Добрый день, КОНТ! Продолжаем знакомиться с людьми работающими на заводах КАМАЗа. Сегодня речь пойдет об реинжиниринге литейного производства.
Литейный завод «КАМАЗа» – это специализированное предприятие с полным технологическим циклом изготовления литейной оснастки и отливок. Как и другие подразделения компании, литейный был включён в масштабный проект реинжиниринга производства. Директор завода Эдуард Панфилов рассказал, как благодаря его реализации улучшаются условия труда, снижаются затраты и напряжённость работы, повышается качество выпускаемой продукции.
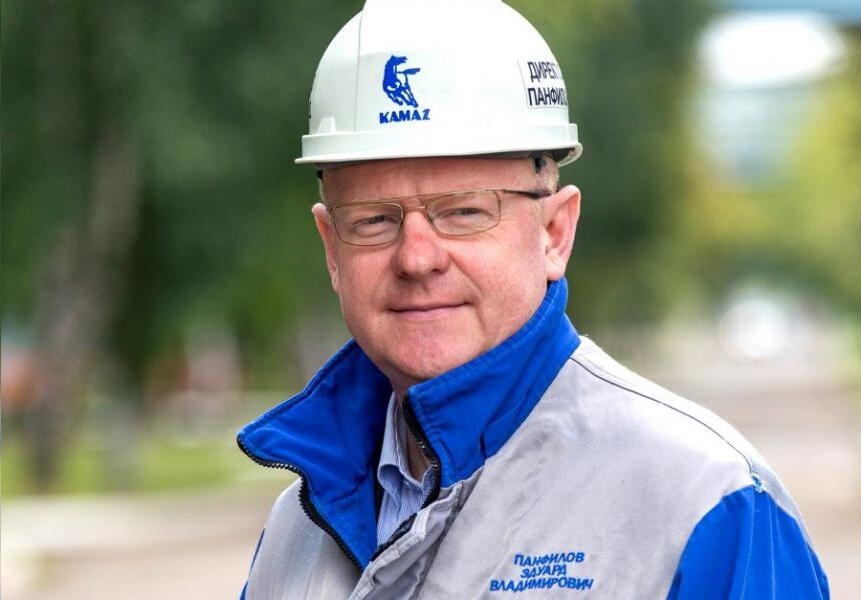
Большой реинжиниринг продолжается
За последние полтора-два года на литейном заводе внедрено несколько проектов. В рамках очередной фазы в 2020 году был смонтирован и запущен комплекс GARANT-Filter для фильтрации воздуха от плавильной печи Otto Junker. Это позволило улучшить условия труда на рабочих местах плавильщиков, снизить затраты на энергоносители и обслуживание фильтров на 4 млн рублей в месяц.
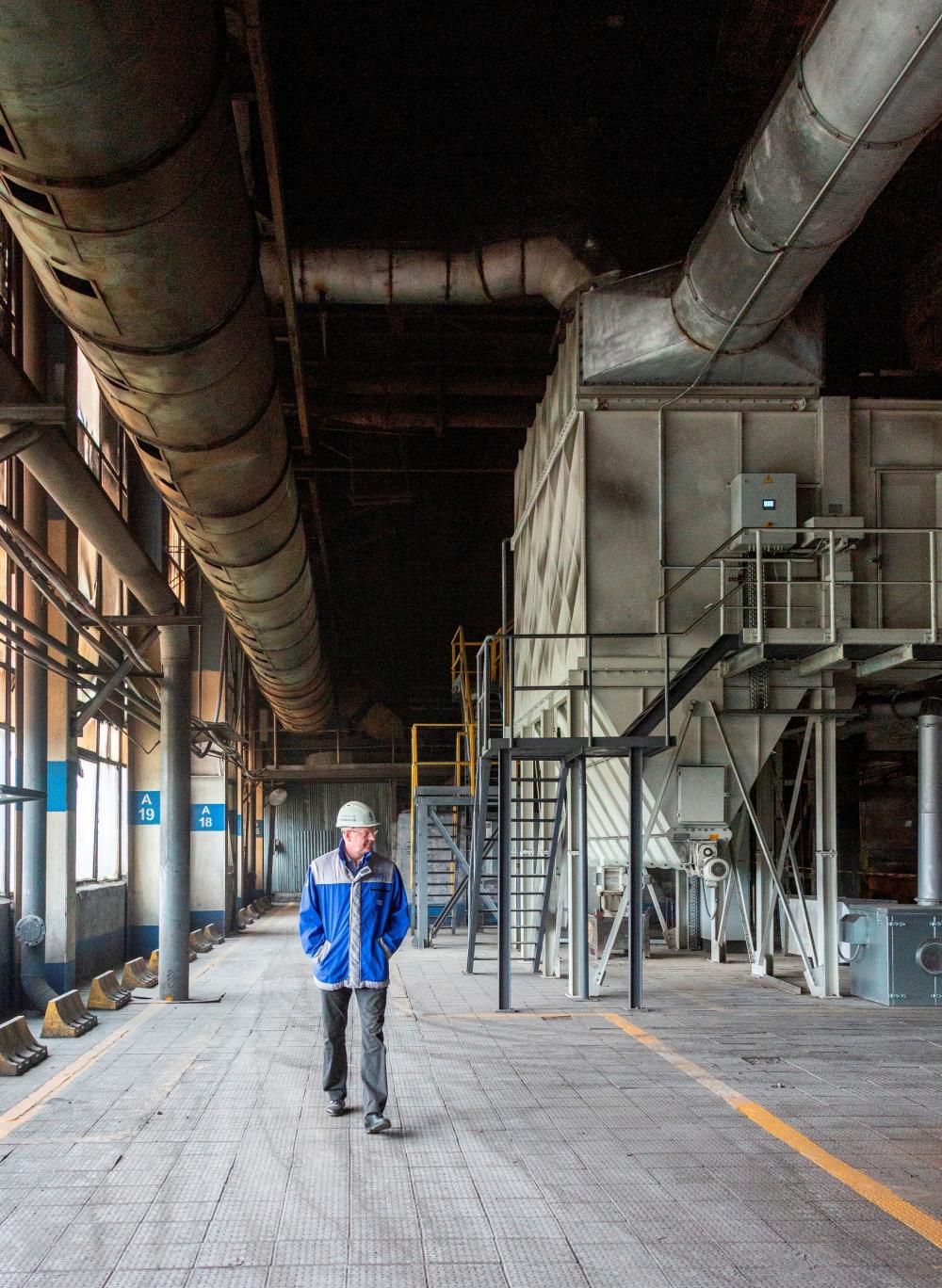
Разница между новой системой фильтрации и имеющейся вытяжной вентиляционной системой «Биг-Хауз» очевидна. Во-первых, уровень шума, который издаёт GARANT-Filter, – 70 дБ. Для примера: такое значение позволяет разговаривать, не напрягая голосовые связки. Во-вторых, за один час фильтры способны очистить до 60 тыс. кубометров воздуха от частиц оксидов железа и цинка, которые идут от печей. В-третьих, сама установка достаточно компактна и легко встраивается в производственные площади. В ближайшее время будет рассмотрен вопрос о закупке и установке ещё нескольких таких систем.
