Здравствуйте, читатели мои!
В преддверии дня трудящегося народа, хочу поговорить о трудовых достижениях в области камнетесания.
Поскольку тут некоторые обладатели альтернативно-обустроенных мозгов пытаются внушить мысль о том, что колонны Казанского и Исаакиевского соборов, Александрийский столп и другие гранитные "поделки" в архитектуре Петербурга никак не могли быть изготовлены вручную, то предлагаю познакомиться с историей развития гранитной индустрии в Новой Англии XIX века. Предупреждаю, что из-за невозможности долго просиживать за компьютером, откладываю в сторону тонкости и причёсывание плодов технического перевода гугла. Но, думаю, что те, кого информация заинтересует, могут взять сей труд на себя.
Книга Arthur Wellington Brayley называется "History of the Granite Industry of New England" 1913 г.
***
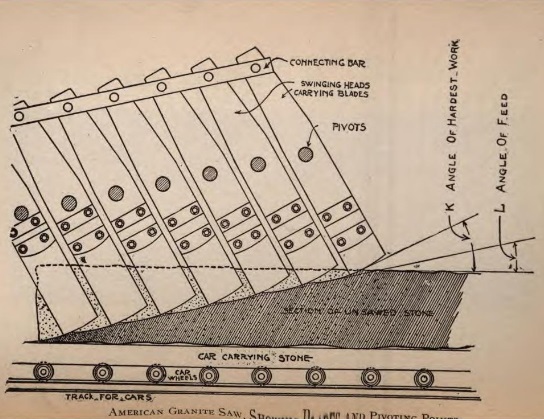
Полировка гранита машинами была впервые введена в эту область в Куинси в 1869 году. Некоторые попытки были сделаны ранее, но оборудование было грубоватым и мало успеха было получено. В 1869 году трое шотландцев, Гордон Маккензи, Джон Уэстленд и Джордж С. Паттерсон, каменотесы, расположенные в Куинси, создали совместное товарищество под фирменным названием Маккензи, Уэстленд и Паттерсон. Они наняли землю в канале Куинси и построили два прямых сарая с расположенной между ними подвесной дорожкой. Один сарай был использован для резки, а другой для полировки. Завод состоял из 30-ти двигателей на лошадиной и паровой тяге, передвижной каретки, двух вертикальных и двух маятников.
Г-н Уэстленд обладал значительными знаниями в области полировки, будучи в собственном бизнесе в течение нескольких лет в Абердине, Шотландия. Он умер в 1872 году, и название фирмы было изменено на Маккензи и Паттерсон. Они вели обширный бизнес резки и полировки гранита до смерти г-на Маккензи в 1897 году. Вскоре после этого г-н Паттерсон отказался от производства, и завод был продан и снесен.
Когда они впервые начали полировку, цена за обработку составляла 3,50 доллара за квадратный фут и 3,00 - 4,00 доллара за фут линейного элемента лепных украшений. Используемый для шлифования материал был прибрежным песком, а турецкий наждак для заключительной обработки камня. Все режущие инструменты для полировальной работы должны быть прямые 8-срезанные. Процесс был медленным, и компания старалась держать его в секрете, позволяя только своим сотрудникам находиться внутри полировочной фабрики. Однако эти ограничения не увенчались успехом, примерно в 1872 или 1873 гг. Господа Черчилль и Хичкок построили небольшую полировальную мельницу... Цена на обычную полировку была снижена до 2,75 доллара за квадратный фут. Это сокращение расходов стимулировало бизнес, и в течение следующего десятилетия объем полированной работы быстро увеличивался, поэтому ряд фирм, участвующих в этом бизнесе, среди которых были Henry Barker & Sons, McDonnell & Sons, Frederick & Field, Murdock & Smith, Милн и Чалмерс, и братьев Барсуков.
С увеличением числа фирм, занимающихся полировкой, цены упали до одного доллара за фут, а затем произошло дальнейшее снижение до шестидесяти пяти центов за фут.
