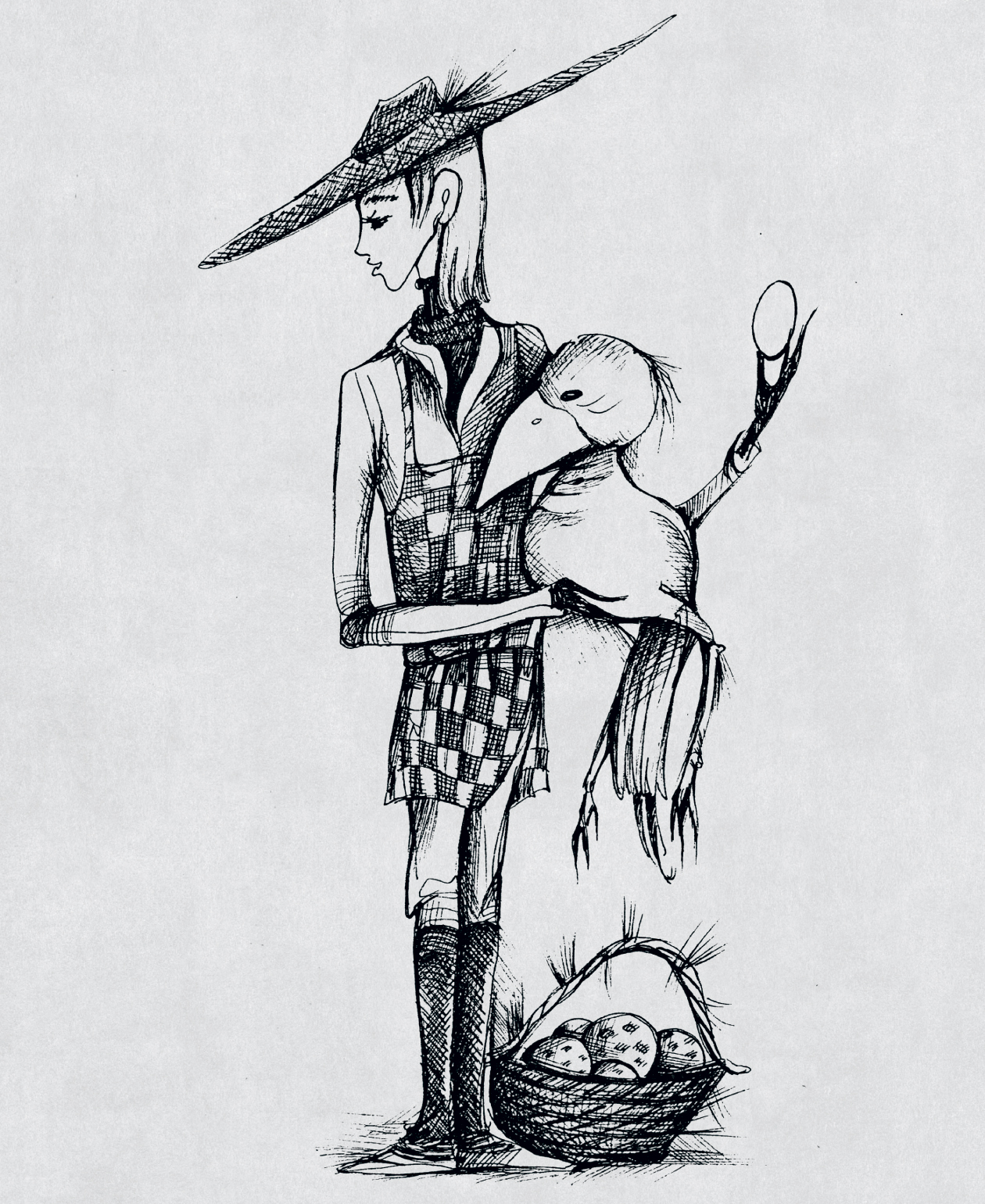
Ну, а дальше все постепенно пошло по сценарию сказки о курице, несущей золотые яйца. Англичанка, - она ведь такая, всегда готова стянуть все, что под руку попадет. Мимо пары-тройки золотых яиц, произведенных доверчивыми русскими, подданные Ее Величества, ессно, пройти не могли.