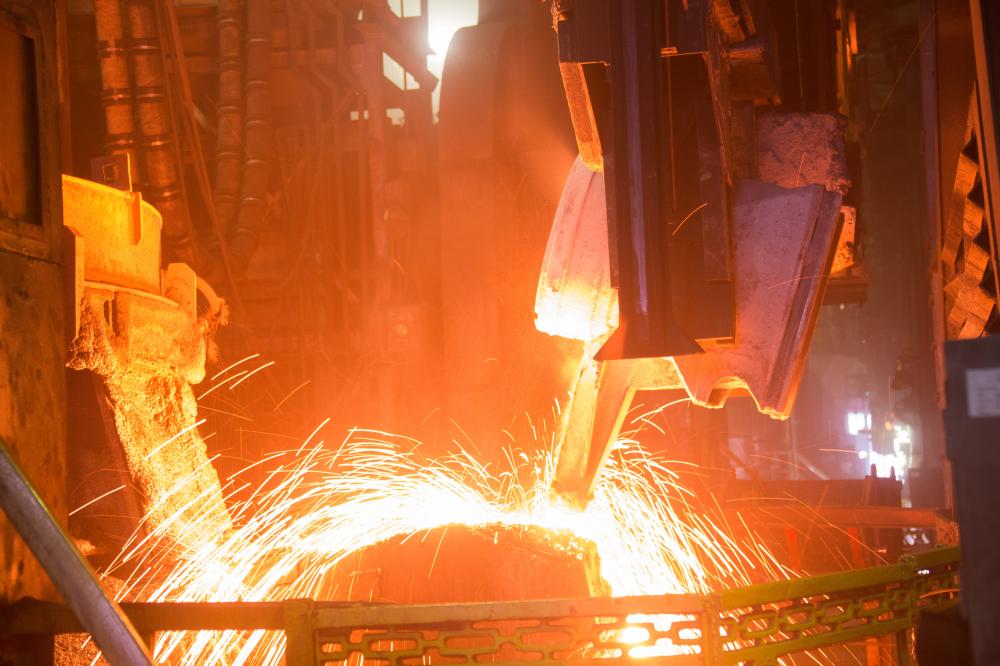
В 2020–2021 годах планируется замена трёх 75-тонных электродуговых печей на 50-тонные индукционные канальные печи. Если привести сравнение, то это как чёрно-белый телевизор с лупой из 60-х годов прошлого века против сегодняшних плазменных панелей. Индукционные печи работают бесшумно – уровень всего 40 дБ, угар снижен в 20 раз относительно электродуговых печей. Следовательно, потребуется меньшая вытяжка для фильтрации воздуха.
Модернизация линии-кормилицы
Второй серьёзный проект, который был начат два года назад и сегодня фактически реализован, – модернизация одной из наших старейших автоматических формовочных линий СПО-1. На ней производятся блоки цилиндров для двигателей КАМАЗ, в том числе и для нового рядного Р6. Это линия-кормилица для всего «КАМАЗа». Подобной модернизации никогда не было в масштабах всей России. Силами подрядчика, российской компании «Сиблитмаш», заменены новейшая система управления Siemens, четыре угловых механизма формовочной линии, модернизирована система гидравлики. Если раньше на линии было 11 гидростанций, то осталось только две. Это говорит о многом: улучшили условия труда, снизили расход гидрожидкости и количество брака, повысили производительность оборудования.
Как снизить напряжённость труда
В 2021 году ожидается серьёзная модернизация двух линий – HWS1 и HWS2 – в формовочном цехе производства чугунного литья. Планируется произвести полный капитальный ремонт и поузловую замену наиболее важных механизмов линий. Это позволит на 20% снизить напряжённость труда обслуживающего персонала, на 15% – затраты на ремонт и обслуживание. При этом производительность вырастет на 15%.
В термообрубном отделении планируем поставить шесть автоматических станков для зачистки отливок. Один такой станок заменяет 10 наждачников. Очевидно, работа наждачников облегчится, и мы выведем их из вредных и опасных условий труда.
Литьё под низким давлением – наша перспектива
Грандиозная модернизация коснётся и производства цветного литья. В 2020 году было принято решение сконцентрироваться на развитии литья под низким давлением. Дело в том, что сейчас в России никто, кроме «КАМАЗа», не производит такого количества алюминиевого литья под низким давлением именно для автомобильной промышленности. Я полагаю, что в ближайшей перспективе мы сохраним это лидерство, кроме того, усилим его более сложной номенклатурой: отливками блоков цилиндров, головок блоков цилиндров, трансмиссии для спецавтомобилей. И тогда мы сможем называться центром компетенций в этой области на территории РФ.
Экономия из воздуха. Сжатого
Отдельно хочется сказать про проект повышения эффективности за счёт снижения потребления сжатого воздуха. У нас очень разветвлённая сеть трасс сжатого воздуха, её длина более 70 км. И очевидно, что на всём протяжении сетей существуют значительные потери. За последние два года мы очень серьёзно поработали над этой проблемой, снизив потери почти на 20 млн рублей. В этом году уже имеем экономический эффект порядка трёх миллионов. Чтобы ещё уменьшить эти затраты, работаем над задачей перемещения компрессорных станций ближе к потребляющему сжатый воздух оборудованию.