Примерно в то же время на рынок был выпущен улучшенный шлифовальный станок Wright & Sons of Montpelier. В продажу была введена охлажденная чугунная дробилка, но изобретатель наложил такие раздражающие ограничения на ее использование и почти непомерные затраты (свыше 12 центов за фунт) на статью, что, когда несколько месяцев спустя г-н Харрисон из Канады предложил охлажденное железо менее чем за половину американской цены, почти каждая фирма в бизнесе начала использовать канадский продукт, но вскоре обнаружила, что они несут ответственность за ущерб за нарушение американского патента.
Владельцы патента урегулировали большинство своих требований долгосрочными примечаниями, и по мере того, как срок действия патента истек, было выплачено лишь несколько банкнот.
До и включительно тридцать семь лет назад (1876 г и позже - Взор) единственным абразивом, используемым для распиливания или полировки камня, был морской песок. Это использовалось со старомодной тяжёлым приспособлением, одна рама пилы, размахивающая, как маятник, с веревками над верхней частью рамы на маленьких тягах, а на конце веревок тяжелые куски железа или камня, что позволило бы пильной раме опираться на камень с достаточным давлением, чтобы пильные диски могли заставлять песок проходить камень с умеренной скоростью, причем песок выступал в качестве зуба для лезвия, когда лезвие входило в контакт с камнем.
Примерно тридцать семь лет назад Джон Харрисон, государственный подрядчик, отец фирмы Harrison Brothers, задумал использовать железные опилки вместо песка, в результате чего он обнаружил, что можно увеличить выход пилы до таких пропорций, которые гарантировали бы использование искусственного абразива вместо песка. Позже выяснилось, что с помощью старой системы прижимания было невозможно пройти камень так быстро, как это позволяло абразив. Это, в свою очередь, привело к обнаружению спиральных передач для распиловочных рамок, что заставило пилу проходить сквозь камень на любой скорости, желаемой оператору.
После нескольких лет тщательного эксперимента появилась чугунная дробь, запатентованная Джоном Харрисоном, - материал, сделанный исключительно для себя и на собственных каменных заводах. Однако вскоре общественность узнала о том, что искусственный абразив, который распиливался более чем в двадцать раз быстрее, чем когда-либо распиливали камень. Для этого материала поступали заказы со всех сторон, и в конце концов возникла необходимость создать завод для производства только дроби. Оглядываясь по сторонам, чтобы найти самый дешевый рынок металлов, было решено найти первый крупного завода в Мидлсбро, Англия, где было возможно получить сырье прямо с земли и производить дробь при минимальных затратах. Этот завод был основан в 1887 году, первый в своем роде в мире.
При изготовлении чугунной дроби было обнаружено, что, делая специальные калибры для распиловки, можно получить лучшие результаты для камня. Камнепильное оборудование сохраняло скорость ударов. Спустя много лет было обнаружено, что можно изготовить охлажденную стальную дробь, которая была названа производителем Harrison Brothers New Process Steel Shot. Этот материал отправлялся во все уголки земли, где обрабатывается камень, и он произвел революцию в распиловке и полировке гранита. Дальнейшие эксперименты приводят к производству так называемого алмазного песка или разрушенной новой технологической стальной дроби, которая имеет угловую форму. Она используется для распиливания мягких камней, таких как песчаник, известняк и для шлифовки поверхности терракоты, кирпича, стекла, оникса и т. д.
У «Братьев Харрисона» есть завод, занимающий площадь в одну четверть гектара, производящий новый процесс стальной дроби и алмазный песок, и они дают работу большому количеству мужчин. Специализируясь на этом конкретном направлении и являясь оригинальными производителями, они производят изделие, которое признано как высококачественное и которое выполняет на 35 процентов больше работы, чем любой другой абразив такого рода.
Генри Паркер и сыновья Кейп-Энн, в 1877 году, построили в своих каменных работах пильный станок, который был первым в Соединенных Штатах в постоянном использовании и предназначен для распиливания гранита с железными шариками.