Скобелев рассказал, как на совете директоров английские партнеры ответили на его возмущение коварством «партнеров»: "Слушай, что ты обижаешься? Ты же понимаешь, мы строим английскую компанию, а не русскую. В ней русские никогда англичанами управлять не будут". На что я им ответил: "Всё. С этой минуты я больше с вами не работаю"".
Ржевский ушел из компании в знак солидарности с товарищем.
Возвращение в Россию в 2009 году оказалось для Скобелева непростым. Но он вовсе не скис: "Это был вызов, в каком-то смысле даже хорошо, что все так резко обострилось и нужно было заново начать день и ночь работать, для того чтобы добиться результатов". Пришлось заново разрабатывать технологическую платформу, так как права на интеллектуальную собственность на прежние разработки остались за Magenta, но "мы же были первыми, - говорит ученый, - кто восемь лет проработал на одной теме по мультиагентным технологиям, и в голове был рой научных идей на 25 лет вперед".
http://expert.ru/russian_reporter/2016/14/risunki-v-kotoryih/
http://www.olap.ru/home.asp?artId=2590
«Эксперт», № 48, 24 ноября 2014
--- Оборонная промышленность Россия не только воссоздала технологию ремонта украинских газотурбинных двигателей, которыми оснащается большинство надводных кораблей нашего ВМФ, но и силами частной промышленной группы «Новик» организовала полный цикл их обслуживания на отечественной производственной площадке в Самаре, на заводе «Металлист-Самара». Алексей Лященко, руководитель «Новика» рассказывает:
- В Самаре много машиностроительных предприятий пусть и не совсем близкого профиля, но около того... Таким образом, кадровый вопрос у нас в принципе решался. Но ключевую роль, конечно, сыграло то, что мы приняли на работу ряд бывших сотрудников «»Зори-Машпроект»... Взяли тех, кто умеет делать то, что нам нужно...
Мы инвестировали более сотни миллионов рублей наших собственных средств. Понимая сложную экономическую обстановку, мы не стали настаивать на том, чтобы государство компенсировало нам эти расходы ...
- если даже Вы привлечете кредит под 14%, что маловероятно, то все равно при такой ставке проект не окупится...
--- А что у нас быстро окупаемо ? Я вот сделал производство по ремонту газовых турбин в Самаре, так оно тоже нескоро окупится. Мы четко отдаем себе отчет в том, что инвестированные в него средства в ближайшее время не вернутся.
- ... а зачем тогда вкладываете ?
--- Ну как зачем ? Потому что корабли должны ходить. Знаете, некоторые люди играют в казино, другие, - едят на дискотеках таблетки. У меня свои предпочтения, я вот корабли люблю...
Недавно вернувшийся в боевой строй фрегат «Ярослав Мудрый» (который на днях пытались спровоцировать амеры в Средиземном море), - дело рук «Новика».
http://expert.ru/expert/2016/13/vsyo-na-svoej-baze/
--- Компания Parallels является мировым лидером в сфере разработки программного обеспечения виртуализации и автоматизации для частных лиц, предприятий и провайдеров услуг. Зародившись в 1999 году как небольшая софтверная компания, она прошла путь до корпорации со штатом более 800 сотрудников, владеющей более чем пятью десятками патентов. Parallels поддерживает более 1 миллиона серверов и ПК, обслуживает более 10 миллионов пользователей в 125 странах. Сергей Белоусов, - председатель правления и главный архитектор.
Мировым лидером является и еще одна основанная Белоусовым компания, - Acronis, - но только в области программного обеспечения для хранения и восстановления данных.
Российский квантовый центр (РКЦ). В консультационный и попечительский советы РКЦ входят два Нобелевских лауреата. Сергей Белоусов, - председатель попечительского совета.
Quantum Wave Fund (Qwave) - Международный венчурный фонд. Сергей Белоусов — старший партнер.