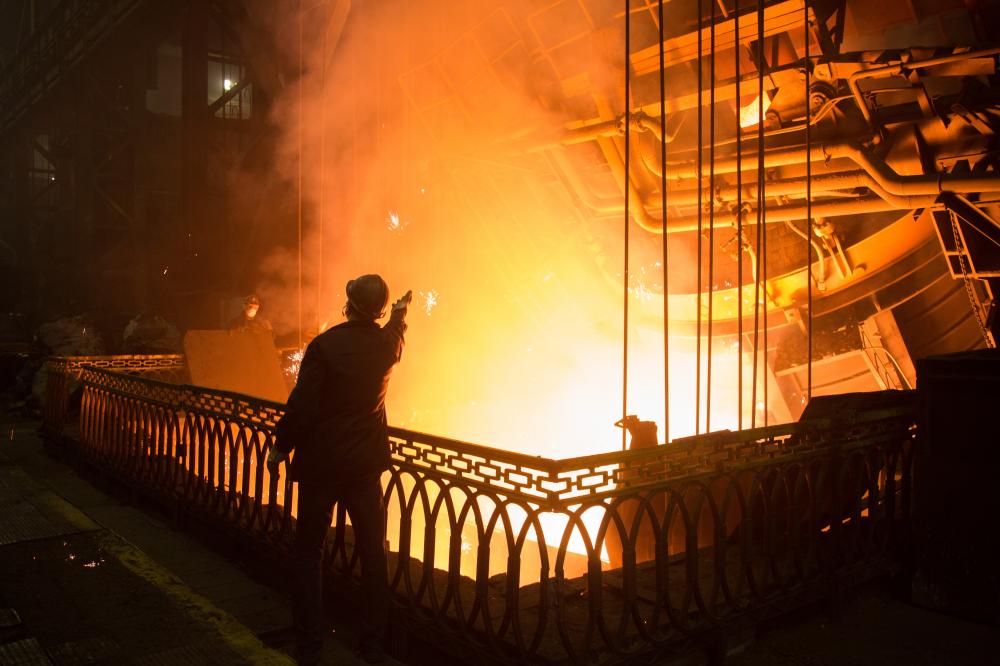
Литейное производство – одно из самых сложных и опасных на «КАМАЗе»
Блиц-опрос
Привык, что жизнь ставит сложные задачи. Иногда кажется, что без них жить уже невозможно. Бывает скучно, когда на горизонте нет ничего, за что можно побороться. Если нет задач, их нужно искать.
Выхожу в производство по нескольку раз в день. Очень важно встречаться со сталеварами, плавильщиками, обрубщиками и представителями других специальностей. При