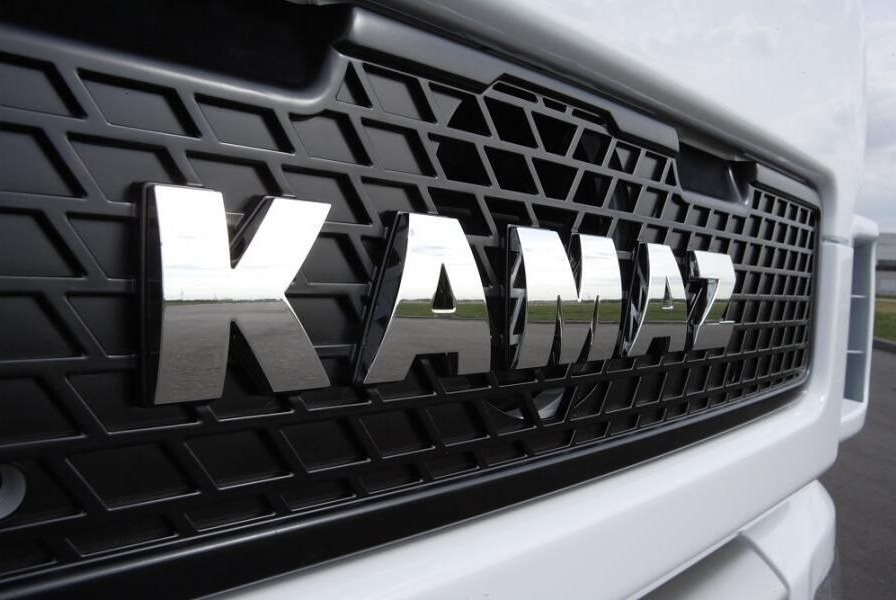
В НТЦ «КАМАЗа» собраны первые образцы среднетоннажных тягачей КАМАЗ-53251. Новые модели продолжат модельный ряд поколения К4.

Разработки представляют собой шасси, на которые будут устанавливаться надстройки для сфер ритейла и ЖКХ. Новые шасси облегчены по сравнению с предшественниками на 200 килограммов. Снаряженная масса образца, предназначенного для коммунальных услуг, равна 6,25 т, технически допустимая масса - 19 тонн. Грузовик для ритейла получил полную массу 18 т, максимальную с учетом прицепа - 28 тонн. Сердцем для обеих машин послужит дизельный мотор Cummins ISB6.7E5 310 класса «Евро-5». Образцы оснащены коробкой передач на 9 ступеней. Модель для торговли укомплектована дополнительным спальным местом.

По словам заместителя главного конструктора по автомобилям Игоря Валеева, при разработке новых образцов стояла задача снизить снаряженную массу автомобилей без сокращения других характеристик, и эта цель достигнута. Впереди новые образцы ждут испытания, а тем временем уже разрабатывается документации для грузовика КАМАЗ-53252 с двигателем «Евро-6».

ПАО «Тутаевский моторный завод», дочернее предприятие «КАМАЗа» в Ярославской области, впервые получило сертификат о происхождении товара формы СТ-1 на промышленные модификации двигателей.

Сертификат, подтверждающий страну происхождения товара, позволяет потребителям двигателей ПАО «ТМЗ» получить таможенные льготы при вывозе их из России на территорию стран СНГ, а также субсидии из федерального бюджета на компенсацию части затрат, связанных с выпуском высокопроизводительной самоходной и прицепной техники.
«Экспертизу проводит Торгово-промышленная палата. Она анализирует документы, указывающие на происхождение всех комплектующих двигателя, и дает экспертное заключение о том, что двигатель действительно российского происхождения. Доля стоимости импортных комплектующих в товарах российского происхождения не может превышать 50 %. Согласно акту экспертизы Ярославской ТПП, доля стоимости импортных комплектующих в двигателях ТМЗ промышленных модификаций 8525.10, 8141.10-05, 8435.10 составляет 2,5 %. Акт экспертизы и сертификат действительны в течение 12 месяцев, поэтому в следующем году всю процедуру предстоит пройти заново», – пояснила начальник бюро управления качеством, стандартизации и сертификации ПАО «ТМЗ» Венера Метерина.