--- Qwave интересуется проектами, в которых учитывается влияние единичных квантовых эффектов. За последние двадцать лет ученые научились их наблюдать. Один электрон, одно квантовое состояние — с помощью этого можно сделать принципиально лучшие технологии для коммуникаций, вычислений и измерений. Построенные на этом устройства будут на порядки быстрее, энергоэффективнее, меньше и точнее.
Например, квантовые сенсоры позволяют создавать миниатюрные и очень точные измерительные приборы. Один из наших проектов связан с модернизацией рамановского спектрометра, который сможет обнаружить наличие одной-единственной молекулы определенного вещества. Потенциальное применение — обнаружение различных веществ, например наркотиков или взрывчатки, в грузе и даже определение, перевозились ли они когда-нибудь в данной сумке... Конечно, нас интересуют темы, связанные с квантовыми вычислениями: квантовые компьютеры и симуляторы. Они позволят рассчитать характеристики принципиально новых веществ: например, Владимир Шалаев разрабатывает порошок, который делает невидимым объект, вокруг которого он распылен. Если появятся, нас заинтересуют и проекты создания высокотемпературных сверхпроводников, работающих при комнатной температуре (Сергей Белоусов).
https://ru.wikipedia.org/wiki/Белоусов,_Сергей_Михайлович
«Эксперт», № 3, 2013
http://www.eco-pravda.ru/page.php?id=5270
--- Владислав Мартынов: «Мы опередили отрасль на 5–7 лет...»
– На первой же встрече перед началом презентации представители фонда, за которым стояли основатели BlackBerry, попросили запустить видео на YotaPhone 1. Пока я делал 20-минутную презентацию, смартфон показывал ролик с YouTube по LTE. Они внимательно наблюдали. YotaPhone не грелся, второй экран продолжал стабильно работать, картинка не расплывалась. Это вызвало изумление: «Как вам это удалось? Это невероятно!»...
– Второй экран выпускает отдельная компания E Ink, и нам нужно было встроить его в смартфон. Мне повезло: купив Nokia, Microsoft закрыл крупнейший центр разработки Nokia в городе Улу, что почти у самого Полярного круга, и не одна тысяча специалистов осталась без работы. Десятерых из них я нанял. Они и занялись интеграцией второго экрана.
- Сильное впечатление на инвесторов произвел именно прототип YotaPhone 2. Его модель была не только намного лучше первой, многих просто завораживал второй экран, на котором проступали надписи, словно на темном камне.
За последние годы проект YotaPhone несколько раз оказывался на грани жизни и смерти, но его инициаторам каждый раз удавалось находить силы и ресурсы для продолжения работы.
https://cont.ws/post/256259
--- Смычка ученых мозгов и разумного тарана
Кого обычно мы себе представляем, когда речь идет о системах отопления и о связанных с ними трубах, о котельных, снабжающих наши дома теплом и горячей водой ? – Дядю Петю, или дядю Васю в замасленной спецовке, с матюками ковыряющихся в забитых накипью трубах.
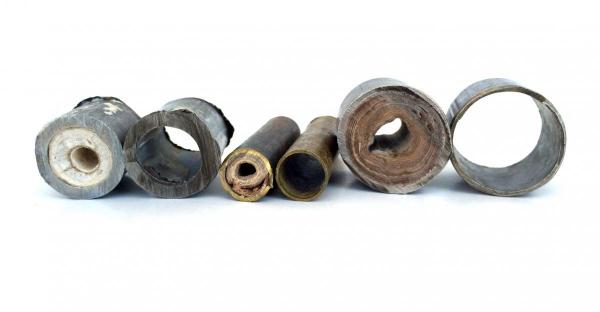
Разве можно подумать, что с грязью, накипью, - и даже с бактериями, жрущими трубные бяки – может иметь дело «финтифлюшка» с фотографии:
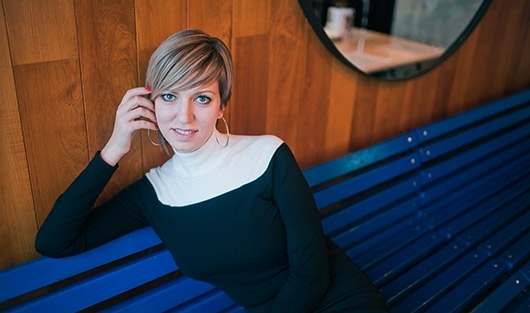
Тем не менее, при личной встрече с «эффектной блондинкой» журналист «Форбс» с изумлением наблюдает, как ловко она вытаскивает из элегантной сумочки... кусок чугунной трубы. С одной стороны которой виден сантиметровый слой накипи внутри, с другой — абсолютно чистая поверхность.