разговоре с ними выявляются проблемы и важные для людей вопросы, идёт определённый съём информации.
Современный руководитель должен быть прагматиком на 100%. Обязательно иметь профессиональное образование и быть уверенным специалистом в своей сфере. Обладать общечеловеческими качествами, например, уважать людей. А самому уважение можно завоевать только делом и постоянно подтверждать. Не так, что один раз и на всю жизнь, а постоянно!
Я могу быть разным: иногда спокойным, иногда вспыльчивым. Надо ловить импульсы ситуации, понимать, как она должна переломиться, и вести себя надо соответственно. Нужно быть артистом в хорошем смысле этого слова.
Пример для меня – мой отец. Он был очень хорошим технарём, добрым, с горячим сердцем. Всё делал не спеша, и всё у него получалось. Думаю, мой отец гордился бы тем, что я, пройдя по определённым ступеням, стал директором завода.
Главное в жизни – сама жизнь и понимание того, что ты приносишь пользу окружающим. Нельзя односложно сказать: важна работа, важна семья или ещё что-то. Нужно жить так, чтобы ни минуты не проходило даром.
Семья смирилась с моей вечной занятостью. Были разные ситуации, на производстве сутками пропадал. Но главное – дать родным позывной, что с тобой всё в порядке. Нужно понимать, что тебя ждут, за тебя переживают.
Директор должен быть всегда на связи. Иногда думаешь: пойду в корпоративный отпуск, отдохну, пока на заводе проводят капремонт оборудования. А