Экспертизу тракторных модификаций двигателя ПАО «ТМЗ» впервые прошло в 2020 году. В 2021 году начался серийный выпуск двигателей с электронной системой управления. На них будет оформляться отдельное экспертное заключение.
Как поясняют специалисты Тутаевского моторного завода, этот документ важен для основного потребителя тракторных моторов – Петербургского тракторного завода. С начала года введена балльная система для локализации сельскохозяйственных тракторов и дорожной техники – оценивается степень локализации каждого вида выпускаемой техники, а не в целом производитель. За технологические операции и компоненты двигателя, произведенные на территории Российской Федерации, в акте экспертизы указываются баллы. Для получения господдержки и участия в госзакупках производителю техники нужно набрать определенное количество баллов. Так государство стимулирует производство российской техники. По данным Минпромторга РФ, в 2019 году доля российской техники на отечественном рынке превысила 54 %, в 2020 году – 58 %. К 2030 году планируется достичь показателя 80 % на внутреннем рынке техники.
В Белгороде накануне вышел на линию первый камазовский электробус. В течение трех месяцев в тестовом режиме он будет курсировать между остановками «Аэропорт» и «Технологический университет» – по одному из городских маршрутов троллейбуса. Пантограф для быстрой зарядки инновационной техники «КАМАЗа» размещен на территории базы Единой транспортной компании, расположенной в поселке Северный.

Одним из первых пассажиров, проехавших на инновационном общественном транспорте, стал глава Белгородской области Вячеслав Гладков. Губернатор отметил экологичность электробуса, который не дает выбросов в атмосферу. Кроме того, Гладков обратил внимание на уровень вибрации и шума в салоне: они значительно ниже, чем в рядовом автобусе.
Директор по пассажирскому транспорту «КАМАЗа» Самат Саттаров напомнил, что в октябре этого года завершилось трехмесячное тестирование электробуса в столице Татарстана. За это время им воспользовалось порядка 40 тысяч пассажиров. Также этот инновационный транспорт собрал множество положительных откликов жителей Казани. К слову, казанский «Метроэлектротранс» выяснил, что электробус челнинского автопроизводителя экономичнее троллейбуса на 57,5 тыс. рублей в месяц.
Реинжиниринг производства на литейном заводе идет полным ходом: две из трех поступивших новых печей Otto Junker уже работают, третья ждет своего часа. А к 2025 году, по проекту, все старые печи заменятся новыми.
Otto Junker – индукционная тигельная печь выдержки емкостью 65 тонн. Рабочий полезный объем составляет 50 тонн – именно столько продукции способна выдавать печь. А оставшиеся 15 тонн приходятся на жидкий металл, который постоянно поддерживается в рабочем состоянии, ведь печь никогда не отключается полностью. Срок службы без перебивки футеровки составляет два года.
Первую из новинок запустили 20 августа, вторую – 10 сентября этого года. И на ЛЗ осваивают работу на них: обучают этому в том числе и специалисты фирмы Otto Junker. Начинали с двух плавок в сутки, сейчас делают уже четыре на новых печах. По проектной мощности они не уступают старым печам (те должны выдавать 33 тонны металла в час), но пока такого результата достичь не удалось – опытная эксплуатация только началась.
И пусть прошло совсем немного времени с момента запуска печей, но, по словам начальника производства чугунного литья Дмитрия Применко, уже можно отметить позитивные перемены в работе.
– Начнем с того, что новые печи работают намного тише. Вспомните, как громко шумели старые.
И действительно – в цеху достаточно комфортно разговаривать, собеседника слышно (прим. авт.).