Так генеральный директор ООО «Наносерв» Елена Левина демонстрирует работу компании. «Наносерв» чистит системы отопления зданий, трубопроводы, выпарные установки и промышленные котлы от солей и накипи специальным биореагентом. Сложно? - Елене, финансисту по образованию, поначалу казалось нереальным разобраться в этом. Зато теперь она говорит на одном языке и с микробиологом в лаборатории, и со слесарем в котельной. Этот бизнес принес фирме в 2013 году 3 млн рублей выручки и 1 млн рублей прибыли. Пакет контрактов на 2014 год — составил уже 200 млн рублей. Среди заказчиков есть сахарные заводы, теплогенерирующие предприятия «Лукойла» и «Роснефти».
Еще удивительнее то, какие люди окружают «эффектную блондинку» в компании. Это 7 профессоров, 5 кандидатов наук, 4 доктора наук, - такой коллектив научной базы ООО "НаноСерв", г.Краснодар, получил 13 мая 2013 года Государственный сертификат соответствия № 0893908, основанный на Патенте на изобретение РФ №2213922, авторами которого являются Звенигородский Виктор Петрович, - ему за 70, и Богомолов Виктор Николаевич, - ему за 60. Их нынешнему начальнику, Елене Левиной, чуть за 30.
- ... Краснодарская компания «НаноCерв» (торговая марка «Бонака») стала победителем Startup Tour 2015, организованного «Сколково» в 2015 году, компания была принята в резиденты инновационного центра.
Сейчас у компании внушительный портфель заказов. Она занималась очисткой труб и котлов для крупной теплогенерирующей компании перед Олимпиадой в Сочи, кроме того, компания обслуживает школы, детские сады, отделения полиции, а также управляющие компании и ТСЖ. В настоящее время у компании более 850 клиентов, 30 контрактов и тестовых внедрений в крупных компаниях (РЖД, «Алроса», «Башнефть»)».
- Благодаря статусу резидента [Сколково], мы участвуем во многих крупных выставках, посещаем конференции и имеем возможность донести до нужной нам аудитории информацию о нашей технологии. Один из последних наших проектов — очистка объектов “РАО Энергетические системы Востока” на Алдане. Этим достижением мы очень гордимся. Так, мы взяли курс на восток и активно расширяем дилерскую сеть» (Елена Левина).
http://www.forbes.ru/svoi-biznes/istorii-uspekha/251721-burya-i-nakip-kak-byvshii-top-menedzher-postroila-biznes-na-chist
http://www.teplosputnik.ru/патенты-сертификаты
http://biochistka.com/news/bakterii-protiv-nakipi-i-gryazi.html
http://expert.ru/expert/2014/47/bakterii-protiv-nakipi-i-gryazi/
http://expertsouth.ru/novosti/krasnodarskii-pobeditel-startup-tour-201.html
--- По сложности изготовления гидромолот сравнивают с двигателем внутреннего сгорания и с артиллерийским орудием. С той лишь разницей, что в двигателе поршень не испытывает нагрузку от удара, высвобождающего тысячи джоулей энергии. А орудийный ствол выпускает пустотелый снаряд, тогда как гидромолот работает с цельнометаллической болванкой, которую нужно не просто выпустить со скоростью 11 метров в секунду, но и поймать потом в финальной точке, и так, - свыше тысячи раз в минуту.