потом понимаешь, что всё-таки надо отслеживать, как он идёт, производство опасное. Но если случается неделя отпуска, никогда не отключаю телефон.
Хорошая новость
Литейный завод выиграл тендер на производство автокомпонентов для автомобиля «Аурус». Сейчас идёт подготовка к закупке оборудования под этот проект. Запуск запланирован на 2022 год. Будет освоено 32 наименования отливок.
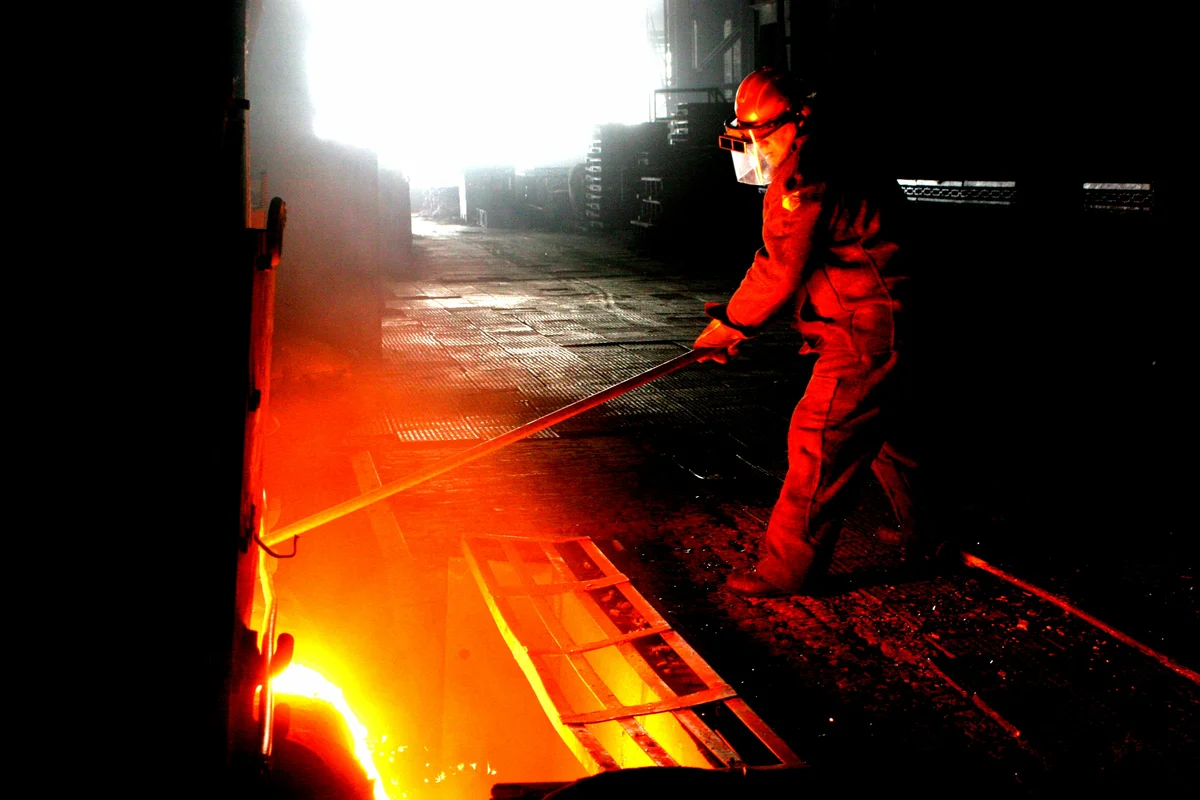
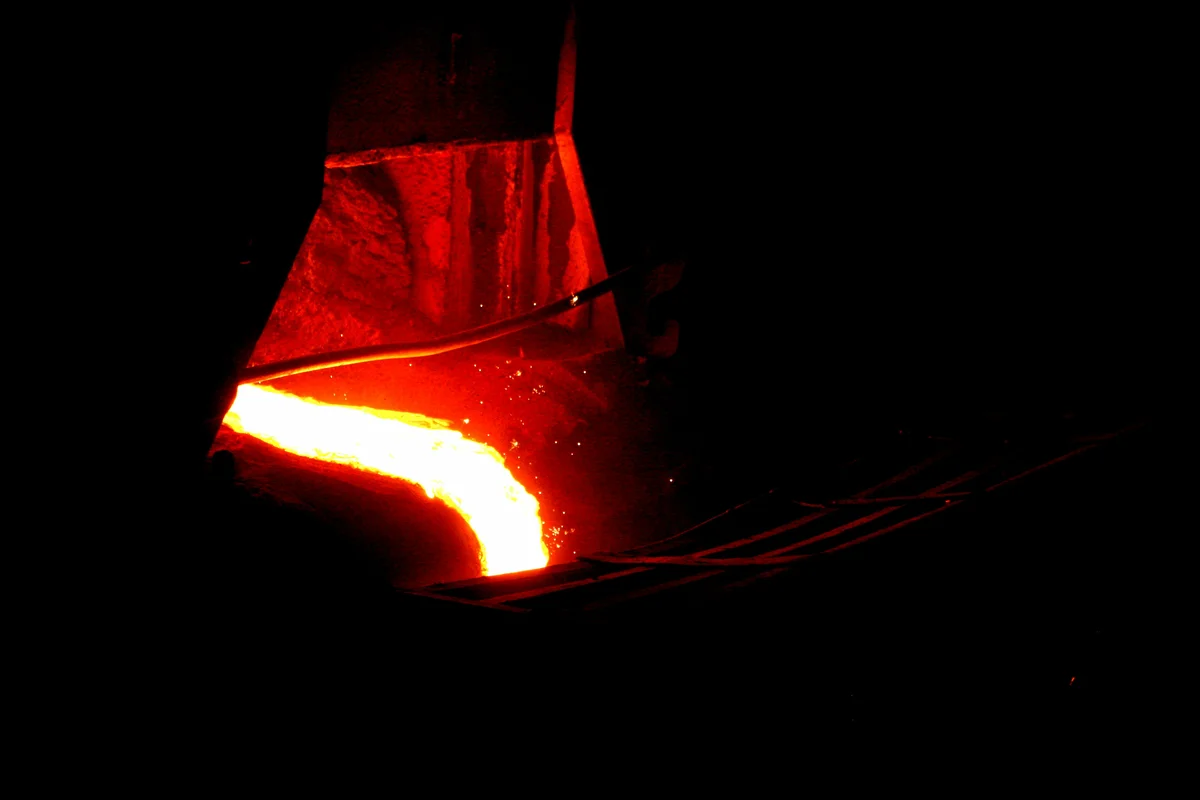