– Еще отмечу, что от этих печей в принципе не исходит излучение – вся рабочая часть закрыта, металл не видно. Открывается печь два раза в месяц для скачивания шлака, – рассказал Применко.
Для литейщиков плюсов от новинок предостаточно: ведь со старых печей шлак качается ежесменно, по нескольку раз в день (доходит до 10-15 раз). Otto Junker требуют меньших трудозатрат, что очень облегчает жизнь плавильщиков.
Да и в плане качества, считает Применко, новые печи не подкачали.
– Отливки из этих печей намного лучше: это видно по качеству поверхности и металла – он заметно чище. С ковшей скачивается гораздо меньше шлака. Для примера: у старых печей тару мы меняем три-четыре раза в сутки, а с новыми хватает одного раза. Также сразу после запуска печей Otto Junker мы отмечаем уменьшение брака – примерно на 2,5-3%.
Первые результаты и наблюдения выглядят многообещающими – литейщики задать жару готовы!
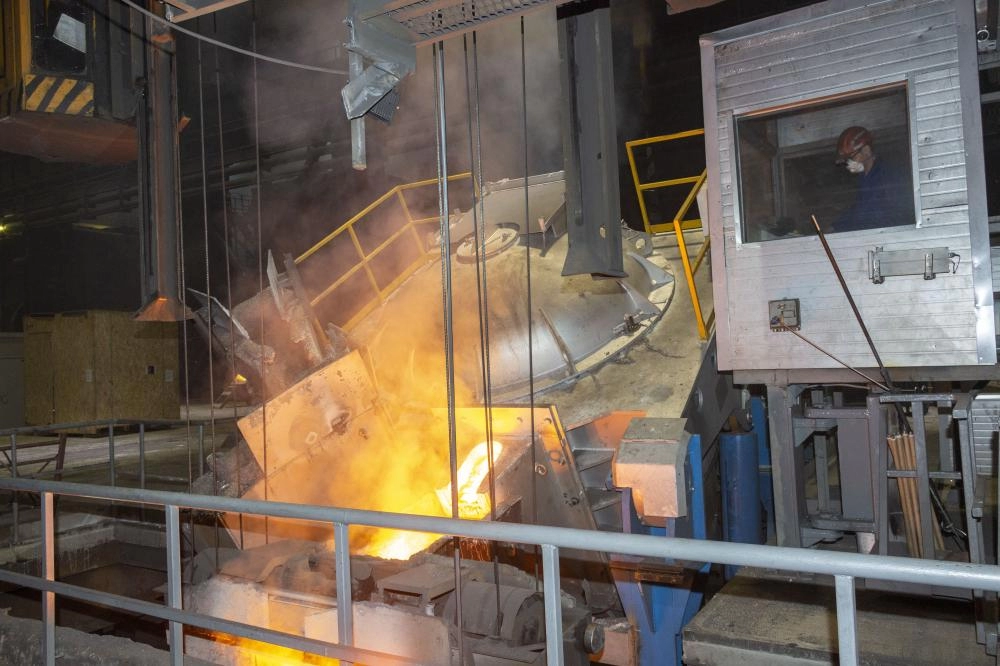
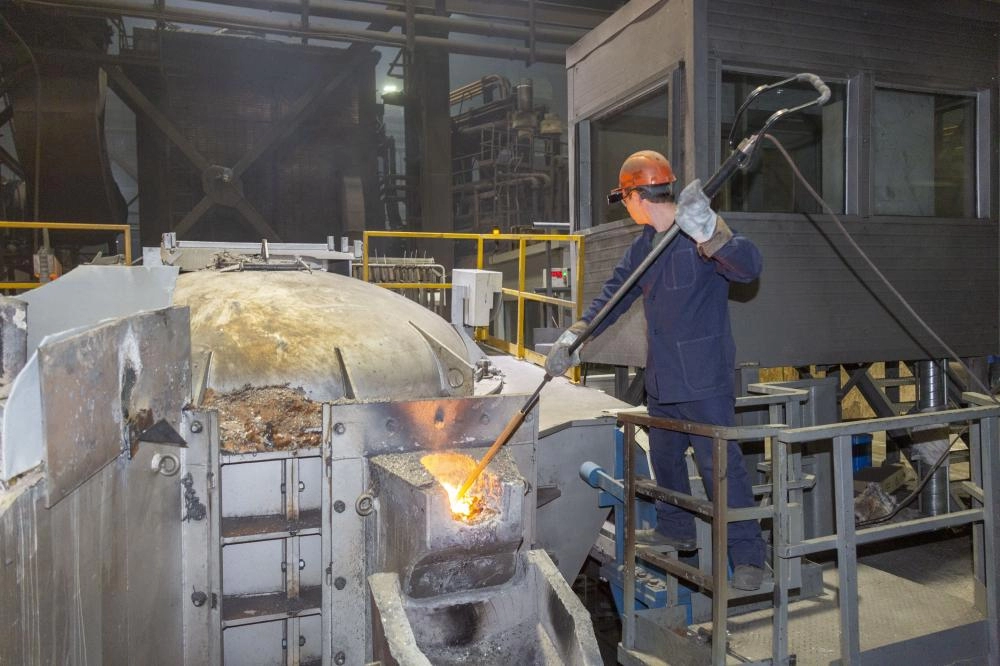
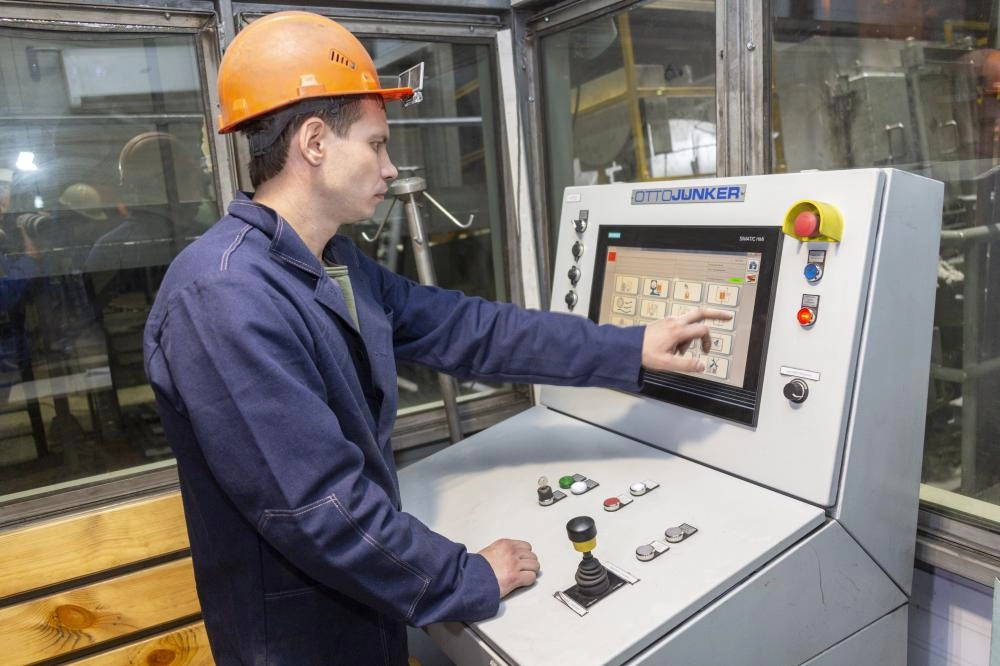
Одну из двух автоматических линий, расположенных на кузнечном заводе, а именн линию штамповки коленчатого вала 031, ждет комплексная модернизация. Ее цель – реконструкция кузнечного производства тяжелых поковок в высокотехнологичное конкурентоспособное производство. Старт инвестиционному проекту будет дан в начале 2022 года.