Высокая температура, трение, ударная нагрузка на материал, то есть, очень большая концентрация напряжения в малом объеме пространства обусловили высочайшие требования к стали и сплавам, используемым при производстве , а также к самой конструкции, микронные допуски элементов которой должны учитывать расширение при нагревании.
До начала 1990-х в мире было четыре центра разработки и производства , - Франция, Германия, Финляндия и СССР. Потом осталось три.
Мало кто ждал, что наша страна так быстро вернется в число лидеров. «Технопарк Импульс», компания основанная в 1995 году выпускниками Московского автодорожного института, уже в 2000-е двинется к амбициозной цели: к созданию российского гидромолота, превосходящего лучшие зарубежные образцы. Серийный выпуск таких молотов начался в 2010 году, после семи лет испытаний и доработок.
http://www.it-weekly.ru/market/business/76223.html
--- Четыре подъезда снизу доверху в итальянской керамической плитке. Пол из керамгранита. Перила из нержавейки. Бесшумные болгарские лифты. Облицовка фасада – особо стойкой разноцветной штукатуркой. Пандусы у подъездов, тротуары из брусчатки. Столь богато обустроенной многоэтажки, как дом № 7/2 по Верхнепечёрской, в Нижнем Новгороде ещё не видели. Оказалось, содержать дом таким образом можно, взимая с жителей плату по муниципальному тарифу. Обычную панельную девятиэтажку с 20-летним «пробегом» привёл в нынешнее состояние Михаил Швыганов, который возглавил правление ТСЖ в 2003 году.
Девятнадцать лет назад, когда Швыганов переехал в этот дом, тот не блистал ухоженностью. На текущий ремонт и содержание здания денег не хватало. Их требовалось найти. Но где? Повысить тариф для собственников? Михаил Иванович нашёл другой способ – сэкономить.
Но сэкономить по умному. Хотя подход Швыганова к ремонту, например, кому-то может показаться шикованием. Однако, по его расчётам, «экономичный» ремонт оказывается совсем не экономичным:
«Через полгода побелка стёрта, стены исписаны – впору заново ремонтировать. Я всегда использую новые и лучшие материалы, способные прослужить по максимуму. Мы не так богаты, чтобы делать дешёвый ремонт. Например, подъезды. Стены отделаны керамической плиткой, пол из керамгранита, подвесные потолки из гипсокартона. Эстетика – раз. Удобство в уборке – два. Долговечность – три. А этому ремонту уже 10 лет! Если бы я экономил в традиционном представлении, я бы за это время был вынужден сделать уже несколько ремонтов»...
Если человек талантлив, так он талантлив во всем, - в последнюю пятилетку Михаил Швыганов (которому сейчас 55 лет) поставил на поток производство наследников: Денису 4 года, Андрею 2 года и Артёму шесть месяцев.
http://pikabu.ru/story/glava_tszh_sdelal_iz_panelnoy_devyatiyetazhki_dvorets_po_munitsipalnomu_tarifu_4084455
http://nn-patriot.ru/?id=7845
--- Одними из самых современных предприятий Рязанской области являются заводы корпорации ТехноНИКОЛЬ, выпускающие стройматериалы. В компании исповедуют философию японского автогиганта, помогают рабочим приобретать жилье и строят спорткомплексы для горожан. Кровли ТехноНИКОЛЬ, рулонные, полимерные, из гибкой черепицей покупают в 70 странах, а сама корпорация потихоньку скупает в Европе заводы, у которых ранее перенимала технологии, и российские ее предприятия работают на самом современном оборудовании. В Рязани компания представлена семью заводами, самый новый открылся в сентябре 2015 года. Здесь выпускают черепицу "Шинглас" ( 60 лет гарантии ) - из-за нее, в том числе, город прослыл "кровельной столицей России" - а также гидро-, тепло- и шумоизоляцию.
Делать все это может благодаря своей эффективной работе. Оборот корпорация - более 60 млрд рублей в год, а производительность труда на одного сотрудника составляет 14 млн рублей. То есть, работает «Технониколь» с показателями мирового уровня, причем компания вышла на этот уровень уже после кризиса 2008 года...