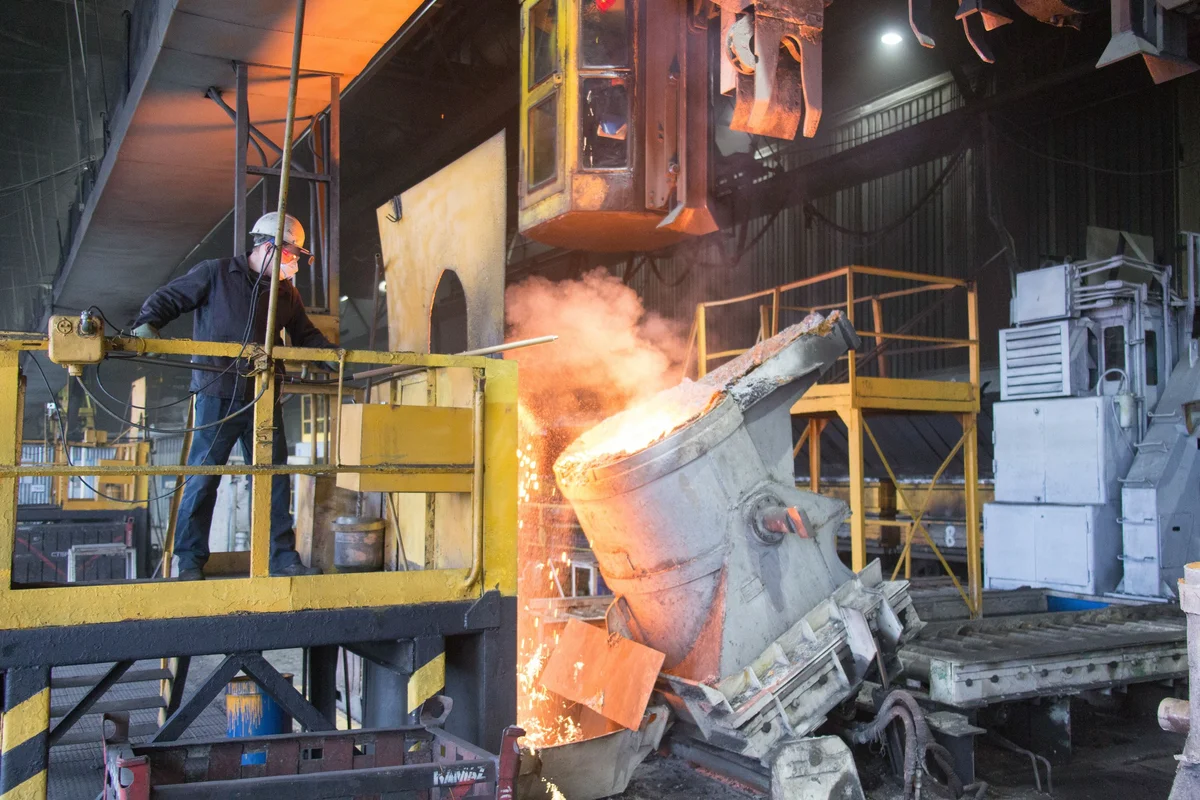
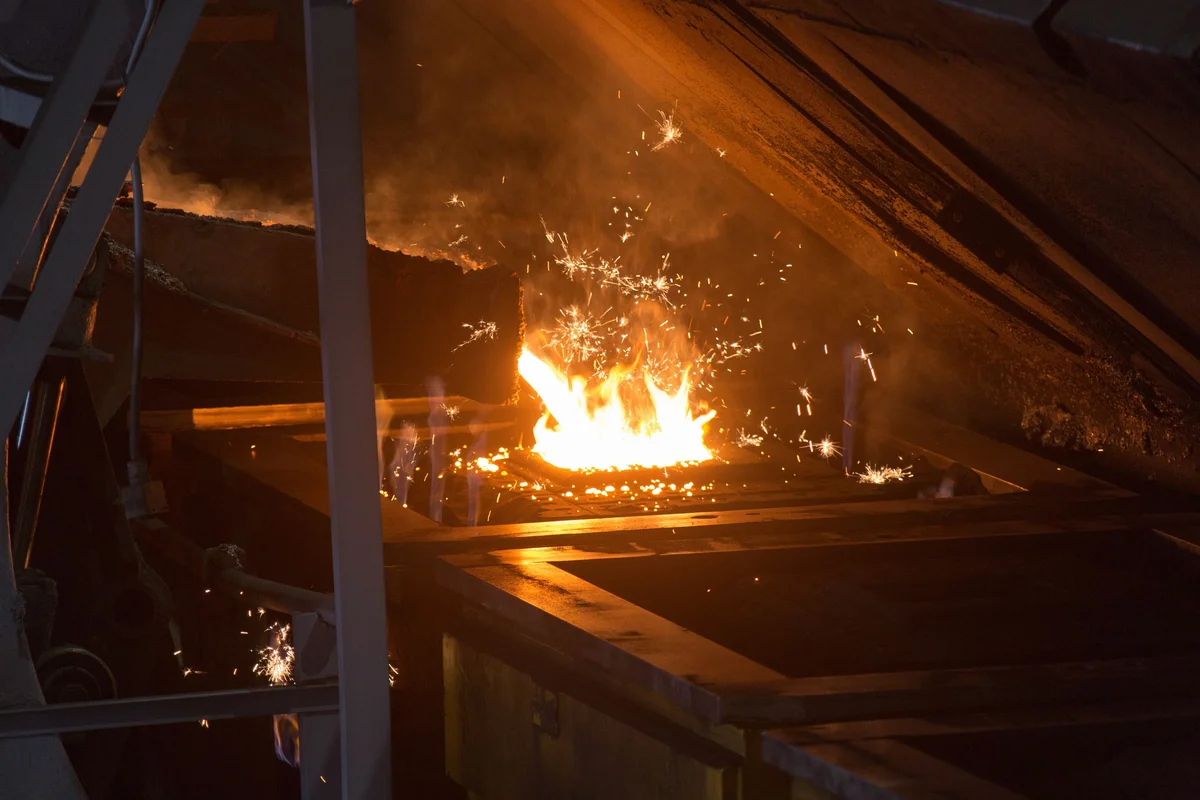
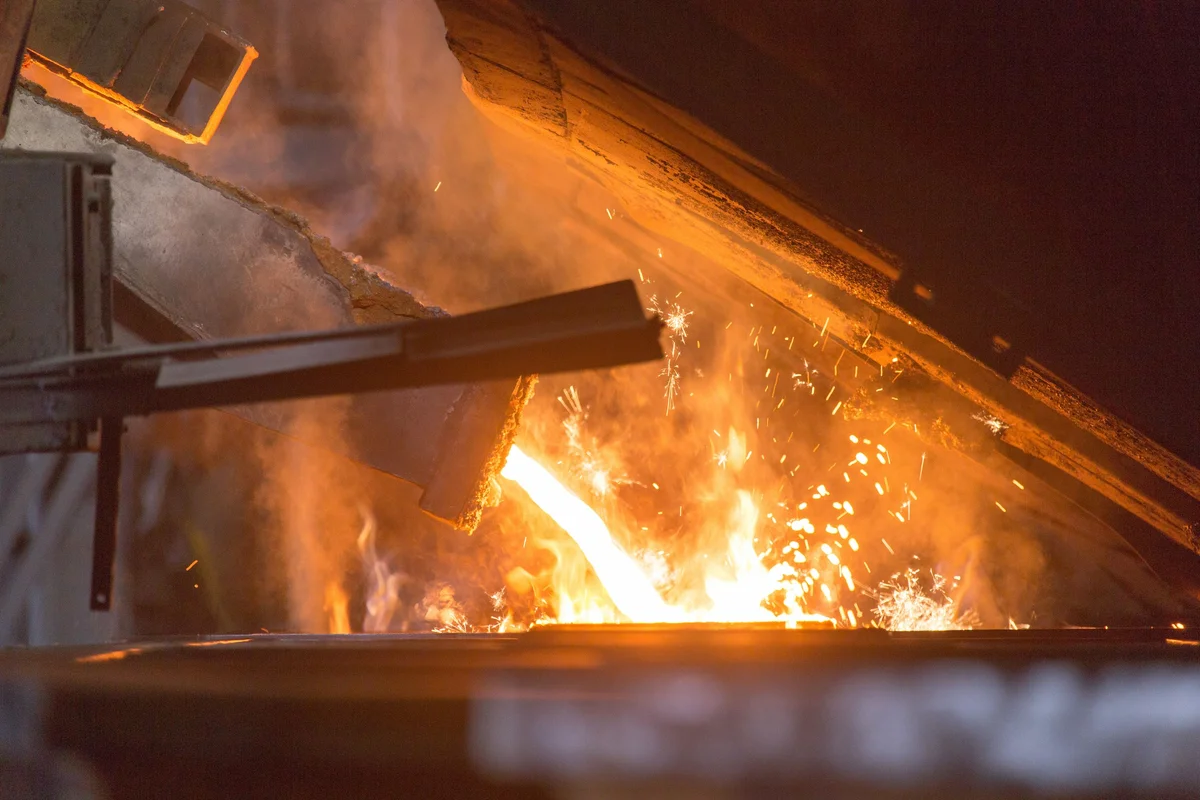
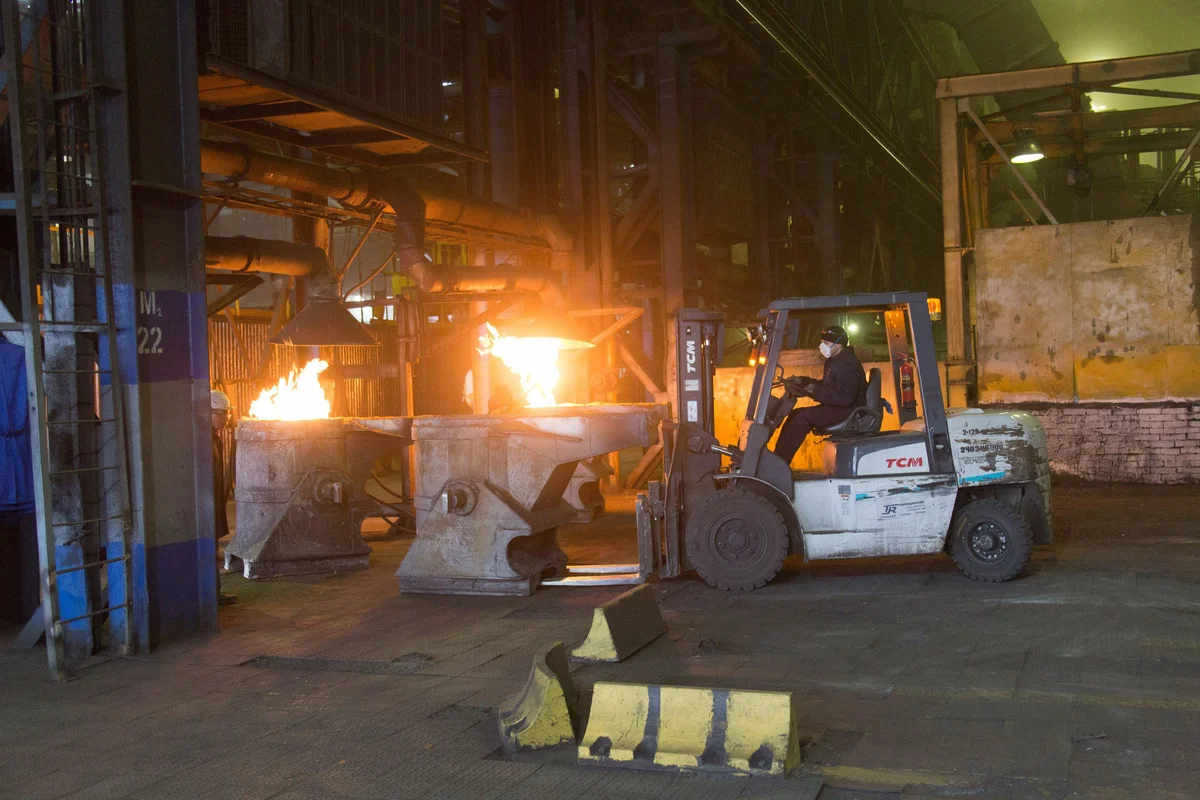
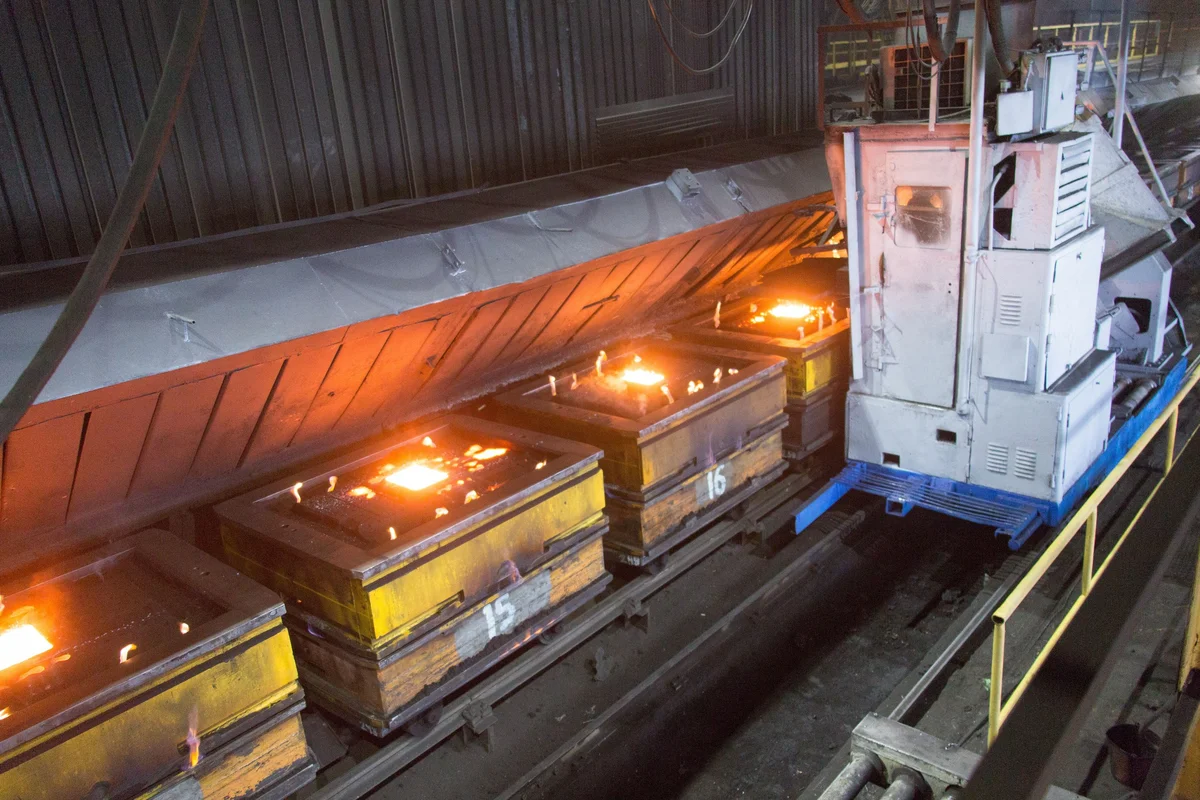
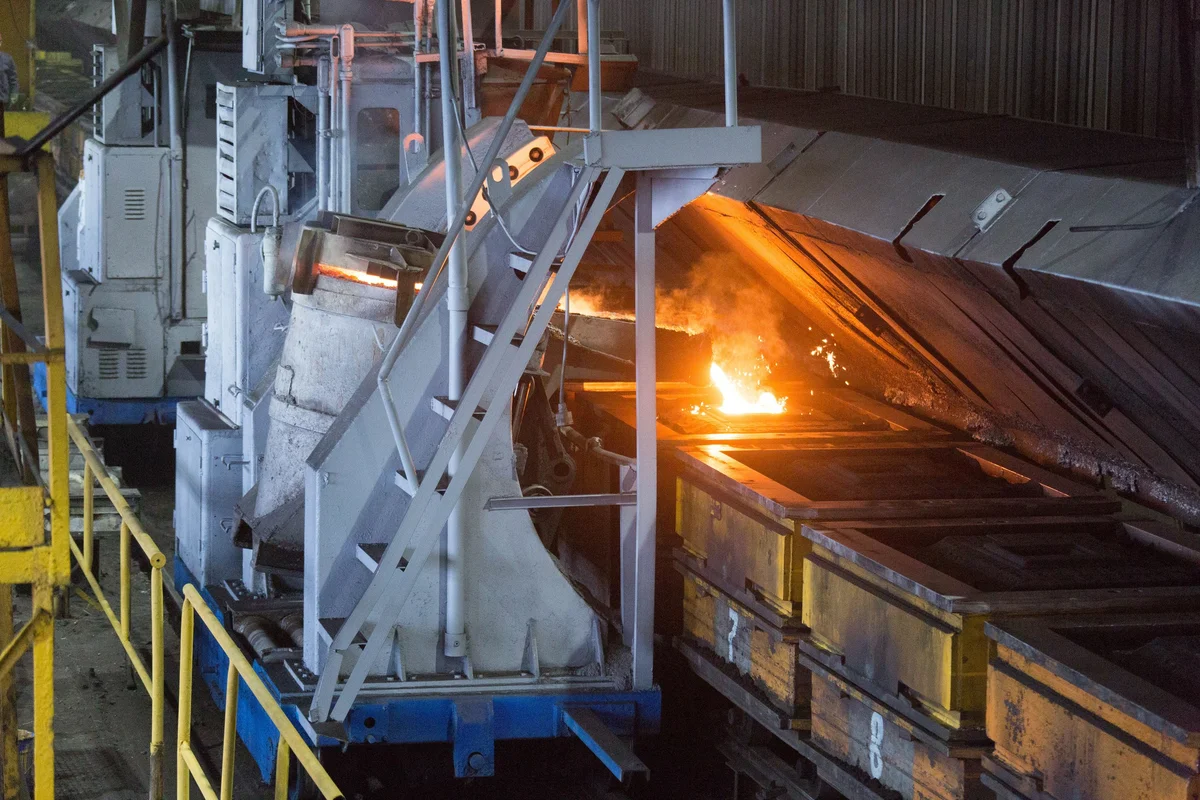
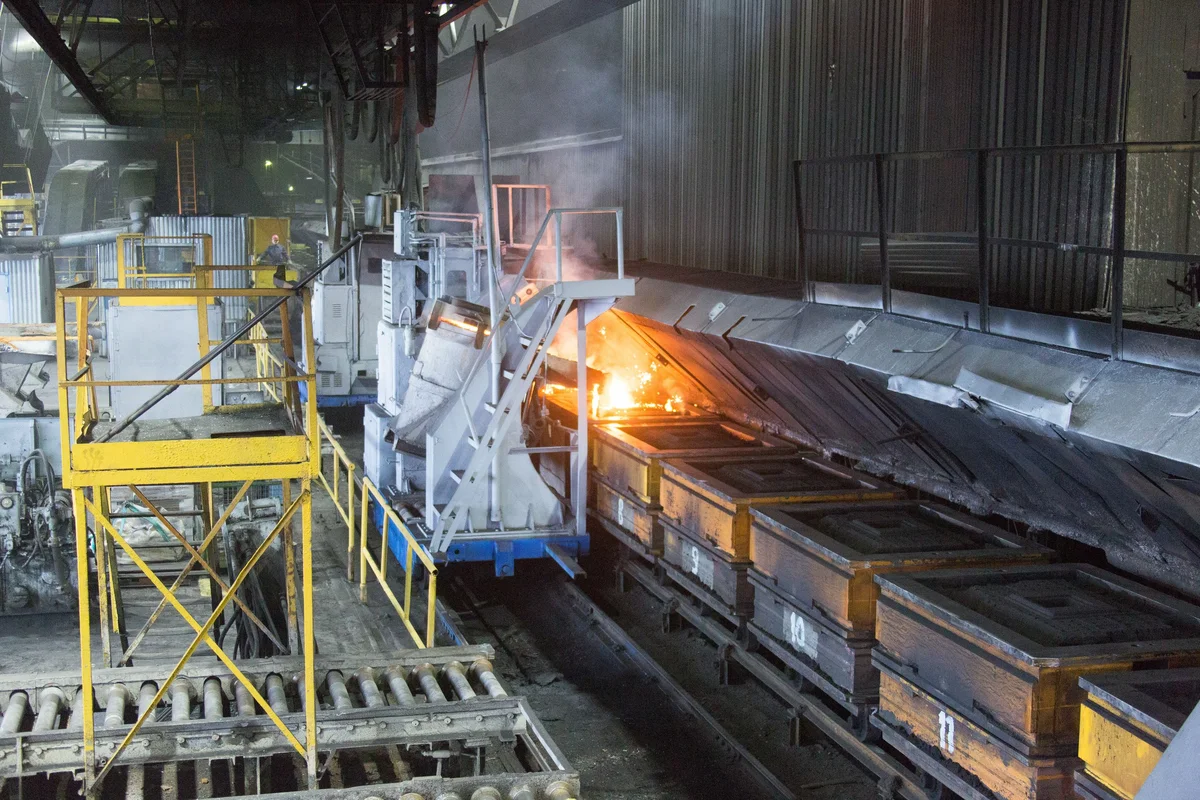
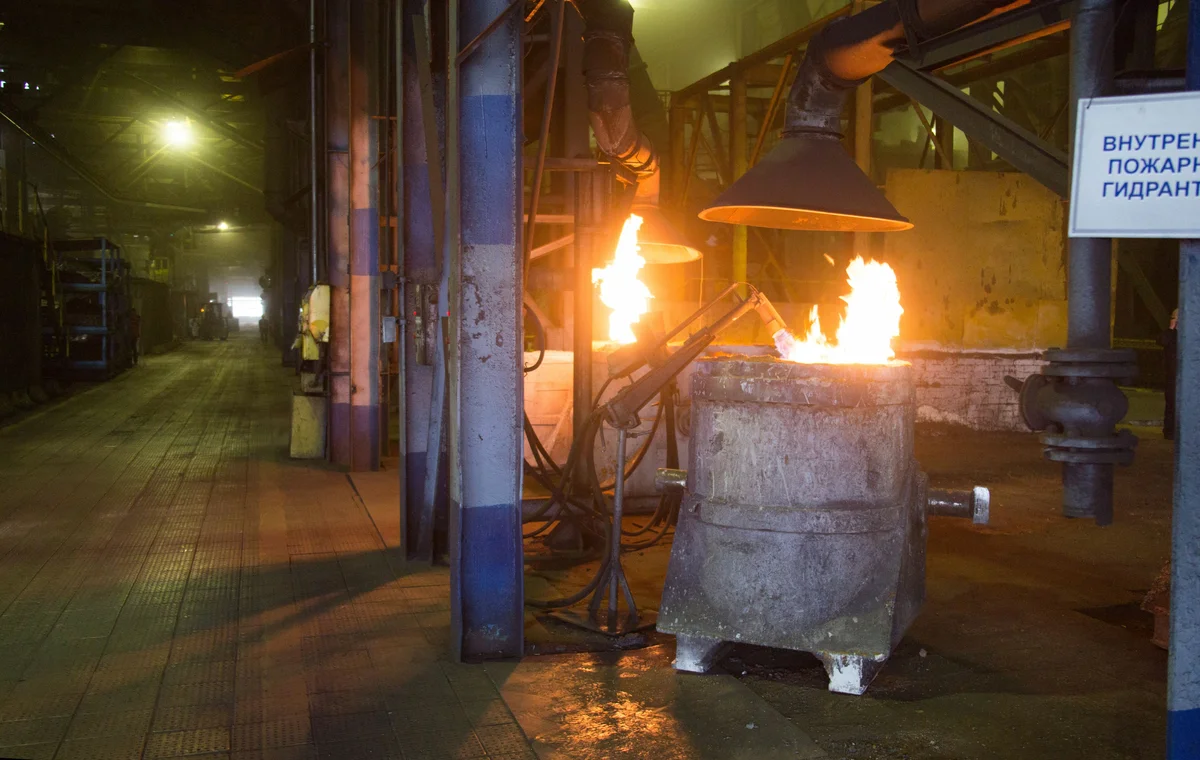

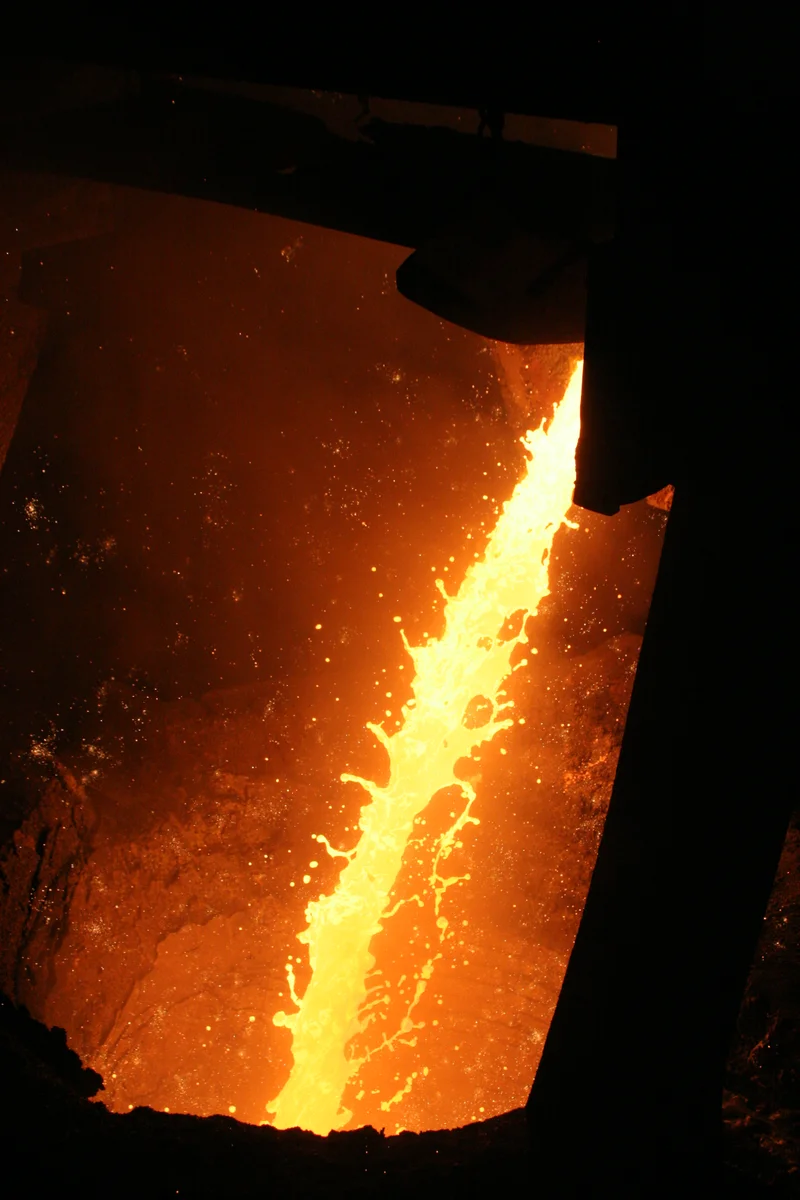
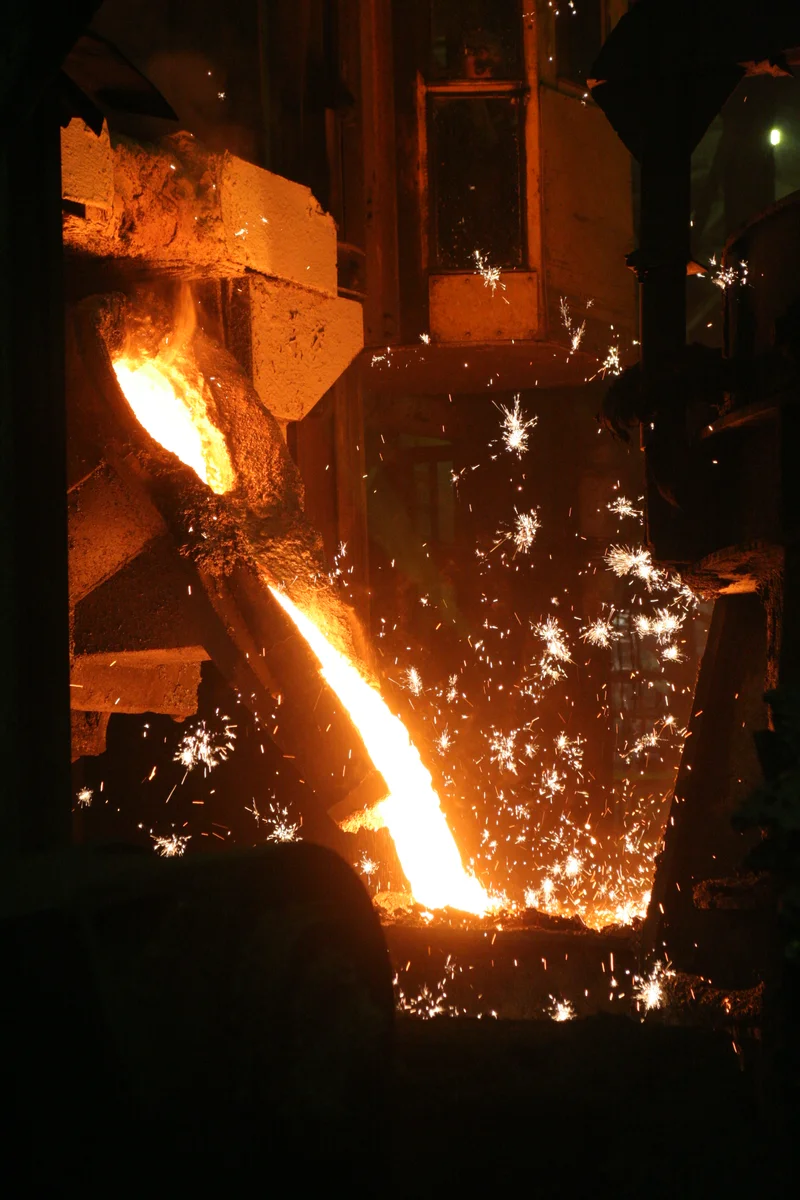
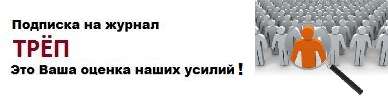
Оценили 10 человек
24 кармы