Модемные полировальные установки - это отличное улучшение по сравнению с их предшественниками. Используются мощные мостовые краны, большие и тяжелые машины, которые используют кольца весом от 800 до 900 фунтов и с пропускной способностью более 25 футов в день, в то время как небольшие, но эффективные машины для мелкой работы также используются. В былые времена от шести до восьми квадратных футов шлифования для машины считалось хорошей работой дня, а рабочим выплачивалось около 22 центов в час. Сегодня тысячи квадратных метров камня ежедневно шлифуются, а рабочие получают сорок центов в час. Тогда все камни для полировки должны были быть хорошо зачищены, не менее 6 разрезов, но теперь требуется только грубая остроконечная работа. Также примечательно то, что, хотя использование песка и наждака было полностью прекращено, все же ничего не найдено, что заменит порошок шпатлевки или распыленный цинк и войлок для глянцевания или отделки камня. Очень мало улучшений было сделано в полировке молдинги по мощности. Маятник такой же, как старый, и цена высокая, около одного доллара на линейную ногу на члена. Очень маленькая формованная работа полируется и мало что обрабатывается, как правило, вручную.
Этот обычай полировки гранита - это возрождение или восстановление египетской системы украшения своего сиенита, столь же древнего, как и вечные пирамиды. Усовершенствования в этой отрасли благодаря машинам настолько снизили издержки, что сделать полированную работу более распространенной, чем раньше. Полированная поверхность намного красивее; Кроме того, он, как утверждается, более прочен, так как поверхность, таким образом, оказывается совершенно непроницаемой для дезинтегрирующих элементов и разрушительного воздействия времени, как это видно на красивых экземплярах полированного красного сиенита древнего Египта, которые все еще сохраняют Оригинальные польский и цвет неизменен.
Г-н Джозеф Ричардс из фирмы Ричардс и Манн изобрел в 1831 году буш или молоток колун. Название кустарникового молота было, очевидно, местным, как в Филадельфии и некоторых других местах, его называли топорным молотом, из нескольких маленьких осей (колунов), вставляемых в щеки прибора. С ней связано шесть, восемь, десять или более осей. Используемое количество зависит от тонкости, с которой ремесленник желает выделывать камень. Этот полезный инструмент впервые был сделан Ричардсом, сплошным или сплошным целым, для которого он получил патент. С тех пор были сделаны улучшения, построенные в нескольких частях. Г-н Ричардс также, как говорят, был первым, кто предложил, построил и использовал лунку Луиса, которая теперь применяется для целей взрыва. Машина для обогащения камня, запатентованная Чарльзом Уилсоном из Нью-Йорка, была создана в Куинси в 1853 году Ричардсом, Мунн и Ко. Не доказав успеха, он был удален на карьеры Рокпорт на мысе Энн, где использовался только один сезон По Баркер, Райт и Ко, с более или менее успешным. Говорят, что эта система используется в Абердине, Шотландия. Каменная строгально-втулочная машина McDonald была запатентована и изготовлена компанией McDonald Stone Planing Machine Company в Бостоне в 1879 году. Эта машина имеет плоскость 7 футов 6 дюймов в ширину, но камень на ширине 10 футов 6 дюймов можно пропустить на каретке, каретку, перемещающуюся при строгании камня 7 футов 6 дюймов в ширину со скоростью 3 дюйма в минуту или 15 футов в час, но может работать, если не строгаете на высокой скорости 30 футов в минуту. Средняя скорость строгального станка составляет 25 оборотов в минуту. Строгальный станок будет снимать стружку глубиной один дюйм, строгая поверхность по всей ширине машины 7 футов 6 дюймов, и с каретой, движущейся со скоростью 15 футов в час, обрабатывая поверхность более чем квадратный метр камня в час. Втулочная машина, которая крепится к раме и проходит непосредственно позади строгального станка, может использоваться, когда требуется втулка.