Вспомним, как недавно Греф восторгался фирмой «Алкоа», которая сумела сократить производственный процесс, - по выплавке и изготовлению алюминиевого проката - с 20 дней до 20 часов (то есть, в 24 раза). Компания же из «страны-дауншифтера» сократила время переналадки технологической линии при переходе с одного вида продукции на другой в ... 1800 раз: с 6 часов до 12 секунд.
Творческий подход к работе в ТехноНИКОЛЬ развит настолько, что удается улучшить немецкие технологические линии. Скажем, в дозаторах сырья производитель установил задвижки, пазы которых спустя какое-то время неизбежно забиваются гранулами полистирола и узел выходит из строя. Рязанские Левши поменяли задвижки на поворотные заслонки - как в карбюраторе, - и проблема исчезла. Авторы идеи получили премию, а опыт немедленно распространили на все заводы компании.
Что такое PIR — полиуретановый теплоизоляционный материал нового поколения, журналистам, собравшимся 24 мая 2016 года на церемонию торжественного открытия завода «Лоджикпруф ПИР» в Рязани, показали не только на конвейере, но и на «кровельном шоу», устроенном прямо в цехе, под грохот работающей линии. Наглядно продемонстрировали, что процесс утепления крыши или фасада с помощью PIR-плит протекает проще и быстрее, чем при работе с традиционным материалом, скажем с минеральной ватой. В случае с которой пришлось бы предварительно установить трапы для хождения по крыше, а также обеспечить рабочего респиратором и перчатками для защиты от пыли. Здесь же ничего этого не нужно: PIR не «вытаптывается» из-за своей повышенной жесткости и экологически безопасен...
Будучи крупнейшим производителем кровельных, гидроизоляционных и теплоизоляционных материалов в России, СНГ и Европе, «Технониколь» и этот свой проект осуществила с размахом. Инвестиции в «Лоджикпруф ПИР» составили 1,7 млрд рублей, и это лишь первая очередь: через два года ожидается вторая. Итоговая проектная мощность линии — 2 млн кубометров PIR-плит — в полтора-два раза превосходит мощность аналогичных европейских предприятий. Правда, в первые годы мощность эта будет использована где-то на 10%. – С чего бы это такая расточительность ? Об этом, среди прочего, поговорим в заключительной части статьи...
http://rg.ru/2015/12/02/reg-cfo/tecnonikol.html
http://www.tn.ru/img_out/articles/upload3j81vhez8fb.pdf
http://rg.ru/2015/12/02/reg-cfo/tecnonikol.html
http://expert.ru/expert/2016/22/stroitelej-zovut-na-pir/
http://expert.ru/expert/2016/22/stroitelej-zovut-na-pir/
--- Что объединяет многие из упомянутых историй ? – Системный, инженерный подход к развитию своего дела со стороны основателей компаний. И, как это некоторых ни удивит, - уверенность в завтрашнем дне. Причем, уверенность не розовоочковая, а подкрепленная глубоким анализом и планомерными усилиями по созданию прочных предпосылок для успешности компаний в обозримой перспективе. При самых разных условиях внешней среды. Уверенность, подкрепленная разумным, как у муравьев и пчел, коллективным трудолюбием.
Терпи. Зри в корень. Не жмоться. Бди. Переумни.
Нетерпеливые Камрады, - пролетев текст с историями успеха по диагонали - обязательно возмутятся, что таких успешных компаний у нас мало, что срочно надо «Быстрее, выше и дальше» (про троллей я и не говорю, - ясно, что закричат и завопят о «сурковской пропаганде»).
И знаете, - ничего удивительного в этом нет, так как подобным настроениям бывают подвержены даже люди терпеливые. Хотя при этом они сами утверждают (на основании своего успешного опыта), что двигаться к настоящему, стабильному успеху, надо не как заяц, а как черепаха.