Автоматическая линия по выпуску коленчатого вала на базе штамповочного пресса EUMUCO KSP-1200 усилием 12 тыс. тонн была и остается своеобразной визитной карточкой кузнечного завода. В конце 70-х ковочное оборудование немецкой фирмы EUMUCO было одним из самых современных, и для камазовской кузницы его установка стала поистине революционным событием, ведь изначально по проекту КПК-3 планировалось оснастить шестью молотовыми линиями. Уже 44 года без единого капитального ремонта и модернизации линия 031 трудится и выдает продукцию.
Конечно, как и любой механизм, это оборудование уже достигло момента, когда требуется его капитальный ремонт и модернизация. В 2019 году эксперты из Германии провели технический аудит линии 031. Это была объективная оценка профессионалов: фирма «СМС Груп ГмбХ» занимается ремонтом, модернизацией и обслуживанием линий EUMUCO по всему миру. Тогда было озвучено, что процесс модернизации начинать необходимо: физически и морально линия изношена. Ее работоспособность – примерно 30% в сравнении с аналогичными линиями конкурентов. Тогда же прозвучало, что немецкой стороной будет предложено несколько концептуальных решений, но неизменно то, что после модернизации линия обеспечит соответствие современным требованиям производительности, автоматизации и цифровизации процесса.
Предложенные немецкой стороной концепции обсуждались со специалистами кузнечного завода, что-то совместно дорабатывалось. И вот при активной творческой переработке материалов, целей и задач под руководством нового директора КЗ Александра Чеха родился проект по комплексной модернизации линии 031, который в сентябре этого года был вынесен на рассмотрение заседания Управляющего Совета ПАО «КАМАЗ» и принят к реализации.
– К концу 2023 года мы должны получить высокотехнологичную автоматическую линию. Например, модернизация позволит нам восстановить производительность линии до ее паспортных данных – 52 штуки в час. Сегодня же фактическая производительность от 19 до 27 шт./час, – комментирует руководитель проекта «Модернизация кузнечного завода» – II этап», главный инженер КЗ Гамир Мухаметзянов. – Кроме того, стабилизируется качество поковок, снизится себестоимость продукции, а это для нашего завода – увеличение объема выпуска коленвалов для нового модельного ряда автомобилей КАМАЗ и заказы по продукции диверсификации.

Сегодня уже проработан регламент проекта. Ведется разработка его плана, актуализируется бюджет, идут переговоры с потенциальным исполнителем работ, в которых будет задействован и производственный персонал завода. Принимая непосредственное участие в демонтаже, монтаже нового оборудования, в пусконаладочных работах, кузнецы будут обретать знания, понимание того, что и как устроено в модернизированной линии. Ведь она станет высокотехнологичной, а новые современные технологии потребуют определенных компетенций.
– Нас ожидает колоссальная работа. Запланировано восстановление, замена основных исполнительных механизмов, систем на всех ковочных машинах линии, – рассказывает заместитель главного инженера КЗ по реинжинирингу Евгений Архипов. – Например, все локальные системы управления будут полностью заменены и интегрированы в новую общую систему управления всей ковочной линии. Кардинально изменится и технология нагрева заготовок: выработавший ресурс комплекс электромашинных преобразователей частоты и индукционный нагреватель будут заменены на современную транзисторную высокочастотную установку индукционного нагрева с индивидуальным источником питания. Эта прогрессивная технология позволит процесс нагрева заготовок под штамповку сделать стабильным и высокопроизводительным, а также снизит потребление электроэнергии в целом по линии на 20%. А еще предстоит модернизация всей транспортной системы линии и внедрение промышленных роботов для перемещения полуфабриката по операциям. Все это вкупе позволит оптимизировать себестоимость выпускаемой продукции, повысит количественные и качественные показатели.