Старый метод высверливания и дробеструйной обработки, ранее примененный ко всем классам горных пород, теперь устранен, за исключением очень сложных и жестких материалов, или там, где, как в случае с пороками ловушки, материал должен использоваться только Для дорожного материала.
Даже когда при сверлении (бурении) или взрывных работах прибегают к нему, обычай бурить ряд отверстий в линии, вдоль которой желательно, чтобы камень сломался; эти отверстия затем заряжаются легко и запускаются одновременно. Таким образом, сила взрыва доставляется по значительной поверхности, и опасность разрушения материала через внезапная банка сводится к минимуму. Этот процесс в основном ограничивается гранитными породами, которые слишком сложно добывать с помощью каналообразующих машин..." https://archive.org/details/hi...
Надеюсь, что вы обратили внимание на год появления новой технологии обработки гранита - 1876. Как известно, Исаакиевский собор и Александровская колонна возводились несколькими десятками лет ранее этой даты. Так что, изпользовать при изготовлении указанных колонн из гранита новую технологию и технику в Петербурге не могли.
Что касается токарного станка для изготовления колонн такого веса, выяснились следующие подробности его применения.
"...Интересная особенность проявилась в процессе современных камне-строительных работах, что старомодная ручная обработка камня иногда лучше, чем машинная. Это выявилось при изготовлении огромных гранитных колонн, украшающих собор Святого Иоанна Богослова в Нью-Йорке. Было запланировано, что эти колонны должны быть самыми большими целыми колоннами из гранитных монолитов - 8 цилиндров, каждый по 51 футу в высоту и 6 футов в диаметре.
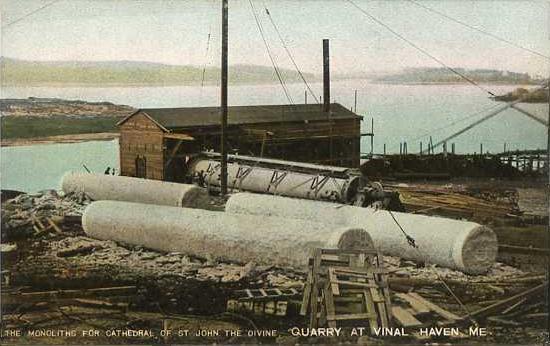
Они были, соответственно, добыты на шельфе с карьеров на острове Фокс, штат Мэн, и подготовились к отделке в гигантском токарном станке и успешно обработаны до нужных размеров.
«Какая великая вещь - токарный станок», - сказал бригадир, когда он осмотрел массивную колонну, ... «Мы бы на протяжении нескольких дней работали с дюжиной мужчин с ручным инструментом».
Но когда рабочие вернулись утром, они обнаружили, что одетый столб раскололся поперечно и разрушен. Второй столбец был повернут и также аккуратно извлечен из токарного станка. Ночью сторож услышал громкий треск, и, осмотрев, обнаружил, что второй столб раскололся.
«Гм!» Заметил мастер, утром, - «токарных станков не так много в конце концов».
Был сделан вывод о том, что огромные размеры и вес колонн, удерживаемых на токарном станке всего лишь в двух поворотных точках, представляли собой слишком большую нагрузку на молекулы камня, что приводило к практическому разрушению колонн даже после завершения работы по повороту и снятию напряжения. Поэтому было сочтено необходимым разрезать монолиты на две части, прежде чем поместить их в токарный станок. Если бы колонны были обрабатываемы вручную, то не было бы и речи об их растрескивании; С другой стороны, стоимость работы была бы значительно увеличена..."
Източник:

Надеюсь, что вы заметили, сколько бы потребовалось каменотёсов для ручной обработки колонн: около 13 человек выполнили бы эту работу за несколько дней.
(тема будет продолжена)
Предыдущие статьи по теме:
1 - https://cont.ws/@efiere/302828
2 - https://cont.ws/@metafor/59007...
3 - https://cont.ws/@metafor/59137...
Оценили 26 человек
48 кармы