Возьмем высказывание Сергея Колесникова, президента корпорации «Технониколь», из интервью журналу «Эксперт»:
--- Таких компаний [как «Технониколь»] должно быть тысячи. То, что у нас не тысячи, а единицы компаний частного сектора, имеющих такой масштаб, говорит о том, что у нас что-то не так. Если бы у нас [в стране] была стабильная финансовая среда, низкие налоги, стабильный спрос, количество крупных компаний быстро бы росло. А когда у нас все постоянно меняется, появляющиеся ростки не развиваются...
Все, вроде бы, верно. Но в этом же интервью, Колесников сам высвечивает слабое место в логике своего высказывания.
- Корреспондент: ... с вашей позиции, совсем-совсем топ-менеджера, что такое эффективность? Года два назад мы с вами говорили об этом, и вы сказали, что главная задача руководства — обеспечить стабильность. Значит ли это, что стабильность равна эффективности?
- Колесников: Если вы работаете в стабильных условиях, то можете оптимизировать нестабильные потоки. Сложно заниматься улучшениями, если... ваш поток постоянно прерывается, если вы постоянно занимаетесь авралами, то вы из этих авралов всю жизнь не вылезете.
Здесь посмотрим, сколько же сама корпорация «Технониколь» шла к обретению необходимой для успешного развития стабильности (shed):
- Корреспондент: А если соотнести изменения со временем? Достичь результатов от перемен хочется очень быстро, а получается медленно. Вы начали внедрять системно эффективность в 2006–2007 году. В какой момент у вас возникла достаточная по мощности команда, чтобы все реализовывать?
- Колесников: Я начал в 2008 году. А стал замечать, что команда начала все делать очень самостоятельно, в 2012-м. Четыре года ушло на раскачку системы. А с 2012-го по 2015-й она движется в заданном направлении. То есть в принципе средний цикл изменений занимает от трех до пяти лет. Но это в компании с четырьмя с половиной тысячами сотрудников и сорока предприятиями ( понятно, что в такой большой стране, как Россия – все гораздо сложнее и дольше, чем в любой самой крупной компании - shed ) Конечно, если компания маленькая — один завод, все можно сделать в течение полугода-года.
И еще про время, необходимое для оптимизации работы с клиентами:
- Корреспондент: В рамках создания системы эффективного производства вы уделили огромное внимание клиентскому сервису.
- Колесников: Мы реализовали стандартизацию обслуживания клиентов внутри компании по всем бизнес-единицам, по всем заводам. Потом сделали унификацию и централизацию. Это очень сложная тема, которая заняла семь лет... Кажется, что это просто. Но все надо прописать: кто, что и когда должен делать, а потом заставить следовать, чтобы никто не бегал друг к другу в кабинет, а все работали, как это работает в симфоническом оркестре — все знают свои ноты, и все работают по указанию дирижера... Прописание этих правил заняло очень много времени. Мы прописывали, смотрели, учились, обучали, передавали опыт на другие предприятия, двигались как черепаха, внедряя те или иные изменения. Делали пилотные проекты, потом эту практику расширяли, потом снова пилот, снова расширяли. Двигались так, что клиенты не видели падения сервиса. Пожалуй, это был самый длинный по времени проект.
«Эксперт», № 3, 2016
http://www.tn.ru/img_out/articles/upload3j81vhez8fb.pdf
Применим эти рассуждения Колесникова не к компании, - даже большой - а к огромной России. Умные люди в России разных эпох недаром подчеркивали, как нужен стране хоть небольшой, - лет на 20 – период стабильности. Но нам же его никогда не давали.
И тем не менее...
ЗЫ. Статья получается длинноватая, поэтому приходится делить ее на части, - вторая вскоре последует.
ЗЗЫ. В обозримом будущем должны также созреть в этой серии («Американские горки Гегемона») следующие отдельные статьи (названия условные): Наш Булат и наши Воины (ссылки будут вставлены); Китай: они думали – ящерица, а вырос – Дракон (ссылки будут вставлены); Злато «Повелителей Вселенной» (ссылки будут вставлены); Ядовитые Стрелы/Семена Баобаба «Повелителей Вселенной» (ссылки будут вставлены)...
Оценили 24 человека
27 кармы