Еще один плюс предстоящей модернизации – ее экологический аспект. По предварительным расчетам, после реализации проекта образование отходов 1 класса опасности на линии должно сократиться на 100%, а это сокращение на 15% в целом по заводу. Будут снижены наполовину и выбросы продуктов сгорания технологической смазки (сажи). Это станет возможным с внедрением роботизированной системы со специализированной распыляющей головкой. Все вышеперечисленное, а еще запланированная санация той части КПК-3, где расположена линия 031, кардинально улучшит условия труда производственного персонала.
Непосредственная подготовка на кузнечном заводе в рамках проекта начнется в начале 2022 года. А модернизированная автоматическая линия штамповки коленвала в режиме пусконаладки должна заработать к концу 2023-го.

Камазовская команда 22 октября отправилась на VIII Национальный чемпионат сквозных рабочих профессий высокотехнологичных отраслей промышленности WorldSkills Hi-Tech-2021.
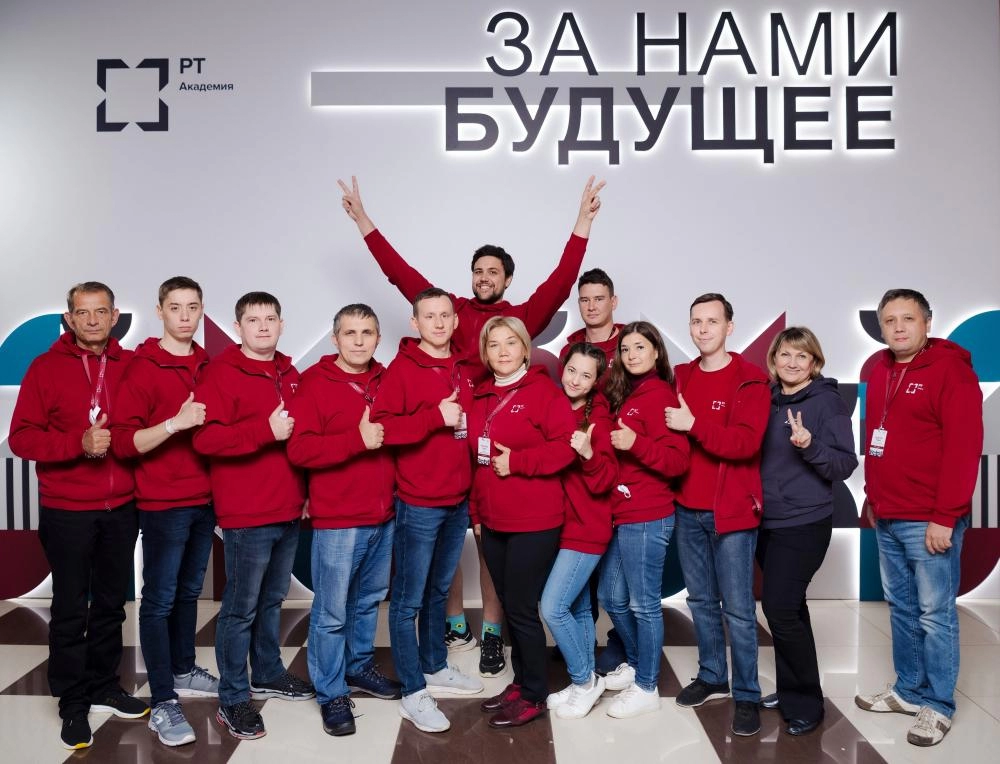
Наши специалисты в составе команды Госкорпорации «Ростех» будут бороться за победу в четырёх компетенциях: «Прототипирование», «Рекрутмент», «Литье», «Развитие производственной системы». Место в сборной каждый из них отвоевал, одержав победу в отборочном туре.
Соревнования пройдут с 25 по 29 октября в МВЦ «Екатеринбург-Экспо». В этом году в чемпионате WorldSkills Hi-Tech примут участие порядка 500 конкурсантов – представителей отечественных индустриальных компаний. Свои навыки они продемонстрируют в 39 профессиональных компетенциях.

Оценили 10 человек
25 кармы